O método de construção em strip planking em espuma PVC, desenvolvido pelo departamento de engenharia da Barracuda Advanced Composites, tem os mesmos fundamentos do método utilizando madeira, que foi um dos primeiros processos utilizados para construção amadora de barcos a vela e para a construção de modelos e moldes. Nas próximas semanas os posts do Blog de Manual de Construção de Barcos vão explorar esse método, começando aqui por uma visão geral que elucida todas as vantagens e etapas do processo, e depois abordando a confecção e posicionamento das cavernas e colocação das ripas de espuma.
Esse processo é ideal para construção de embarcações one-off com o mínimo de ferramentas possível e baixo investimento inicial. É mais indicado para barcos com grande parte de superfícies planas, mas é possível produzir superfícies com dupla curvatura. No método tradicional de strip planking, a madeira desempenha toda a função estrutural e as camadas de fibra aplicadas na parte externa do casco têm apenas função de proteção contra umidade. No strip planking em PVC, a espuma tem a mesma função estrutural de um material sandwich, provendo resistência à compressão e ao cisalhamento e garantindo um casco muito mais leve do que se tivesse sua estrutura construída em madeira.
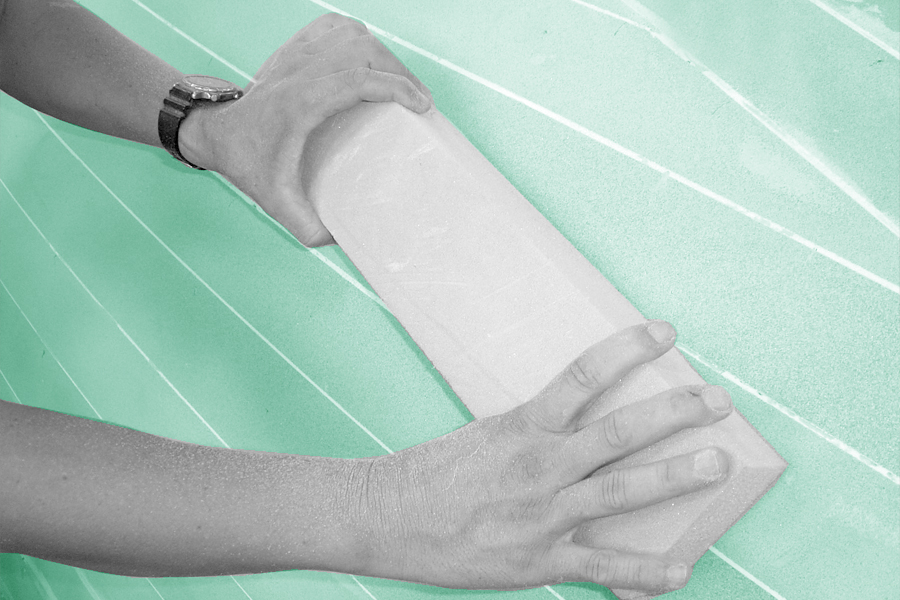
Além disso, barcos construídos com compostos sandwich tendem a não ter qualquer espécie de reforço longitudinal ou transversal, ou pelo menos não tanto quanto os usados em projetos de laminados sólidos e madeira. Barcos projetados e construídos em strip planking de madeira tendem ser dotados de uma série de cavernas transversais (90°) para compensar o uso de ripas longitudinais (0°) utilizadas no casco.
O processo de construção de strip planking em PVC começa com o posicionamento das cavernas, seguido do corte e posicionamento dos strips que são colados um nos outros com uma massa a base de resina poliéster. Depois disso, a superfície externa das espumas é preparada para laminação e acabamento antes do casco ser virado e laminação interna ser iniciada para a consolidação do painel sandwich.
