O processo de infusão a vácuo traz uma série de benefícios para construção de embarcações que vão muito além do aumento da eficiência estrutural, já que permite a realização da laminação em um ambiente muito mais limpo e organizado. A versatilidade do processo faz com que seja possível construir estruturas a partir de moldes fechados ou até mesmo com painéis planos por meio do Método Power Flex.
Um dos principais elementos que determinam o sucesso da infusão é a resina utilizada. As duas principais características a serem observadas são o tempo de gel e a viscosidade, que são extremamente sensíveis às condições ambientais no momento da fabricação.
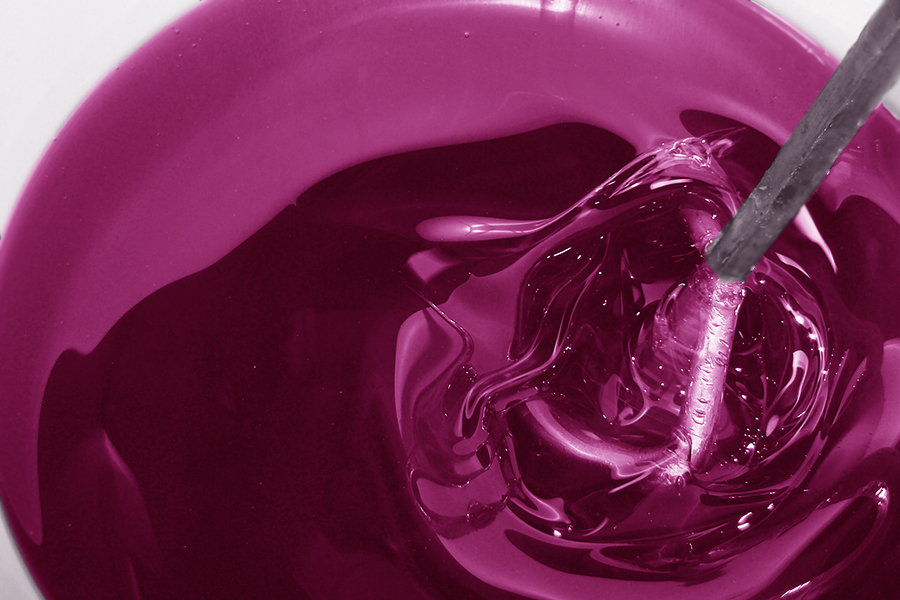
O tempo de gel compreende o intervalo entre a mistura da resina com o catalisador e o aumento exponencial de sua viscosidade, que representa sua passagem do estado líquido para o gelatinoso e, posteriormente, sólido. O Gráfico 1 indica que quanto maior a temperatura inicial da resina, menor é o tempo de gel.
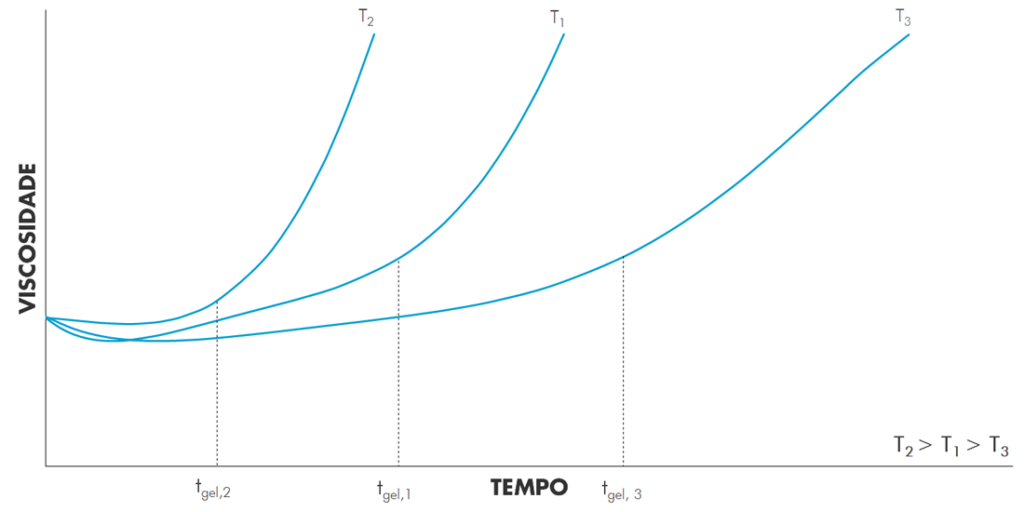
O construtor deve buscar um tempo de gel que seja suficiente para que a resina percorra o caminho designado pelo plano de infusão e entre em estado de gel antes de alcançar as linhas de vácuo, o que causaria uma queda no gradiente de pressão e prejudicaria a compactação do laminado durante o restante do processo de cura da resina.
