Embarcações do tipo multicascos são construídas a partir de cascos de igual tamanho posicionados paralelamente. A estabilidade da embarcação se dá pela alta razão de aspecto entre o comprimento e a boca e não há a necessidade de adicionar uma quilha como em um veleiro com apenas um casco, embora alguns destes barcos a vela usem bolinas para aumentar a eficiência quando se veleja contra o vento.
Em um veleiro, manter as deformações do casco dentro de um limite máximo de 1% é importante porque qualquer distorção na geometria sob carregamento resultará na redução da tensão de estaiamento, aumentando a deflexão dos estais de proa e de popa, modificando a curvatura do mastro, deformando as velas e reduzindo o equilíbrio, o ângulo de orça e a velocidade.
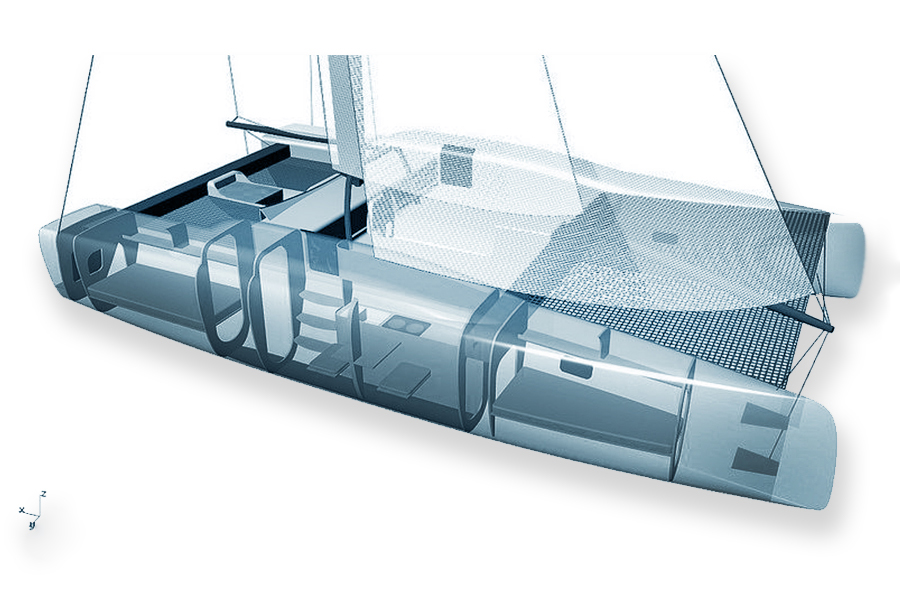
Em embarcações a motor, as deflexões devem ser analisadas com cuidado também para que não haja redução na eficiência hidrodinâmica da embarcação que pode chegar a navegar em velocidades acima de 50 nós. Deflexões permanentes devem ser evitadas porque podem distorcer a forma do casco e afetar as acomodações internas, sistemas de bordo e até mesmo a instalação e funcionamento de equipamentos.
Para limitar as deflexões, deve-se realizar o dimensionamento estrutural adequado da embarcação. Para isso, é necessário ter conhecimento das cargas que atuam na embarcação durante sua operação, o que já um processo complexo em monocascos. Embarcações multicascos ainda estão submetidas a todo um conjunto especial de esforços.
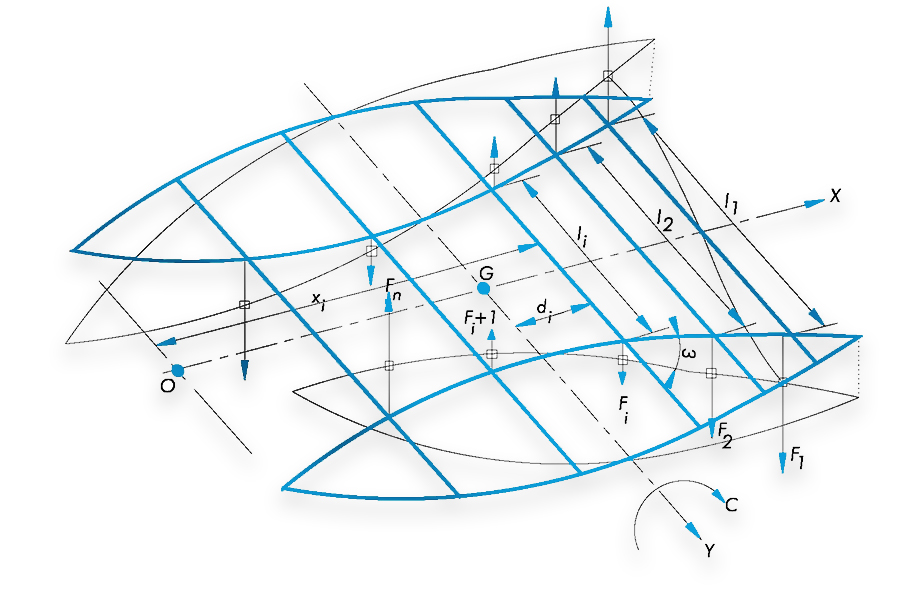
A estrutura deve resistir a deflexões causadas por grandes tensões globais devido ao movimento transversal pelos flutuadores e pelo movimento de caturro, também chamado de pitch, criado pela passagem da crista de uma onda na proa de um dos flutuadores e outra pela popa do outro casco. Este movimento induz uma torção na estrutura central dos multicascos de difícil quantificação.