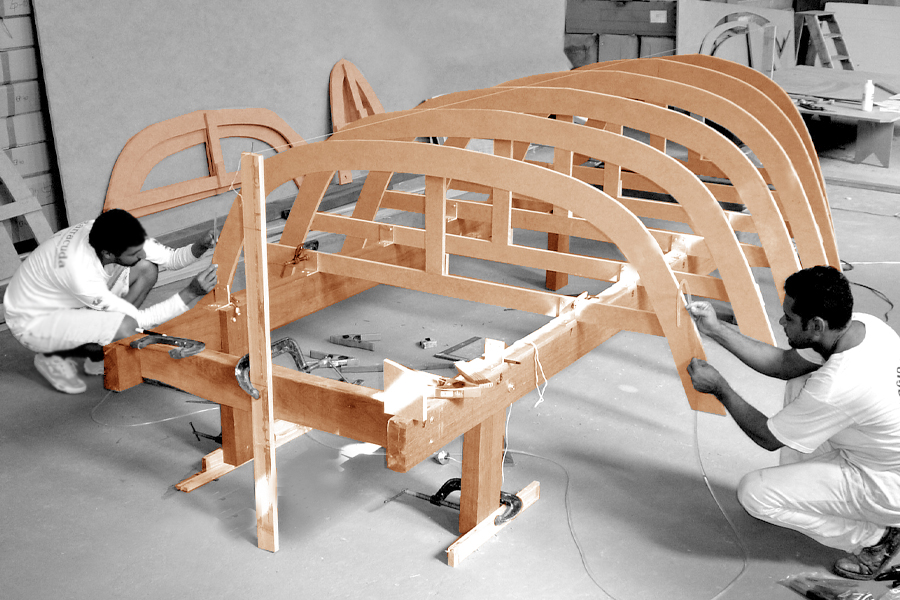
As espumas de PVC utilizadas para construção dos strips possuem densidades que variam entre 60 a 100 kg/m³ para a maioria dos projetos, com espessuras entre 10 e 50 mm, sendo que espessuras até 80 mm podem ser fornecidas caso seja necessário. As ripas de espuma devem ser cortadas com serra circular com uma boa lâmina e dispensam a usinagem de perfis macho e fêmea, como exigido paras as ripas de madeira, já que a colagem lateral é feita de topo, o que acaba reduzindo significativamente o trabalho de montagem.
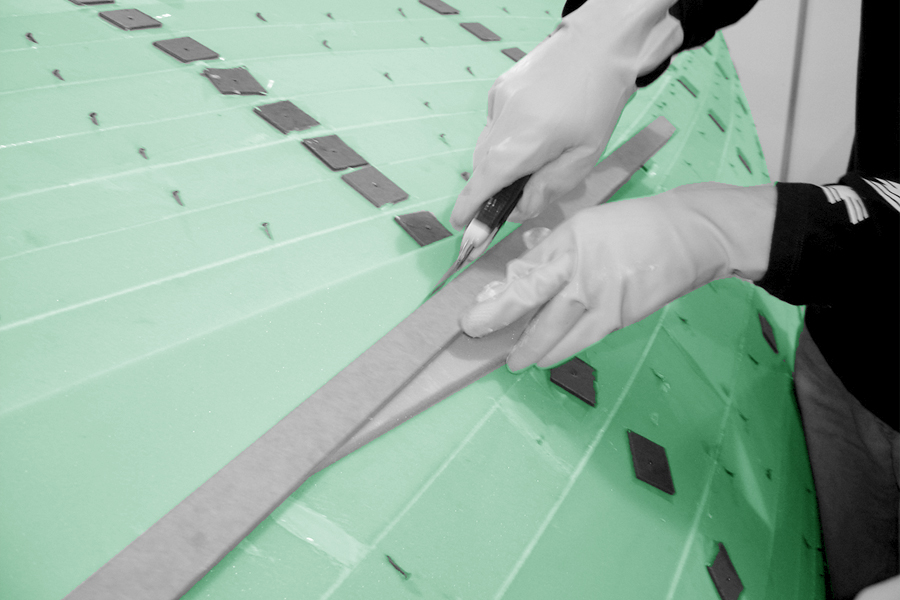
Inclusive, as ripas de madeira devem ter entre 20 e 25mm de largura e as de espuma podem variar entre 50 e 200mm, a depender do desenho das seções. A largura das ripas deve sempre ser maximizada de forma a diminuir o peso do adesivo, sendo inclusive possível que o construtor use placas com até 1200 mm de largura em barcos a motor com grandes superfícies planas.
