As resinas epoxy são uma classe de resinas termofixas com amplo espectro de viscosidade, reologia e velocidade de cura, o que possibilita seu uso em uma grande variedade de aplicações como, por exemplo, resinas de laminação, adesivos, selantes, tintas e vernizes. Por incrível que pareça, apenas 5% das resinas epoxy consumidas no mundo são utilizadas para laminação de materiais compostos e desse universo 95% é utilizada na fabricação de pás eólicas.
Gráfico 1. Uso da resina epoxy no Brasil
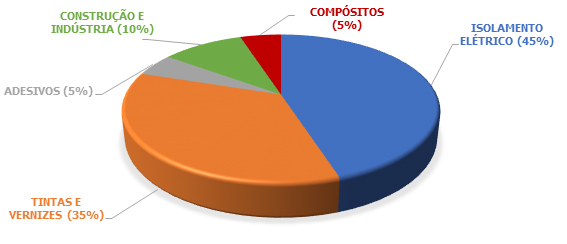
Resinas epoxy podem ser definidas como todas aquelas em que as ligações químicas ocorrem através de grupos de radicais epoxy. No estado básico, essas resinas podem ser líquidas ou sólidas. No estado sólido, elas são termoplásticas, com a habilidade de serem dissolvidas pelo calor e endurecidas pelo resfriamento. Sua conversão em uma resina termofixa ocorre através do processo de polimerização pela adição de um endurecedor que inicia uma reação irreversível de ligação entre as moléculas. Os endurecedores compõem parte da estrutura polimérica final da resina, portanto sua escolha possui influência no desempenho mecânico das peças finalizadas.
A taxa de resina/endurecedor é muito diferente de outras resinas e, dependendo do sistema utilizado, pode variar em 100:12, 100:25, 100:30 e até mesmo 100:50 partes em peso de resina e endurecedor. Para o construtor de barcos as resinas que costumam apresentar melhores características mecânicas a temperatura ambiente costumam variar a proporção resina endurecedor de 100:26 até 100:33.
O gel time da resina epoxy pode variar entre poucos minutos e várias horas, conforme a necessidade do construtor. Essa grande vantagem em relação a outras resinas pode ser controlada pela escolha do tipo de endurecer, que pode ser lento, médio ou rápido. Uma combinação de endurecedores pode ser utilizada para que se alcança um tempo de gel adequada para uma determinada peça. Um erro muito comum cometido pela maioria dos laminadores é aumentar ou diminuir a proporção de endurecedor indicada pelo fabricante para modificar o tempo gel. Ao contrário das resinas poliéster e estervinílicas, a resina epoxy não pode sofrer alteração na proporção de endurecedor pois a cura final do laminado será seriamente afetada.
Com seu gel time variando entre 15 minutos e 12 horas, as resinas epoxy possuem formulações adequadas para laminações manuais, vacuum bag e até mesmo infusão.
Há uma certa resistência por parte dos construtores de barcos de produção seriada em usar resinas epoxy por questões de custo, mas atualmente já se encontram opções com propriedades mecânicas excelentes para laminação e cura à temperatura ambiente com um custo bem acessível. No entanto, a resina é apenas uma pequena parte do custo total do barco. No caso de utilização de fibras como Kevlar® e carbono, este valor é uma pequena parcela a ser considerada pelo aumento significativo de performance no laminado.
Se esse tipo de resina for utilizado com precisão é possível se obter teores de resina até duas vezes menores que nos laminados convencionais em resina poliéster, o que também proporciona melhores propriedades mecânicas e necessidade de uma quantidade menor de fibras de reforço para o mesmo trabalho. Assim, computando o peso final do laminado, peso da resina, resistência e velocidade de construção, é possível concluir que a diferença em termos de custo das resinas poliéster e epoxy pode não ser tão discrepante.