O processo Power Flex é uma maneira de utilizar a eficiência mecânica e produtiva do processo de infusão para a construção de barcos one-off em cascos com o formato multichine. Nos posts anteriores foram abordados os conceitos e as etapas de construção dos painéis k-lite e fabricação e montagem dos picadeiros e cavernas.
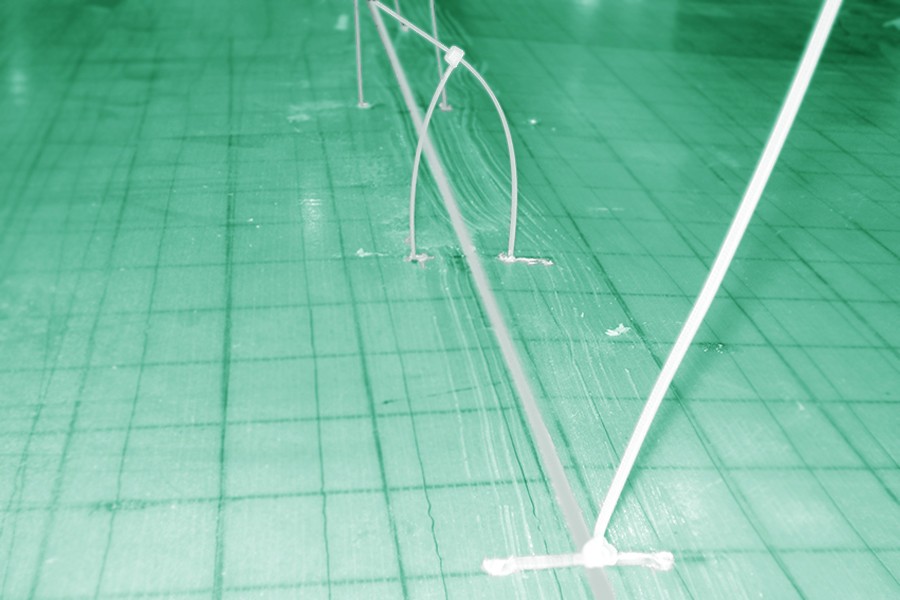
O que se segue é o processo de consolidação e acabamento do casco, realizado por meio do posicionamento dos painéis k-lite utilizando abraçadeiras de plástico. As linhas de colagem devem então serem preenchidas com adesivo de base epoxy e sílica e a integridade estrutural da embarcação é garantida a partir da laminação manual de tapes de fibra de vidro nessas linhas. Depois é a vez da etapa de acabamento, composta pela aplicação de massa no casco, seguida do primer e da pintura.
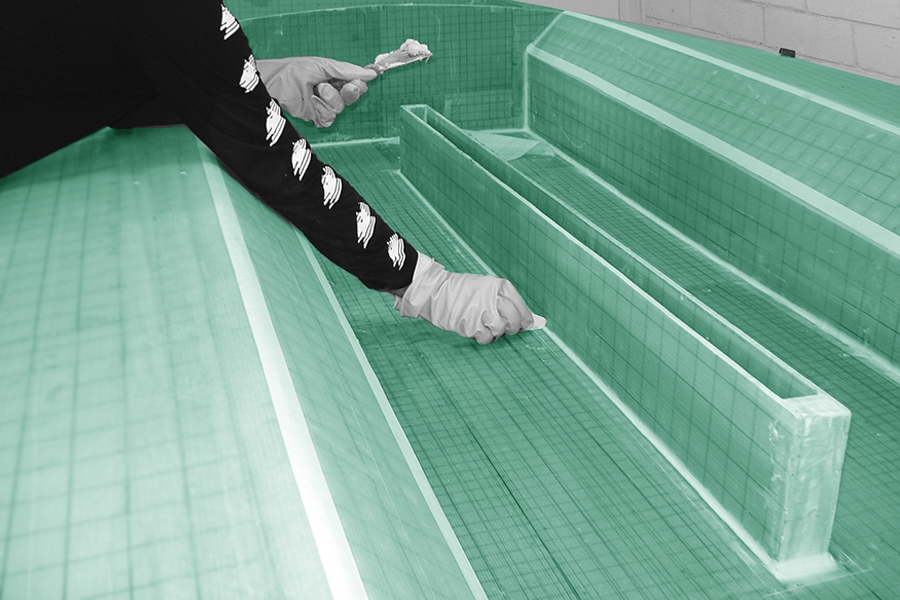
O primeiro passo para a montagem do casco é fazer uma série de furações com diâmetros de 3-4 mm nos painéis para que seja possível utilizar abraçadeiras plásticas para juntá-los na posição correta. A abraçadeira deve produzir pressão suficiente para manter os painéis juntos até a cura do adesivo e o espaçamento entre elas deve ser suficiente para evitar o empeno das arestas do painel.