As facilidades de montagem e colagem das ripas de PVC fazem com que seja possível diminuir consideravelmente o tempo de construção. Um barco pequeno de 25 pés pode ser montado em oito horas de trabalho, enquanto a construção em madeira levaria semana ou meses. Além disso, com o uso de madeira é obrigatório o uso de resina epoxy para a colagem das ripas e laminação da camada externa de fibras. A espuma PVC permite o uso de resina poliéster para laminação e colagem, o que diminui o custo e permite a construção de um laminado relativamente rígido.
O acabamento é outro aspecto onde o strip planking em PVC leva vantagem sobre o processo que utiliza madeira. Antes da laminação externa das camadas de fibra é necessário que a superfície do casco esteja perfeitamente aparelhada e por melhor que sejam as juntas de madeira, algum ajuste ainda será necessário. E lixar madeira é um processo muito mais trabalhoso do que lixar espuma rígida.
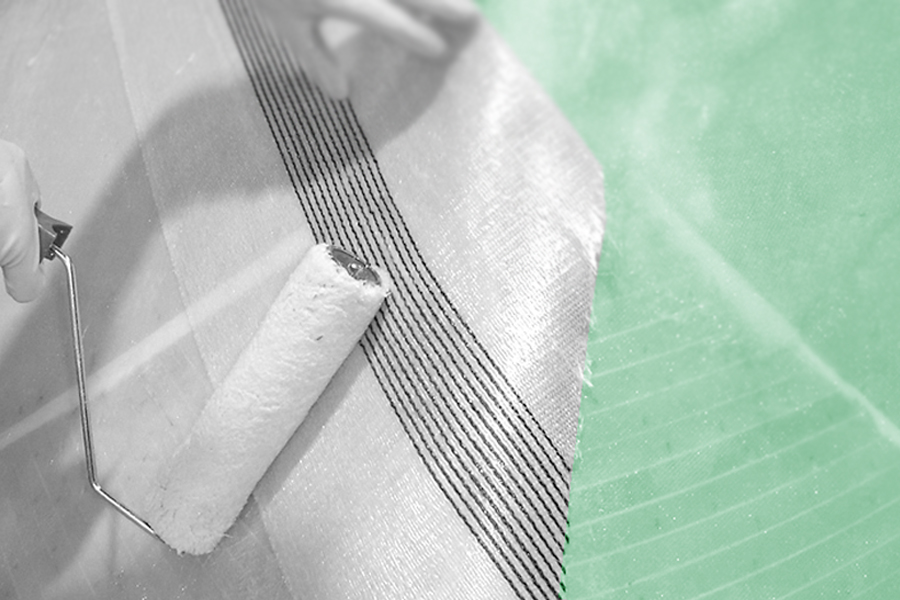
A seleção dos tecidos deve ser feita com base nos planos de construção criados pelo projetista, mantendo sempre as mesmas gramaturas e direções no caso de alguma adaptação. Tecidos biaxiais são sempre a melhor opção para construções one-off e têm a vantagem de permanecerem estáveis ao longo da laminação, diferente de tecidos woven roving, por exemplo, que criam superfícies irregulares. Em barcos muito grandes onde as camadas de fibra ultrapassam 3 kg/m², o construtor pode optar por utilizar um número maior de camadas de tecidos mais finos, que irão fornecer um acabamento quase perfeito.
Clique aqui para acessar Strip Planking em Espuma de PVC – Parte 2
Lucas Lopes disse:
Como selecionar a melhor resina de laminação para esse tipo de strip planking?
Barracuda Composites disse:
Olá, Lucas
Uma das grandes vantagens do processo de Strip Planking é a possibilidade do uso de resina poliéster. O strip planking em madeira exige o uso de resina epoxy, que tem um custo muito maior. Entre as opções de poliéster, você precisa observar a compatibilidade da resina com a espuma PVC, além de selecionar uma resina adequada para laminação manual, pois, como veremos nas próximas semanas, as faces dos painéis são laminadas dessa forma.
