A construção das estruturas de materiais compostos como se conhece hoje só foi possível com o desenvolvimento das fibras de vidro em meados de 1940. As fibras de carbono apresentam uma revolução igualmente significativa para os composites estruturais, sendo um reforço mais forte, mais leve e mais durável que qualquer outro material disponível no mercado atualmente.
Desde a década de 1970, a indústria é capaz de produzir fibras de carbono a base de polímero de poliacrilonitrila (PAN) em grandes volumes, mantendo o desempenho, qualidade e consistência necessárias no processamento de materiais desenvolvidos para indústria aeronáutica, para onde elas foram originalmente desenvolvidas.
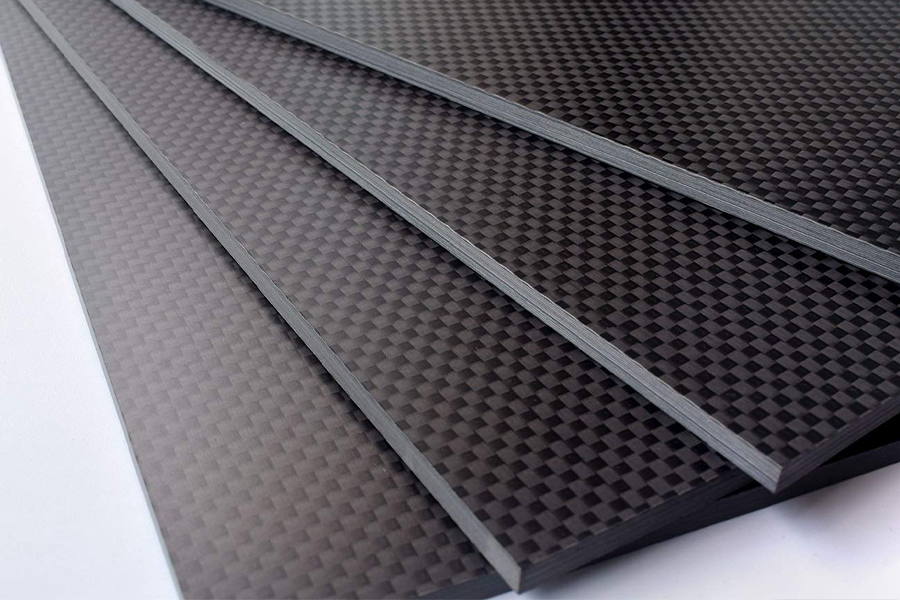
Na indústria náutica sua aplicação é destinada à peças que necessitam de uma eficiência estrutural muito alta ou que precisem ter baixo peso para que o centro de gravidade da embarcação não fique muito alto e prejudique a estabilidade da navegação. Ou seja, não são apenas os barcos de regata que fazem uso desse tipo de reforço, mas muitos estaleiros acabam utilizando fibras de carbono para construção de casarias e principalmente de hard tops.
Assim como existem diferentes variedades de fibra de vidro, existem diferentes variedades de fibras de carbono. A diferença entre elas se concentra principalmente na combinação entre resistência à tração e módulo de elasticidade, como indicado no Gráfico 1.
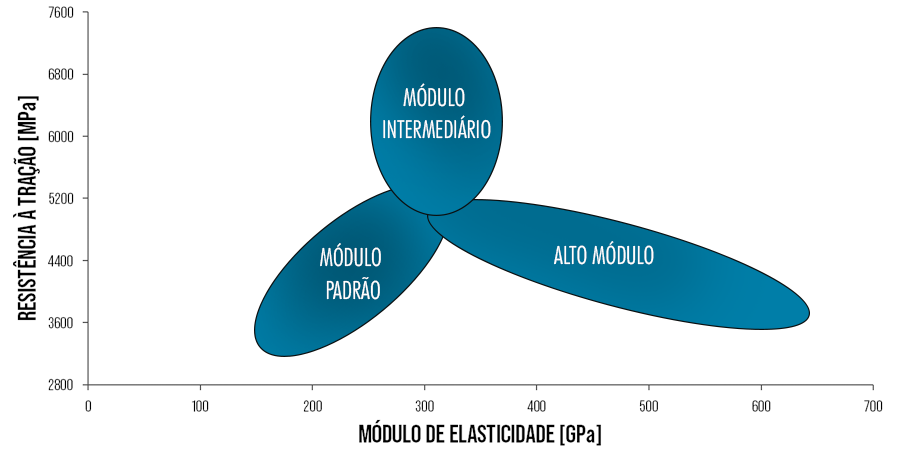
As fibras de carbono de módulo padrão, conhecidas no mercado como fibras de Standard Modulus, possuem módulos de elasticidade até 230 GPa ou um pouco superior. São as fibras de carbono com melhor custo-benefício considerando tanto a resistência à tração quanto a rigidez do material, com fios construídos com 1k a 24k filamentos.
