A criação da fibra de vidro e o desenvolvimentos dos plásticos durante a Segunda Guerra Mundial foi o que permitiu a construção da primeira estrutura em materiais compostos que foi o veleiro feito pelo engenheiro Ray Greene no ano de 1942.
A história dos materiais compostos foi mais uma vez revolucionada na década de 1960 com as fibras de carbono, cuja criação se iniciou no século XIX durante o desenvolvimento das lâmpadas incandescentes, muito antes de a humanidade buscar materiais de reforço para plásticos termofixos.
O princípio das lâmpadas incandescentes é transformar energia elétrica em energia luminosa através do efeito Joule, por meio do aquecimento de um filamento em uma ampola de vidro onde havia sido formado vácuo. Sem a presença de oxigênio, chamas não eram iniciadas e o filamento se tornava incandescente ao ser aquecido, emitindo luz visível ao olho humano.
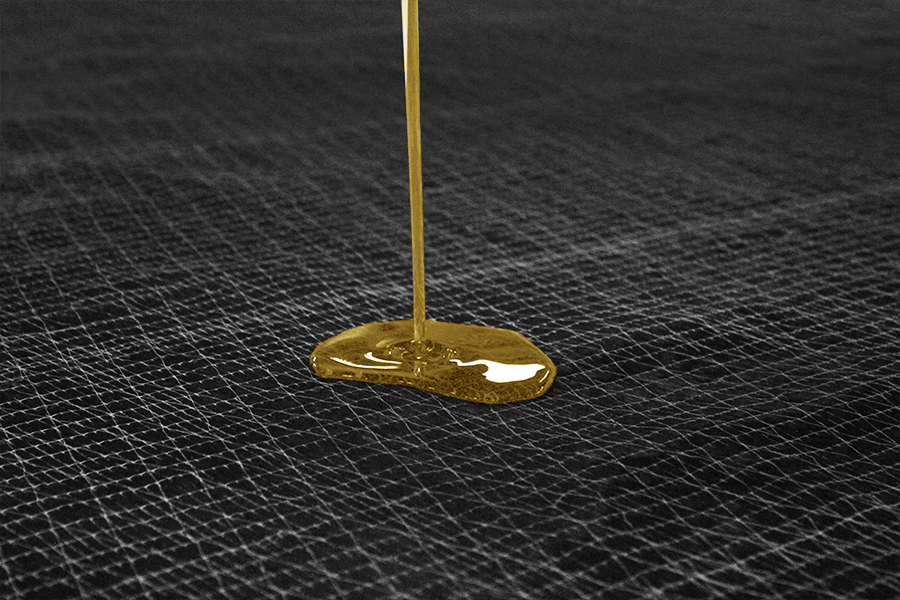
O material que forma esse filamento é o que determina a intensidade e duração da luminosidade. Quanto maior a resistência elétrica e ponto de fusão do material, mais intensa e durável é a luminosidade que ele é capaz de produzir. Foi nesse contexto eu os inventores Sir Joseph Wilson Swan e Thomas Edison criaram as primeiras versões das fibras de carbono, fabricadas a partir da carbonização de algodão. Apesar do conceito revolucionário, o processo utilizado por eles era bastante ineficaz e produzia fibras com apenas 20% de carbono e quando o tungstênio se mostrou uma opção mais viável, as fibras de carbono foram abandonadas para essa aplicação.
As fibras de carbono a base de derivados do petróleo, como se conhece hoje, foram produzidas pela primeira vez por acidente em um laboratório em Ohio, quando Roger Bacon tentava determinar o ponto triplo do carbono aquecendo filamentos de rayon em argônio.
O processo criado por Bacon continuava sendo extremamente ineficiente e foi somente no início da década de 1960 que Akio Shindo, no Japão, conseguir sintetizar as fibras a partir de poliacrilonitrila (PAN) alcançando um teor de 55% de carbono em um processo que, pela primeira vez, era interessante também do ponto de vista econômico.
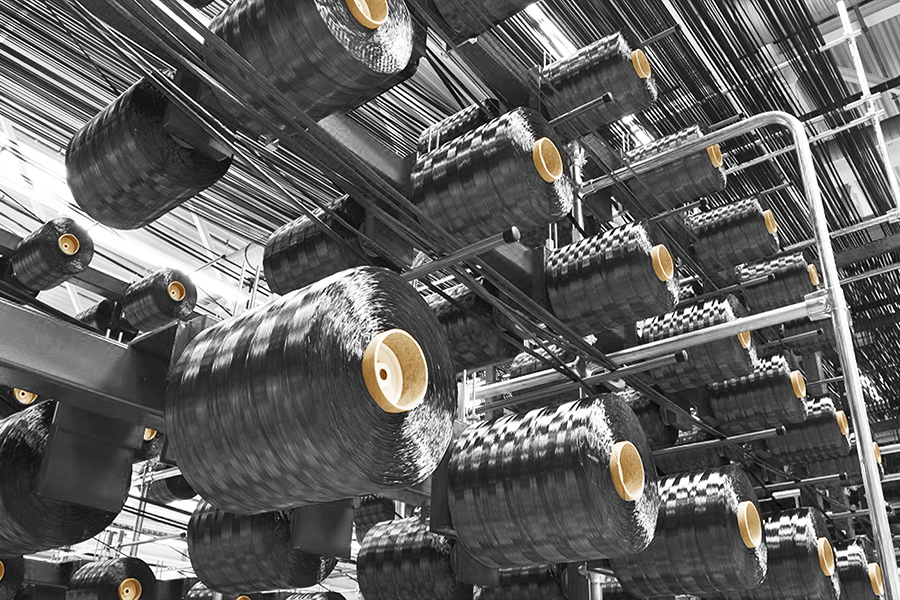
A partir de então, cientistas e empresas no mundo todo continuaram o desenvolvimento do material que começou a ser utilizado na indústria aeroespacial na década de 1970 para fabricação de foguetes, já que o suas propriedades mecânicas eram conservadas mesmo em altas temperaturas.
