A eficiência estrutural de um painel sandwich depende do nível de integração entre as duas faces e o material de núcleo. O elemento responsável por esta união é a linha de colagem entre estes três elementos, que garante a integridade global da estrutura.
Posts anteriores do blog descrevem a colagem do núcleo sandwich nos processos de laminação manual e a vácuo e mostram que nesses casos a junta adesiva é composta por uma massa de colagem. Quando se utiliza o processo de infusão a vácuo, no entanto, a junta adesiva é formada por uma quantidade de resina líquida que consolida as faces e o núcleo durante a injeção da matriz.
Uma das principais características dos materiais de núcleo sandwich que é muito pouco explorada é o resin uptake, que representa justamente essa quantidade de resina necessária para realizar a ligação das faces com o núcleo. Essa quantidade de resina varia em função da natureza do núcleo, do tamanho das células de sua microestrutura e de sua densidade. Mesmo que muitos materiais tenham célula fechada, existe ainda uma pequena espessura na superfície do material onde existem células abertas devido ao corte que têm seu volume preenchido por resina durante o processo de infusão. Dependendo do tipo de material sandwich e seu processamento, esta quantidade de resina pode ser até ter uma massa maior que a do próprio material sandwich e é muitas vezes esquecida pelos projetistas.
O resin uptake não altera somente o peso final da peça, como também a quantidade de resina necessária para sua fabricação e as propriedades específicas do núcleo. Por essas razões, sua determinação é de primordial importância tanto para o projeto estrutural quanto para o planejamento da fabricação da peça, pois tem impactos diretos no custo e no desempenho das estruturas fabricadas em materiais compostos. O custo da resina absorvida nestas pequenas células abertas pode ser consideravelmente alto e desconsiderado no custeio do processo.
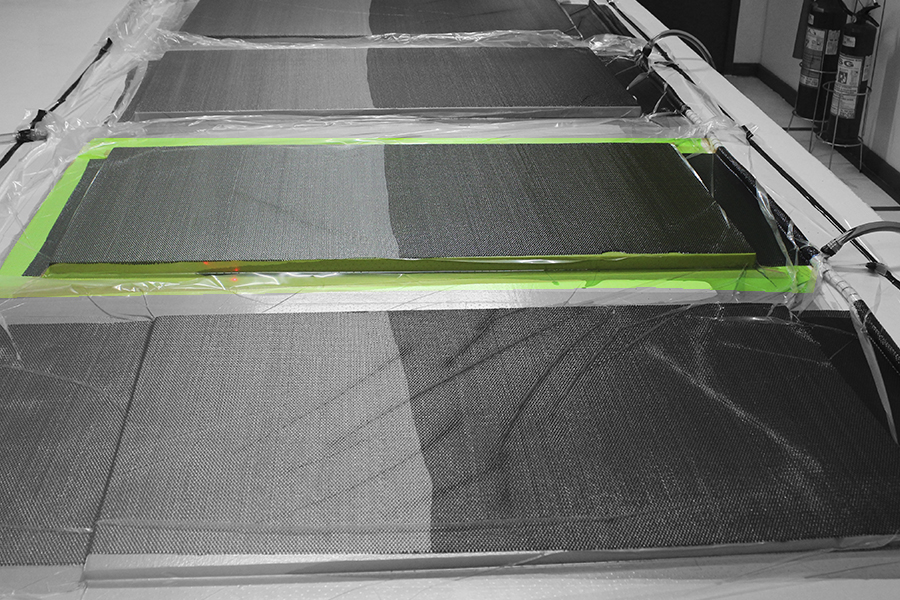
Assim como a maior parte das propriedades dos materiais compostos, a melhor maneira para determinar o resin uptake de um material de núcleo é de forma experimental. O processo começa com o cálculo da massa e das densidades nominais das placas. Esse processo é seguido da infusão das amostras que passam pelo tempo de cura adequado e, após isso, são novamente pesadas.
