A temperatura do ambiente de laminação é uma condição crucial para um bom trabalho. O ideal seria que todas as laminações fossem feitas em situações com controle de temperatura a fim de uniformizar o processo de cura, permitindo uma curva de cura ideal da resina, evitando distorções na peça e desgaste dos moldes.
O resultado de uma laminação com temperatura controlada só mostrará seus benefícios alguns anos após o barco ser lançado ou quando este estiver sujeito a severas condições de operação, e por essa razão é difícil de convencer a um fabricante em modificar seu padrão corrente de construção.
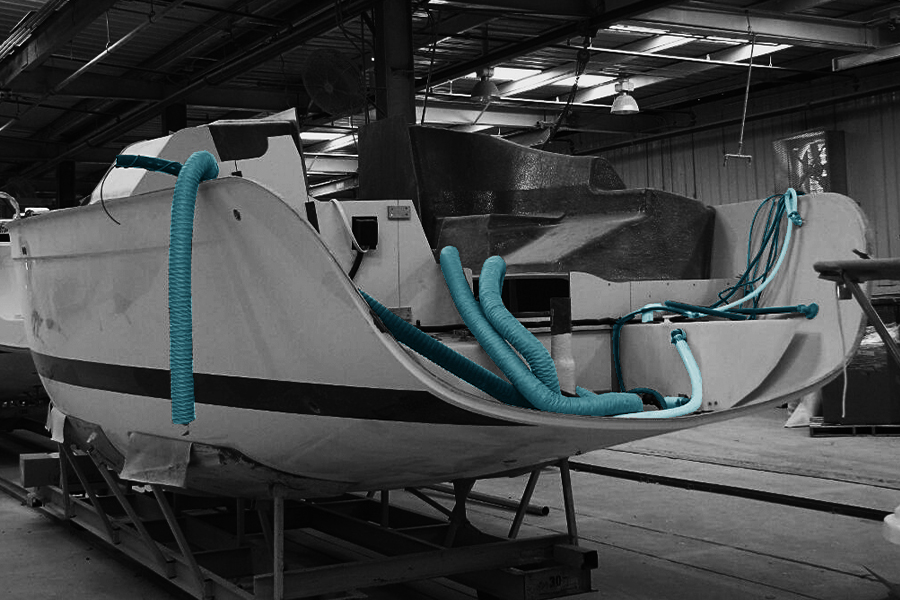
Para qualquer construção em fibra, a temperatura de trabalho deve ser mantida constante ou, pelo menos em uma determinada faixa. Para resina poliéster, a temperatura mínima varia entre 15 e 18 ºC, mas é possível laminar a temperaturas mais baixas usando maiores taxas de catalisador e acelerador ou ainda resinas de alta reatividade. A maior razão para não laminar peças abaixo destas condições é que as propriedades do laminado ficarão muito aquém dos seus valores ideais, o que se reflete diretamente em um problema na segurança e performance do barco.
Enquanto algumas resinas precisam ser curadas em temperaturas elevadas, aquelas utilizadas na construção de barcos devem ser trabalhadas idealmente a uma temperatura constante de 25ºC. Isto irá proporcionar uma cura homogênea sem distorções ou desmoldagem precoce.
Dependendo do tipo de construção, a pós-cura com temperatura elevada (depois da cura inicial a temperatura ambiente) pode trazer benefícios para o laminado. Esta prática irá acelerar o processo de maturação durante o endurecimento, aumentando as propriedades finais do laminado.
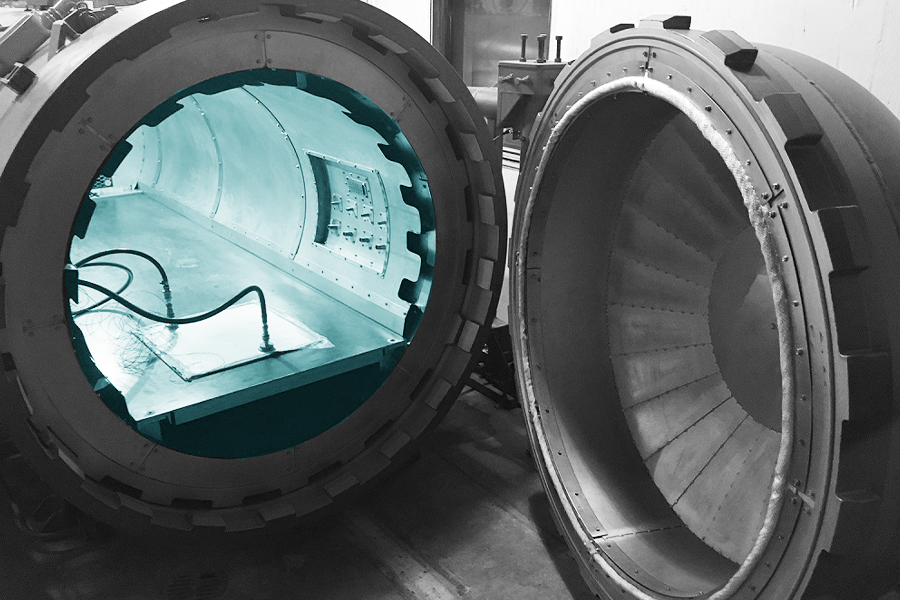
Para barcos de produção que utilizam materiais tradicionais, a pós-cura é normalmente dispensada, mas quando os barcos são feitos com produtos de alta performance, como resinas e adesivos a base de resina epoxy ou mesmo estervinílicas, ela é sempre muito importante. Resinas usadas nesses trabalhos, e sujeitas a pós cura, podem apresentar um ganho de propriedades mecânicas em mais de 20%.
Embora uma temperatura mais alta dentro da sala de laminação aumente a taxa de cura da matriz de resina, nada irá substituir o uso da proporção correta de catalisador dentro da resina. A melhor configuração é curar a resina em uma temperatura estável durante o seu primeiro período de cura e depois submeter o laminado a um processo de pós-cura.