A partir da década de 1990, aeronaves comerciais como o Boeing 787 e os Airbus A350 e A380 também começaram a ser produzidos em larga escala com esses materiais. Atualmente, é possível produzir reforços em grandes volumes com até 95% de teor de carbono, que apresentam resistência à tração de até 4.000 MPa e módulos de elasticidade maiores que 400 GPa.
É muito comum que construtores amadores não relacionem a construção de embarcações com a fibra de carbono porque os custos são muito mais elevados do que a construção típica com fibras de vidro e resina poliéster. No entanto, esse material é cada vez mais utilizado em aplicações náuticas que requerem alta resistência e baixo peso.
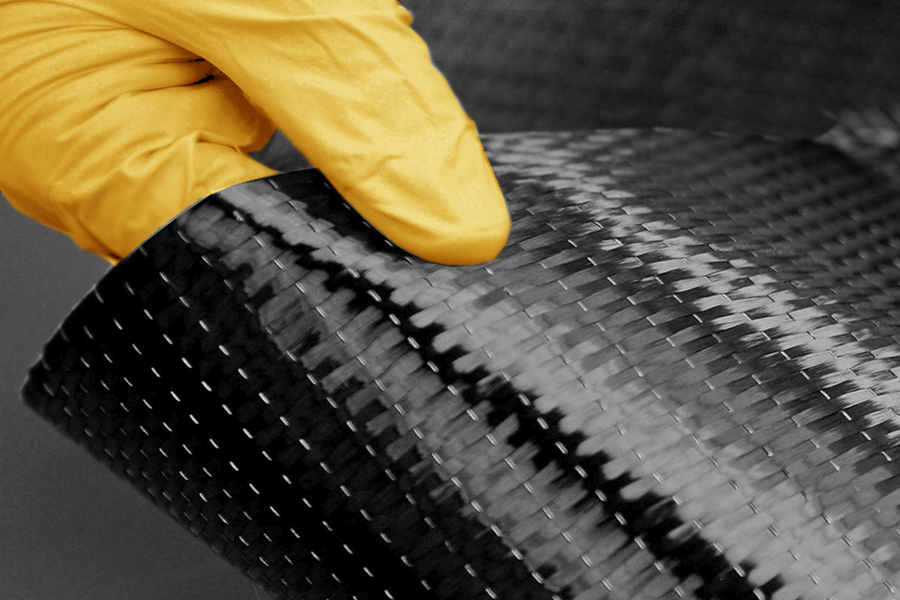
Além de integrar a construção de embarcações de regata desde a década de 1970, a fibra de carbono é muito utilizada em peças como hard top e casarias de embarcações de recreio, já que permitem a diminuição do peso dessas peças que ficam muito acima do centro da gravidade da embarcação, trazendo não só benefícios relacionados ao consumo de combustível durante a navegação como também à estabilidade transversal e conforto dos passageiros.
Com a popularização desse tipo de material, melhoria nos processos de manufatura e aumento na escala de produção, as fibras de carbono devem continuar a conquistar espaço nas mais diversas aplicações e é possível que sejam as substitutas naturais das fibras de vidro nas próximas décadas. Mesmo hoje, os construtores que buscam redução de peso devem avaliar as fibras de carbono como uma opção em seus projetos.
Carla Gooes disse:
Ouvi falar que as tais fibras do tipo 3k sao as melhores.. Isto é verdade?
Barracuda Composites disse:
Olá Carla,
Tecidos de fibra de carbono 3k são aqueles construídos com cabos de 3.000 filamentos. Eles proporcionam uma tecelagem bem “apertada” e com pouca porosidade, entretanto, não é isto que determina as maiores resistências ou rigidezes às fibras. O tipo mais comum de fibras de carbono (e mais econômicas) são as do tipo HS (alta resistência), mas existem várias outras categorias que têm resistência várias vezes maior, mas que também são bem mais caras. O problema de usar fibras de segunda qualidade e tecidos em teares antigos é que o material não fica homogêneo e tem muitos espaços vazios que vai apresentar um padrão cosmético de baixa qualidade
ISAK DIAMANTE (REPAIR SOLUTIONS ENGENHARIA LTDA) (www.repairsolutions.com.br) disse:
Prezados,
O artigo é bastante interessante e esclarecedor.
Somos aplicadores de FC em estruturas de concreto armado.
Gostaríamos de reproduzir este artigo, na íntegra, em nosso blog, citando é claro V.Sªs. como Fonte.
Neste caso, solicitamos formalmente sua autorização, ou não, para esta reprodução.
Obrigado.
Isak
Barracuda Composites disse:
Pode sim. Depois me passa o link da postagem!