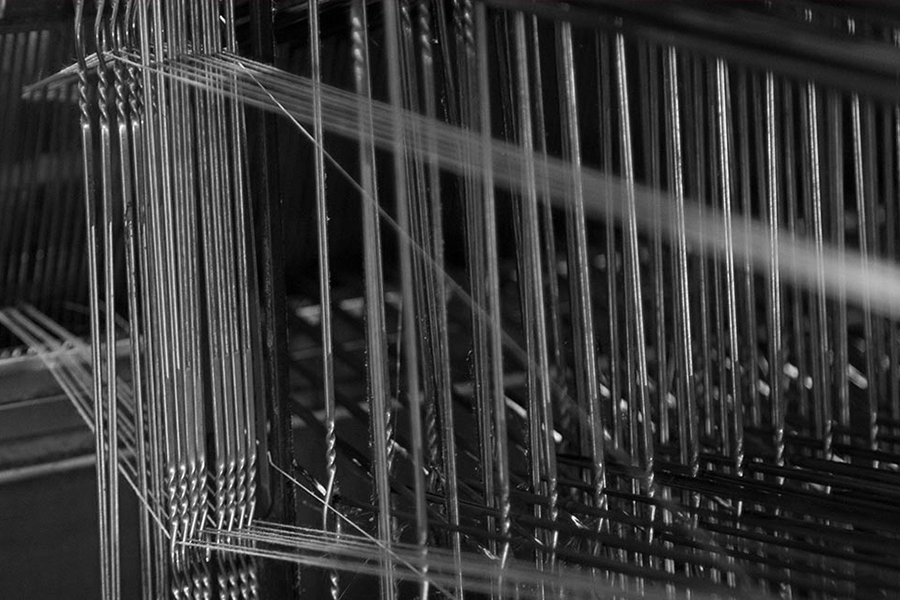
As fibras de módulo intermediário, ou Intermediate Modulus, possuem módulos de elasticidade que variam entre aproximadamente 290 e 330 GPa. Existe uma grande variedade dessa classe de fibras de carbono, que também são conhecidas como High Strength porque apresentam a melhor resistência à tração. A diferença entre os conceitos de resistência e módulo de elasticidade já foi abordada em vários tópicos e detalhes no blog.
As aplicações das fibras de módulo intermediário são bastante amplas, incluindo as áreas aeroespacial, industrial, entre outras. Por sua ampla gama de opções, elas apresentam diversos preços e propriedades para atender as diferentes demandas desses mercados. Os fios dessa classe de fibras de carbono são construídos com uma quantidade de filamentos que varia ente 6k e 36k.
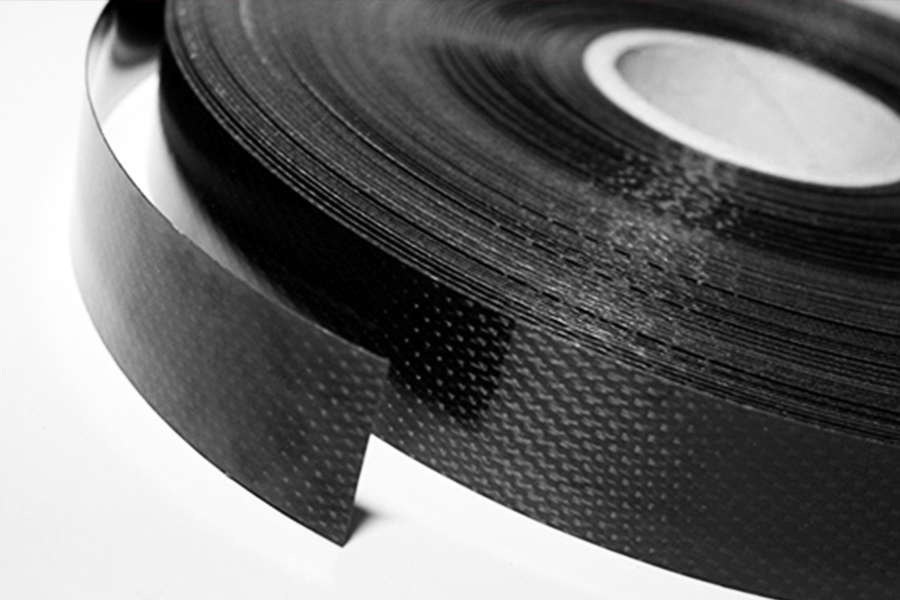
Por fim, as fibras de carbono de alto módulo, também chamadas de High Modulus, podem alcançar módulos de elasticidade de até 640 GPa. São normalmente utilizadas em aplicações onde a expansão térmica é um fator crítico, já que seu coeficiente de expansão é muito baixo. Isso inclui estruturas aeroespaciais e até mesmo artigos esportivos de altíssimo desempenho. Os fios das fibras de carbono de alto módulo são compostos por uma quantidade de filamentos que varia entre 3k e 12k.
