O costado de uma embarcação é uma região que pode ter uma grande variedade de geometrias e detalhes, sendo quinas muito utilizadas como detalhes cosméticos e arquitetônicos. Em barcos mais antigos construídos em laminados sólidos, as quinas eram colocadas emparelhadas no costado para tambem prover alguma resistência adicional nos painéis, o que não é necessário em construções do tipo sandwich.
A Figura 1 mostra o detalhe onde a espuma do painel superior monta diretamente na quina do costado e a terminação do painel inferior é feita com chanfro. Neste tipo de montagem é necessário adicionar tapes de tecidos a 45° na junção para reduzir a diferença de momentos de inércia entre o laminado sandwich e a parte sólida.
A Figura 2 mostra a configuração onde se utiliza um perfil usinado de espuma de PVC para arredondar os cantos da junção. Esta comfiguração não necessita de reforço adicional pois o fluxo de tensões é praticamente constante durante todo o painel do costado.

A Figura 3 mostra o detalhe utilizado por vários estaleiros que utilizam o processo de laminação por infusão. Neste detalhe, tanto a espuma do painel inferior quanto do superior são transpassadas utilizando um enchimento de outra placa de espuma para completar o perfil final da quina. Está configuração proporciona um maior momento de inércia, agindo como um reforço extra no costado, além de promover um fluxo de resina constante durante o processo de infusão, o que não acontece em montagens estruturais que deixam laminados sólidos intercalados entre dois painéis sandwich.
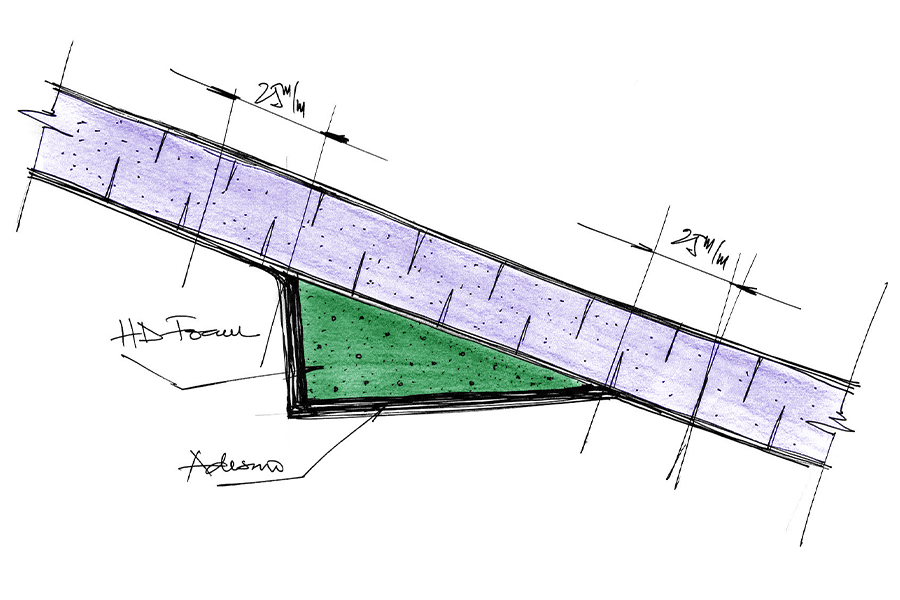
Embarcações que navegam em regime de planeio ainda possuem sprayrails na divisão entre o fundo e o costado, ou muitas vezes no fundo do casco. Esses elementos têm a finalidade de gerar uma pressão de planeio extra no fundo. O laminado dentro do sprayrails pode ter reforços unidirecionais e a espuma de alta densidade deve ser colada com adesivo de modo a preencher todos os espaços vazios. Sobre a espuma do sprayrails deve ser adicionado um tape extra na trama de 45°, como indicado na Figura 4.
Realizar o planejamento da construção de elementos como as quinas dos costados e sprayrails, ou mesmo outros presentes nessa série de posts, é um desafio pois exige experiência para que a solução seja eficiente do ponto de vista estrutural ao mesmo tempo que seja de fácil execução para que o processo produtivo não saia prejudicado. Mais detalhes estruturais estão presentes no livro Métodos Avançados de Construção em Composites.