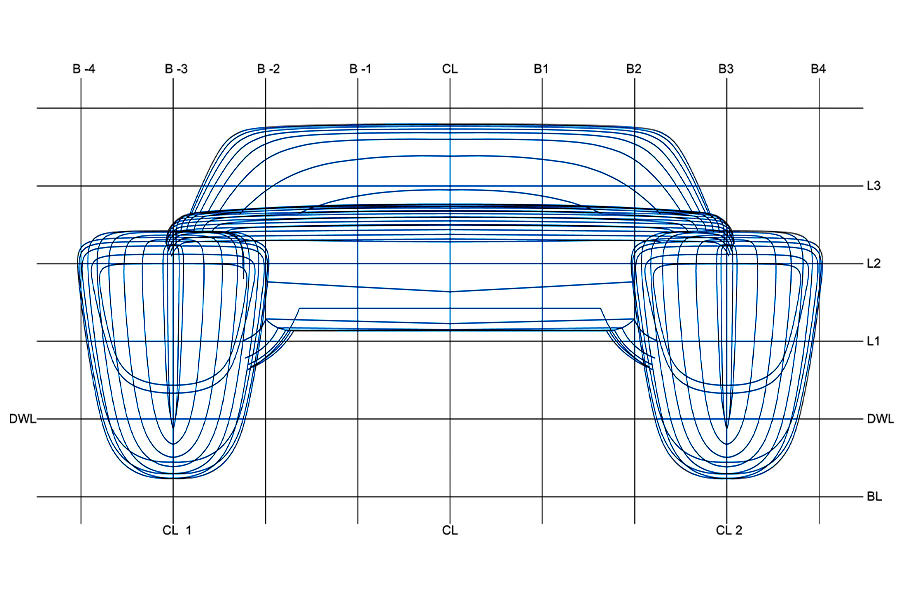
O cálculo torsional em barcos do tipo multicasco deve ter consideração especial principalmente em barcos de alta velocidade. Tanto a estrutura transversal de ligação dos cascos como a sua conexão com o costado e o convés devem ser feitas de forma precisa de modo que o fluxo de tensões nesta estrutura seja dissipado em outras partes do casco.
A ligação desta estrutura com os cascos deve ser feita de modo suave através da transferência de esforços para um conjunto de anteparas que irá descarregar posteriormente os esforços transversais para um sistema de reforços longitudinais.
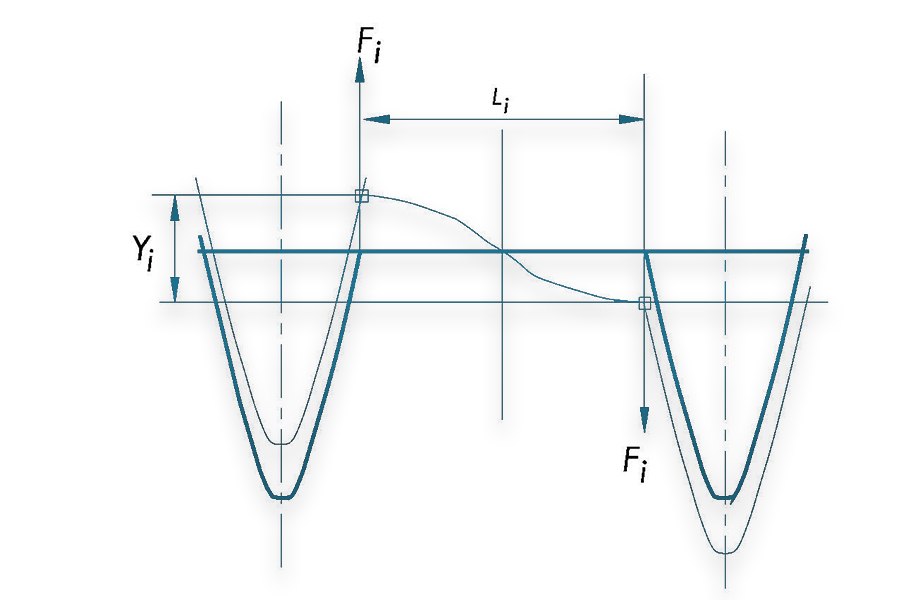
Os materiais com maior razão entre rigidez e peso a disponibilidade dos construtores são os sandwich com núcleo de espuma e faces de alta rigidez construídas a partir de laminados poliméricos com fibras de vidro. Eles representam a opção com maior eficiência e durabilidade, permitindo também uma construção mais rápida e de menor custo.
Embarcações que prezam o alto desempenho, como veleiros de regata, ainda podem optar por núcleos de honeycomb de aramida e faces construídas com prepreg.