Fernando disse:
Já possui o livro do Sr. Jorge, mas aguardo por aqui mais informações. A ideia de construção e um Samoa 34/36 ou Mutchine 34/36. Um usa strip outro panel plancking. Estou no aguardo apenas da definição do local para adquirir os projetos. Conto com a ajuda dos senhores.
Manuel disse:
Estou interessado na construção de uma catamaran com projeto de construção em strip planking em madeira e gostaria de saber se posso substituir essa madeira pela espuma de PVC sem que prejudique a aceitação do engenheiro naval já que o projeto original é em madeira.
Barracuda Composites disse:
É possível sim! A construção com laminados sandwich com núcleo de espuma PVC é capaz de produzir embarcações mais resistentes e mais leves do que seria possível construir em madeira. Prova disso é que há décadas embarcações militares substituíram a madeira por laminados sandwich com núcleo Divinycell, como é o caso dos navios suecos das classes Landsort, caça-minas construídos entre 1983 e 1996, e Visby, corvetas construídas entre 2000 e 2009. Você pode saber um pouco mais sobre a história das construções em sandwich nesse post do nosso blog.
francisco Bittar disse:
tenho uma pergunta que nao tem muito a ver com esse post, mas achei ele o mais semelhante à pergunta.
Então, estou projetando um veleiro de 11 pes que tem o fundo levemente curvado e o costado reto (tipo um mini 650),ele seria construido em compensado naval de 6mm. Portanto pensei em fazer o fundo com varias chapas de de compensado de uns 10 cm de largura, moldadas sobre as cavernas e longarinas; e seriam aparelhadas em 45 graus , um lado espelhado do outro( como sao feitos alguns cascos em cold molded, acho). A pergunta entao é se eu precisaria fazer uma segunda camada* de chapas no sentido inverso da camada de baixo, como se faz em um cold molded normal de madeira maciça.
Eu deduzo que só uma camada seria suficiente, pois o compensado, diferentemente da madeira maciça, já tem laminas no com os veios da madeira no sentido inverso , correto? muito obrigado!
* só para esclarecer, se eu for fazer com as duas camadas eu usaria chapas de 3mm
Barracuda Composites disse:
Olá, Francisco
Parabéns por sua iniciativa, esperamos que seu projeto seja um sucesso. Em construções com compensado naval é comum que as camadas interna e externa sejam contínuas e as placas intermediárias sejam sim posicionadas com uma orientação de [0/90]. Deve ser realizada também a laminação da superfície externa da embarcação para garantir a estanqueidade do seu veleiro. É necessário que se faça o uso de resina epoxy para garantir a adesão das camadas de fibra de vidro com a madeira e evitar o fenômeno de hidrólise, que pode causar apodrecimento do compensado por absorção de água. Como você ainda está na fase de projeto, é válido analisar a possibilidade do uso dos métodos de strip planking em espuma PVC ou até mesmo do power flex, que vão permitir que sua construção tenha um custo menor e leve menos tempo, além do fato que seu barco ficará mais resistente, mais durável e mais leve.
Alexandre disse:
Olá.
Li o livro, muito bom, porém não dá conclusão sobre quantidade de tecido usar no fundo, costado e convés. Número de camadas e gramatura do tecido de cada camada, parte interior e exterior do barco. Como obtenho estes valores?
Outra pergunta. É possível dividir um barco de 12m em 4 partes de 3 e fazer laminação de cada uma destas partes de forma separada?
Teria que fazer neste caso camada por camada ou já poderia colocar todas as mantas uma sobre a outra, impregnar com resina e dai aplicar vacuo?
Obrigado
Barracuda Composites disse:
Olá, Alexandre
O número de camadas e a gramatura do tecido vão depender da espessura que você deseja alcançar. Como uma regra geral, você pode obter a espessura a partir da expressão: t = (n.Aw)/(ρf.vf).