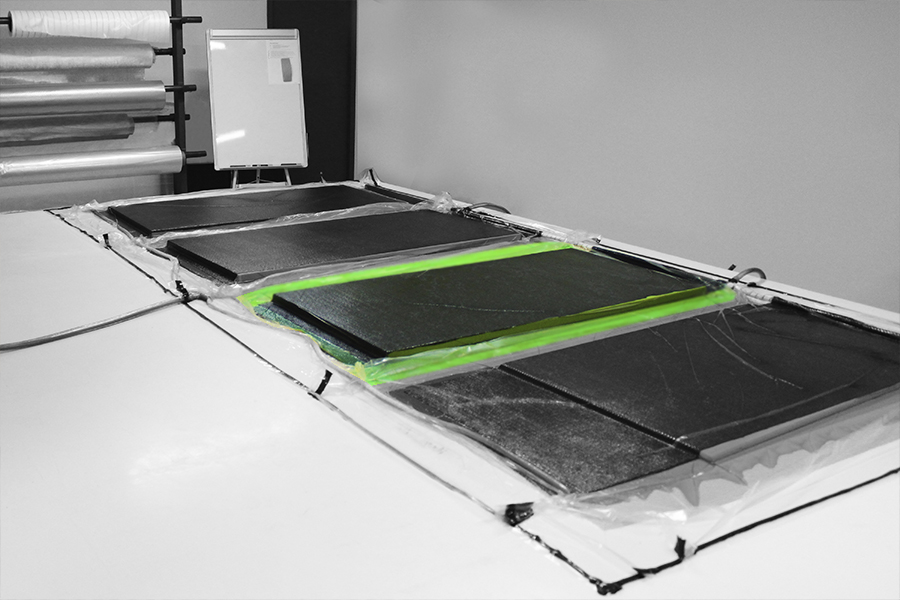
É importante determinar a densidade nominal dos materiais de núcleo antes da infusão porque a densidade informada pelos fabricantes dos materiais está sujeita a uma variação em função da tolerância dos produtos.
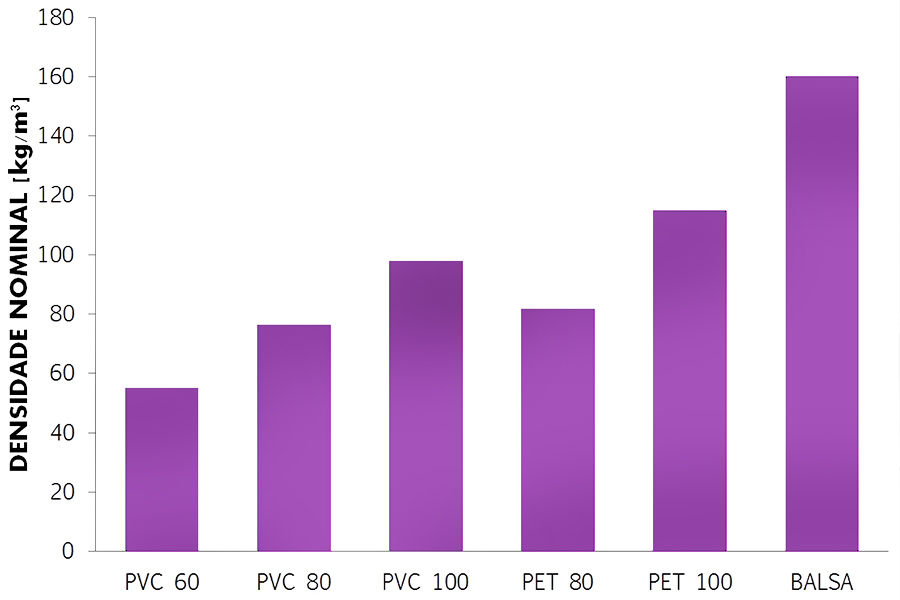
Após a infusão das placas com as mesmas condições de pressão e temperatura, linhas idênticas de resina e vácuo e resina com mesmo valor de viscosidade, é possível determinar o resin uptake simplesmente subtraindo a massa dos núcleos antes e depois do processo de infusão.