Quando se fala de resina poliéster insaturadas, amplamente utilizadas para infusão de estruturas náuticas, o tempo de gel pode ser controlado pela concentração de catalisador e pelo armazenamento da resina em uma temperatura inicial adequada. No entanto, a temperatura do ambiente, ou do molde mais especificamente, possui grande influência em outra característica extremamente importante da resina, sua viscosidade.
Fisicamente, a viscosidade representa a resistência de um fluido ao escoamento, mas pode ser interpretada também como a “espessura” de um líquido. O tempo de infusão é diretamente proporcional à essa propriedade, que pode dobrar de valor com uma redução de 10°C na temperatura da resina, como indicado pelo Gráfico 2.
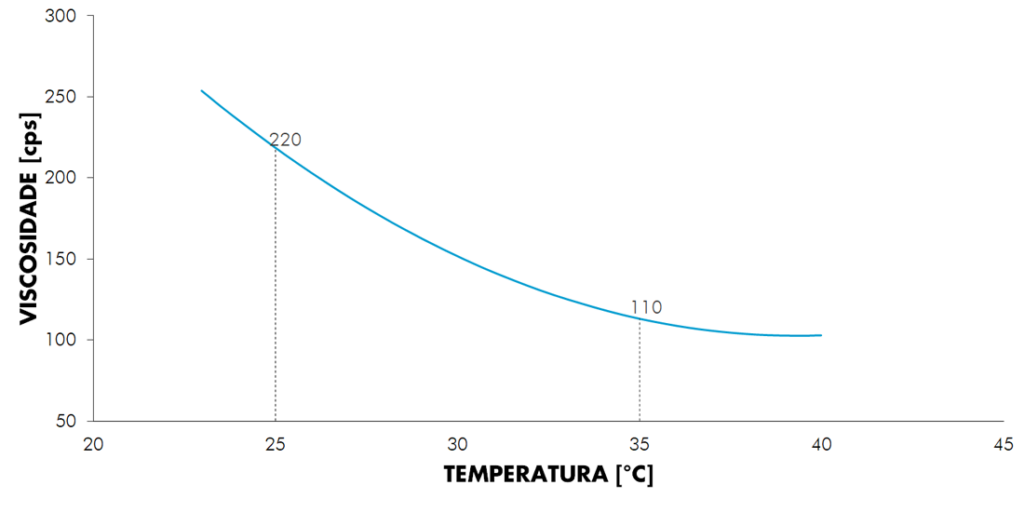
Resinas de laminação manual podem ter até 450 cps de viscosidade, o que tornar a infusão inviável já que o gradiente de pressão não tem força o suficiente para vencer essa resistência ao escoamento e não consegue transportar a resina através do laminado de maneira eficiente. Resinas de infusão, então, devem apresentar viscosidade entre 100 e 200 cps no momento da impregnação.
Moldes de estruturas mais complexas como pás eólicas podem apresentar um sistema de aquecimento para controlar esse aspecto da resina, mas em geral construtores de embarcações são reféns das condições ambientais. É importante, então, realizar a infusão de estruturas dentro das condições ideais de temperatura, que variam entre 20°C e 30°C.
Essas são duas das principais características das resinas de infusão, mas não são as únicas. O pico exotérmico, o teor de sólidos, o intervalo de pico e mais detalhes sobre a formulação de resinas termofixas podem ser encontrados no livro Processo de Infusão a Vácuo em Composites.