Nessa expressão, n representa o número de camadas, Aw representa a gramatura do tecido que você selecionar, ρf é a densidade da fibra de vidro e vf é o teor de fibra que o seu processo construtivo é capaz de alcançar. Com a espessura requerida calculada, você pode selecionar o tecido e a quantidade de camadas necessárias para alcançá-la.
Não é comum dividir o casco em diversas partes e realizar a laminação separada porque a continuidade é uma característica importante para a estrutura.
Felipe disse:
Olá,
Minha dúvida é qual livro devo comprar para aprender sobre o método em strip planking em PVC ?
pretendo construir um projeto do Cabinho em breve .
Obrigado
Barracuda Composites disse:
Olá, Felipe
O método de Strip Planking em PVC é descrito no Métodos Avançados de Construção em Composites. Você encontrará um cpítulo inteiro dedicado a essa técnica.
JOSÉ ROBERTO DE FREITAS DIAS disse:
Fiz uma pergunta parecida em outro post, mas achei interessante a construção com o PVC expandido para a minha situação, mas fica uma dúvida: posso construir um casco de 2,20 x 1,40 m, talvez até um pouco maior, para um aerobarco? Este tipo de embarcação é submetida a muitos impactos e torções, porém poderia utilizar reforços em fibra de carbono e aramida. Mas gostaria de ter uma sugestão de quantidade de camadas que preciso em um casco nestas medidas, mesclando o tecido de vidro, fibra de carbono e uma camada externa de aramida de fundo de casco.
Barracuda Composites disse:
Olá, José
O uso de espuma PVC realmente vai diminuir o peso da sua embarcação. O projeto estrutural desse tipo de construção é bastante particular e o plano de laminação vai depender do tipo e das quantidades de reforços que você utilizar.
Em teoria, é possível você realizar a construção utilizando a fibras de carbono e fibras de vidro, a quantidade de camadas vai depender da resistência que você precisa obter e da espessura que deseja.
Ricardo alaim disse:
Boa noite estou comprando um projeto do Roberto barros cabinho, multichine 26c, já é um barco de pequeno custo, minha intenção é construi-lo com o melhor material no mercado.
Essa construção em strip plaking nesse caso seria uma boa.
Perdão a pergunta sou novo no mundo da construção naval.
Barracuda Composites disse:
Olá Roberto,
A contrução em Strip Plancking ou Multichine em espuma de PVC é uma ótima opção.
Nos avise se tiver alguma dúvida!
André Gustavo de Carvalho Magalhães disse:
Boa tarde.
Estou planeando fazer um barco pequeno para pesca de 18 a 20 pés pelo método de strip planking em espuma de pvc. Minha pergunta: esses strps são comercializados no comprimento, largura e espessura solicitadas ou ja existe strps de varias medidas para escolher. E dentro dessa escolha qual seria o melhor strip
para um barco com 18 a 20 pés.
Grato pela atenção.
André.
Barracuda Composites disse:
Olá André,
Os Strips são cortados na espessura e na largura desejada (costuma ser de 30 a 50mm) no comprimento da chapa de espuma.
Att,
Paulo Villegas disse:
Senhores, boa tarde!
Tratando-se de veleiros, até qual tamanho de embarcação poderia ser construída usando o método de construção Strip Planking em Espuma de PVC? Eu poderia construir um veleiro de 40, ou 50 pés por exemplo?
Barracuda Composites disse:
Bom dia Paulo,
Não há restrições quanto ao tamanho de um veleiro que pode ser construído através do método de strip planking. Sem dúvida, você consegue construir um valeiro de 40 ou 50 pés.
Leonardo Antunes disse:
Ohhh meu amigo,que bela página a sua, com muita informação e você é muito simpático, responde à todos! Você pode me ajudar??? Estou na fase de projeto para faser uma traineira de 8 a 10 metros, sei muito pouco sobre o assunto mas,moro perto de praia e vi uma possibilidade de uma forma melhor de trabalho. Quero este barco para fazer turismo com as pessoas que gostam de pescar, é possível fazer ele usando o strip planking em espuma PVC ou até mesmo do power flex que você falou? Lembrando que ele terá motor… é possível fazer este barco??? Quantas pessoas este barco suporta? Ele é seguro??? Você escreve e vende livros sobre o assunto??? Vende os materiais??? Obrigado pela Simpatia e se puder me ajudar, fico muito grato. Deus abençoe.