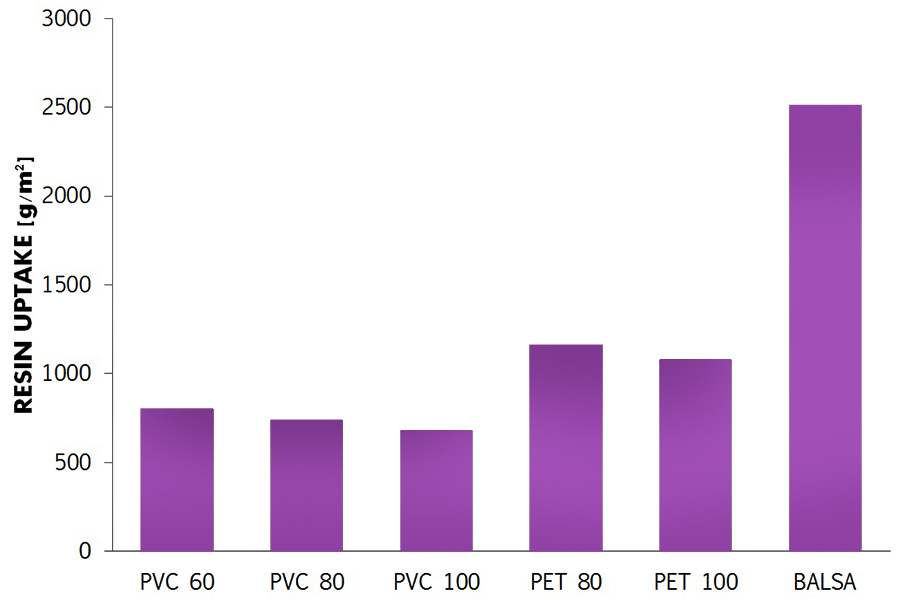
Essa informação está presente no Gráfico 2 em g/m2 e fica evidente que no caso das espumas quanto maior a densidade do núcleo, menor seu resin uptake. No caso da madeira de balsa esta regra não se aplica. É possível perceber ainda que as espumas de PVC absorvem uma quantidade menor de resina do que as espumas PET e que a madeira balsa. A razão disso é que o PVC possui células bem pequenas e fechadas, enquanto os dois outros núcleos têm células disformes e abertas que permitem que a resina permeie toda a sua estrutura interna e não apenas sua superfície.
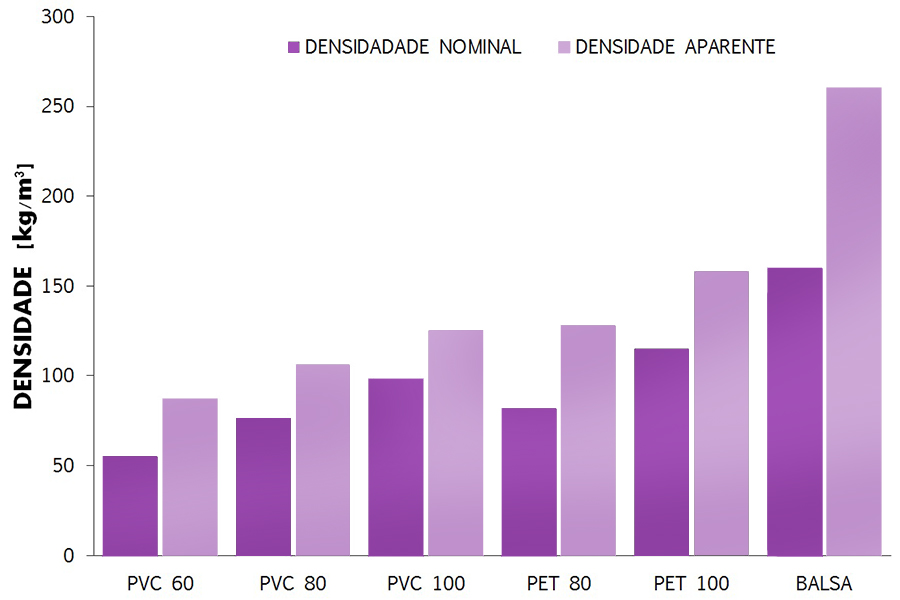
O Gráfico 3 mostra como o resin uptake altera a densidade final dos núcleos sandwich, também chamadas de densidades aparentes. Um aumento mais drástico da densidade aparente significa uma diminuição mais significativa nas propriedades específicas do material sandwich e, portanto, uma diminuição da eficiência estrutural.
Por fim, o Gráfico 4 ilustra como o tamanho da célula da microestrutura de espumas PVC influencia a absorção de resina dos núcleos. Quanto maior o tamanho da célula, mais espaço a resina tem para ocupar e, portanto, maior o resin uptake.