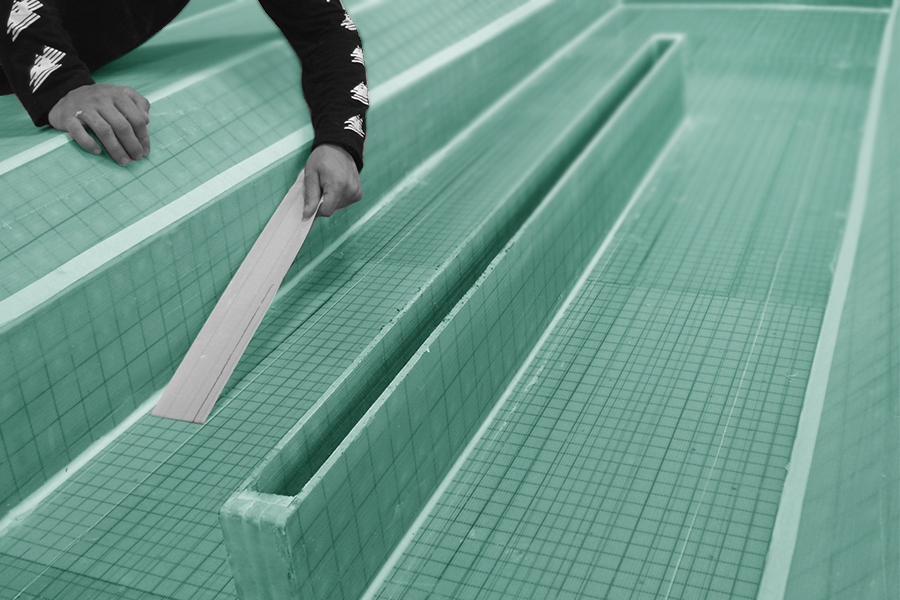
Quando as chapas estiverem posicionadas, as abraçadeiras devem ser retiradas para aplicação do adesivo sobre o topo das cavernas. Para garantir uma superfície livre de contaminação na etapa de aplicação de massa no casco, o peel ply dos painéis infundidos deve ser removido apenas na região onde o adesivo será aplicado. O adesivo utilizado deve ser à base de resina epoxy e sílica, para garantir a adesão entre os painéis e uma tixotropia que impeça o escorrimento entre as placas que, depois de receber o adesivo, devem ser posicionadas no local adequado e fixadas novas abraçadeiras de plástico.