Barracuda Composites disse:
Boa tarde Leonardo,
É sim possível fabricar essa embarcação através do processo de Strip Planking com espuma da PVC e até mesmo por Power Flex se o projeto for mais plano. Com esses tipos de fabricação a embarcação fica muito resistente e fica bem mais leve do que os projetos originais em madeira, o que gera uma boa economia de combustível a longo prazo.
Quanto a capacidade de passageiros, isso depende do projeto da embarcação em si, não há limite devido ao tipo de material utilizado.
Os Livros Manual de Construção de Barcos e Técnica e Prática de Laminação em Composites detalham muito bem esses dois tipos de fabricação.
Caio disse:
Boa tarde, eu comprei o livro MÉTODOS AVANÇADOS DE CONSTRUÇÃO EM COMPOSITES com o intuito de converter o compensado naval em espuma de PVC porém, não ficou muito claro para mim. O veleiro que eu quero construir tem 5 metros de comprimento (Sztrandek 495).
No capitulo 6, espessuras básicas, fala para calcular o número estrutural do barco(NS).
NS= 0,25.
Espessura do costado – abaixo e acima da DWL = 4mm
Em espessura dos tecidos, eu não entendi quando diz: “teor de 50% para tecidos biaxiais combinados”.
Como eu tinha encontrado a espessura do costado(4mm), eu cheguei a conclusão de que teria que ter 1500g/m quadrado. Esta certo isso?
Seria através da espessura do costado e da espessura dos tecidos que eu descobriria a densidade da espuma de pvc e a quantidade de camadas da fibra de vidro?
Barracuda Composites disse:
Boa tarde, Caio
Para 5 metros o número estrutural é de 0.4, a espessura do costado é de 4mm e a do fundo de 6mm. Cada 1200 g/m2 de tecido combinado, laminado manualmente, vai representar 1mm de espessura. Então, aí você tem o seu plano de laminação. Esta espessura representa 50% de teor de fibras.
valter chamisso coca disse:
Olá !!!!
Tem alguma literatura sobre cálculos estruturais para definição das espessuras(interna / Externa) para um casco em strip e principalmente sobre o espelho de popa, no caso para embarcação com motores de popa.
Vou fazer um casco de 24´ usinado em maquina cnc, alias já dei inicio ao projeto
Grato : Valter
Barracuda Composites disse:
Oi Valter,
Sugerimos que você leia o livro Métodos Avançados de Construção em Composites! Nele tem um capitulo sobre dimensionamento estrutural com as espessuras recomendadas.
Luis Henrique Gomes disse:
Luis Henrique Gomes
Olá!
Eu comprei projeto do samoa 28 para contrução em strip planking em espuma de PVC. Esse método basta apenas no caso do costado trabalhar com as réguas de PVC + as camadas de fibra de vidro e resina epóxi, enfim tudo que for necessário por fora e por dentro do casco? O PVC seria o núcleo certo? . O suficiente para se ter um casco de -+ 9 metros firme,seguro, forte e rígido? O convés e anteparas também do mesmo material? São muitas perguntas e dúvidas, essa é a minha primeira vez. Já tive um velamar 33 e fast 345 , mas construir é a primeira vez. Desde já agradeço
Barracuda Composites disse:
Sim. O método é bem simples. O livro vermelho https://www.e-composites.com.br/metodos_avancados_de_construcao_em_composites/p
tem a descrição do processo com centenas de fotos. Tanto para o casco quanto para o convés.
Neste processo voce pode usar resina poliéster que é bem mais simples e fácil de trabalhar além de ser bem mais econômica que epoxy.
Leia o livro que muitas das suas duvidas vão desaparecer!!!
Boa sorte.