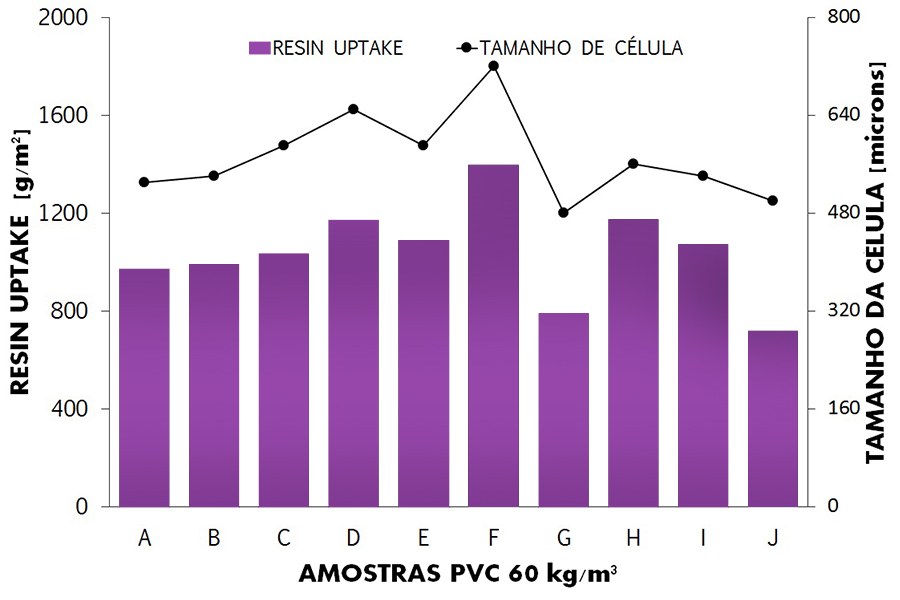
Em resumo, as espumas PVC apresentam o menor resin uptake entre as opções de núcleo. Em comparação com as espumas PET, isso acaba aumentando ainda mais sua vantagem em relação às propriedades específicas. Em relação à madeira balsa, mostra que a quantidade de resina necessária para a fabricação do laminado é menor, diminuindo o custo da fabricação. Isso ainda se soma a maior durabilidade da espuma PVC e com a possibilidade do uso de resina poliéster, que possui um custo muito menor em comparação com a resina epoxy que a madeira balsa exige.
Roberto disse:
E o honeycomb? Qual o resin uptake aproximado?
Barracuda Composites disse:
Olá, Roberto
O honeycomb é um núcleo formado por células abertas e a eficiência de sua estrutura se apoia justamente no fato de que esse núcleo possui muitos espaços vazios. Isso se contrapõe com o processo de infusão, que tem como princípio fazer com que a resina de baixa viscosidade ocupe todos os espaços possíveis dentro do laminado. O resin uptake do honeycomb não foi estimado porque ele não é utilizado no processo de infusão, que iria preencher todos os espaços vazios de suas células abertas, criando um laminado pesado e ineficiente.
Fernanda Lemos disse:
Porque a madeira balsa exige o uso de resina epoxy e a espuma PVC não?
Barracuda Composites disse:
Oi Fernanda,
Porque a resina epoxy possui uma resistência à entrada de água no laminado maior que a resina poliéster, além de uma maior capacidade de adesão. As células abertas da madeira balsa fazem com que ela absorva água e umidade, o que deve ser evitado porque, por se tratar de um material orgânico, isso acaba causando sua degradação. A espuma PVC, que possui células fechadas, não absorve água e consegue manter sua integridade por décadas mesmo sendo laminada com resina poliéster.
Tiago Lopes disse:
Mudar as condições de infusão e a resina pode alterar o valor de resin uptake?
Barracuda Composites disse:
Olá, Tiago
Sim! Principalmente a resina, porque o resin uptake é muito dependente de sua viscosidade. Em teoria, quanto maior a viscosidade, menor o resin uptake. No entanto, a infusão depende da utilização de uma resina com baixa viscosidade, entre 180 e 250 cps. Mesmo assim, a eficiência estrutural e o teor de fibras que a infusão consegue obter justifica o uso desse processo tanto financeiramente quanto estruturalmente.