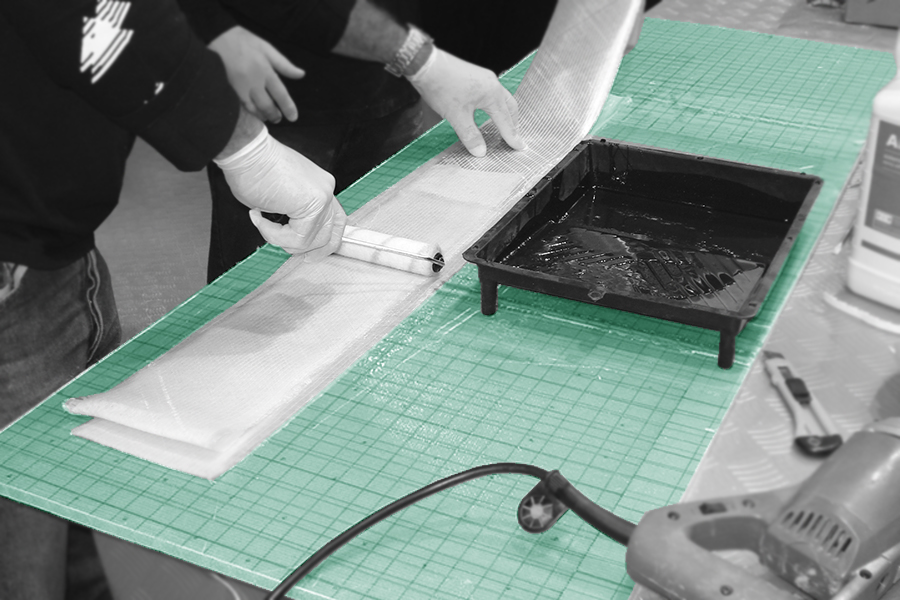
Após a cura completa do adesivo, é hora de realizar a laminação dos tapes na superfície externa do casco. Para começar, é preciso retirar as abraçadeiras plásticas e verificar se as linhas de colagem estão perfeitas. O peel ply na região das laminações deve ser retirado também e uma lixadeira de fita com lixa de ferro #40 ou #60 deve ser utilizada para preparar a superfície.
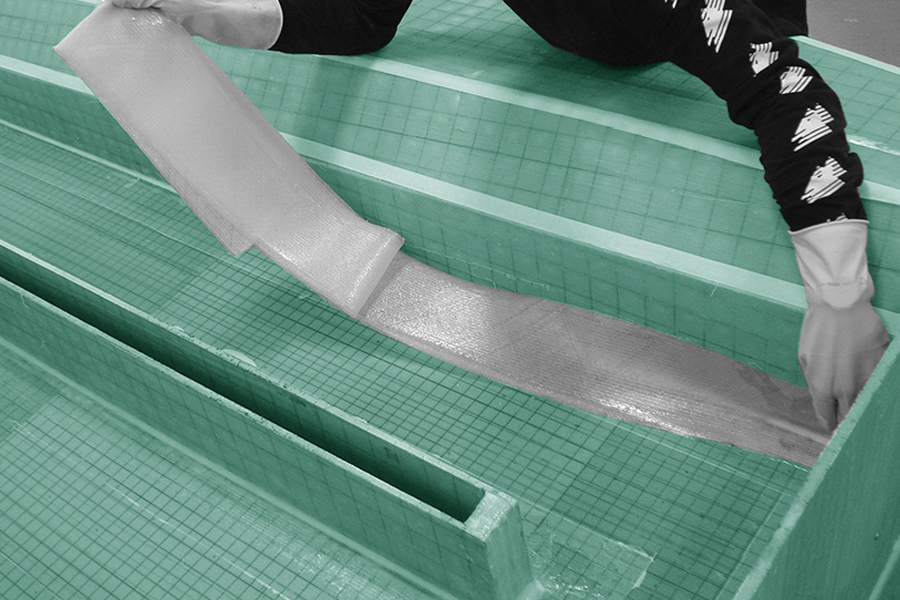
Os tapes devem ser contínuos e ter as bordas do tecido preparadas para evitar ressaltos. Em um barco pequeno, um tape de tecido biaxial [±45] com gramatura de 200-300 g/m² é a melhor opção em termos estruturais. A resina de colagem normalmente é à base de epoxy, de modo que se obtenha uma união sólida e resistente. Resinas poliéster podem ser utilizadas e apresentarão facilidade de manuseio, mas devem ser testadas para determinar sua compatibilidade com a resina utilizada nos painéis.
Antes de iniciar a laminação, é necessário aplicar na superfície uma pequena quantidade de pasta de resina catalisada com sílica, o que facilita a colocação dos tapes e evita que eles escorreguem sobre a superfície seca. Os tapes devem ser pré-impregnados sobre uma mesa de laminação antes de serem posicionado no casco e o peso de resina não pode ser superior a 50% do peso das fibras.