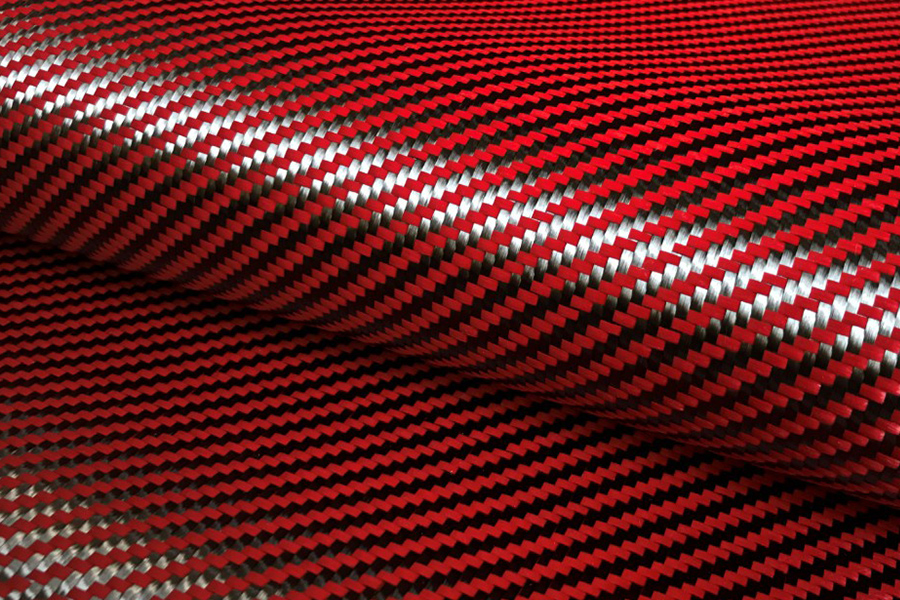
Ao selecionar o melhor tipo de fibra de carbono para o seu projeto, o construtor deve também verificar qual o tratamento superficial a fibra recebeu, já que isso definirá qual o sistema de resina será compatível com os filamentos. Em geral esse tipo de reforço é compatível com sistemas de resina epoxy e, mais raramente, com resinas estervinílicas e poliéster.
As subclassificações dentro dos tipos de fibra de reforço são mais algumas das inúmeras variáveis que o construtor deve estar atento no momento de selecionar os melhores materiais para seu barco.
Lucas Marttens disse:
É obrigatório laminar fibras de carbono com resina epoxy?
Barracuda Composites disse:
Olá, Lucas
O tipo correto de resina é determinado pelo tratamento superficial que as fibras recebem durante o processo de fabricação. Em geral, as fibras de carbono são fabricadas para serem compatíveis com epoxy porque esse tipo de resina possui propriedades mecânicas e de adesão melhores, sendo capaz de extrair o melhor desempenho possível de uma fibra que é utilizada em projetos que demandam elevada eficiência estrutural.
Daniel Freitas disse:
A fibra mais resistente não é sempre a mais rígida?
Barracuda Composites disse:
Olá, Daniel
Não necessariamente, são propriedades distintas apesar de estarem relacionadas pela Lei de Hooke. A resistência é representada pela tensão que o material desenvolve antes da ocorrência de um determinado fenômeno, por exemplo, a ruptura. A rigidez se relaciona com o a resistência à deformação que o material apresenta. Você pode entender um pouco mais sobre esses conceitos nesse post.