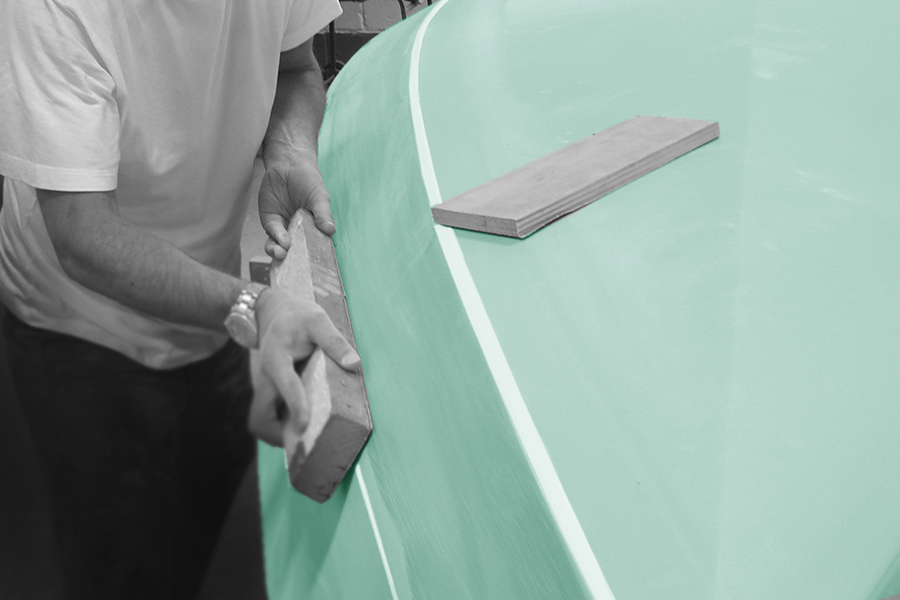
Depois de posicionado e acabado, uma tira de peel ply deve ser colocada em cima do tape para evitar que a resina fique exposta e para preparar a linha de colagem para receber o acabamento.
Após o posicionamento do peel ply em todas as linhas de colagem, é necessário virar o casco e realizar a laminação dos tapes na parte interna da mesma maneira. Só após a cura deles é que se inicia o acabamento com massa e tinta. É possível escolher entre massas de epoxy e de poliéster para o acabamento.
Seguindo a aplicação da massa, o casco deve ser preparado para receber o primer por meio do lixamento manual e contínuo de forma progressiva com lixas de ferro de #40, #60 e #80. Com o casco limpo e livre de resíduos, o primer deve ser aplicado em duas demãos cruzadas para garantir uma superfície uniforme e com brilho. Depois de sua cura, é necessário mais um lixamento do casco, dessa vez com lixas de ferro de #60 e #80 e então é possível realizar a pintura e acabamentos finais.
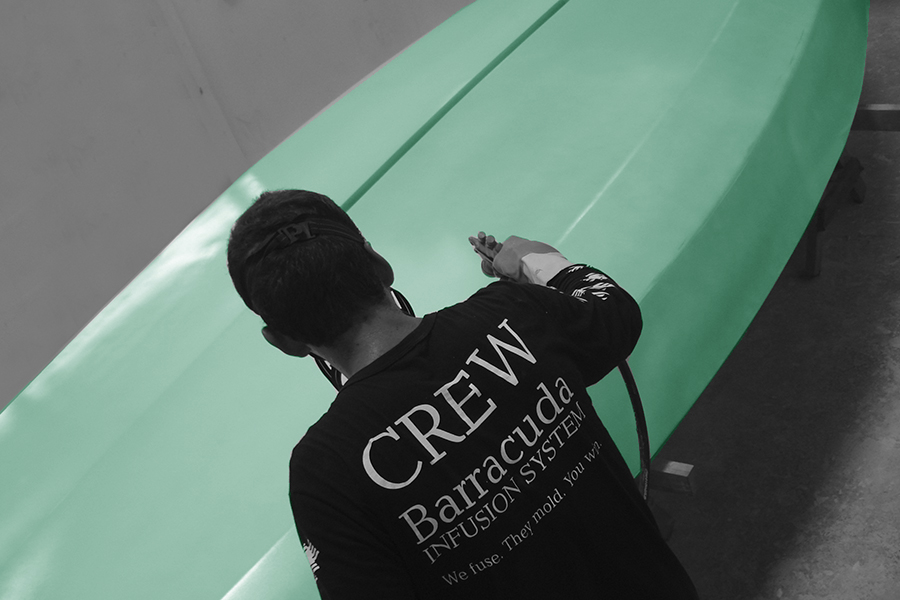
Para mais informações sobre o Power Flex, é possível adquirir o livro Técnica e Prática de Laminação em Composites, que descreve com detalhes o processo de construção do dingue Andorinha, projeto desenvolvido no escritório de Roberto “Cabinho” Barros, com fotos ilustrativas de todas as etapas.
Rodrigo Santiago disse:
Como escolher o primer certo para a etapa de acabamento?
Barracuda Composites disse:
Olá, Rodrigo
A compatibilidade do primer com a massa de acabamento utilizada deve ser sua maior preocupação quando você for selecionar esse produto. A boa notícia é que não faltam opções no mercado e a lista de fornecedores é longa. No caso da construção do Andorinha, usamos um primer de dois componentes à base de epoxy compatível com a massa de poliéster.
Marcio Silva disse:
O uso da resina epoxy não seria mais seguro na laminação dos tapes? Garantindo que os painéis estejam bem estruturados?
Barracuda Composites disse:
Olá, Marcio
A resina epoxy vai sim garantir uma colagem mais resistente se for corretamente aplicada e feita para ser utilizada na laminação de composites. Porém, se não houver nenhum problema de compatibilidade com a resina de laminação dos painéis k-lite, a resina poliéster consegue fazer o mesmo trabalho com um custo menor e com maior facilidade de manuseio, sendo uma opção viável e segura.
Laura Fernanda disse:
Porque colocar o peel ply após a laminação dos tapes se ele é um tecido com função desmoldante?
Barracuda Composites disse:
Olá, Laura
Apesar de ser a principal, essa não é a única função desse material. O tecido de peel ply também fornece uma textura de acabamento na peça que diminui o trabalho de lixamento posterior e nesse casco, ainda protege a superfície do casco de impurezas que poderiam prejudicar a aplicação da massa de acabamento, sobretudo se ela tiver formulação a base de resina poliéster.
Marcelo disse:
Li no livro “The Element of Boat Strength” que em veleiros a área da quilha deve ser em fibra pura (sem núcleo).
Se o núcleo é o suporte da laminação, qual é a técnica para ter a área da quilha em fibra pura?
Barracuda Composites disse:
Oi Marcelo,
A quilha deve colaborar no suporte estrutural ao mastro e receber ferragens, por isso é comum que seja feita de fibra sólida. No caso da construção do barco desse post, especificamente, foram utilizadas espumas PVC de alta densidade (240 kg/m³) no pé do mastro. Em todos os pontos que receberiam ferragens também foram incorporados reforços de alta densidade dentro da espuma durante o processo de laminação. A espuma escolhida foi para essas regiões era de poliéster com 240 kg/m³, capaz de suportar os esforços de aperto de parafusos diretamente sobre elas. A bolina de fibra sólida foi fixada em uma caixa construída em painéis k-lite também. Mais detalhes sobre essa parte do processo de construção podem ser encontrados no livro Técnica e Prática de Laminação em Composites.
Nilson Garcez Montenegro Junior disse:
Olá, boa noite, tenho os três livros de construção de barcos do Sr. Jorge.
É possivel comprar o kit completo em k-lite para montagem do casco do andorinha, já nas dimensões do projeto?
Grato;
Nilson Montenegro
Barracuda Composites disse:
Bom dia, Nilson
Por favor, mande um e-mail para [email protected] com sua solicitação e número de telefone que entraremos em contato para te atender.