Frequentemente os agentes desmoldantes são citados em posts do blog como uma das primeiras etapas da construção das embarcações, então é importante destacar quais são as opções a disposição do construtor e a importância desse elemento que possui profunda influência na qualidade final da peça, na preservação do molde e no tempo de produção.
O agente desmoldante é o primeiro produto a ser aplicado no molde, antes mesmo do gelcoat. Sua função é proteger a superfície do molde e garantir que a estrutura seja facilmente removida com a menor tensão de desmolde possível.
As principais características de desempenho de um agente desmoldante são o tempo de aplicação e o treinamento necessário que os operadores precisam para preparar o molde antes de cada laminação, a quantidade de ciclos de desmoldagem antes de ser necessário reaplicar o produto, a contaminação da peça final e a compatibilidade com todos os materiais do molde e do laminado.
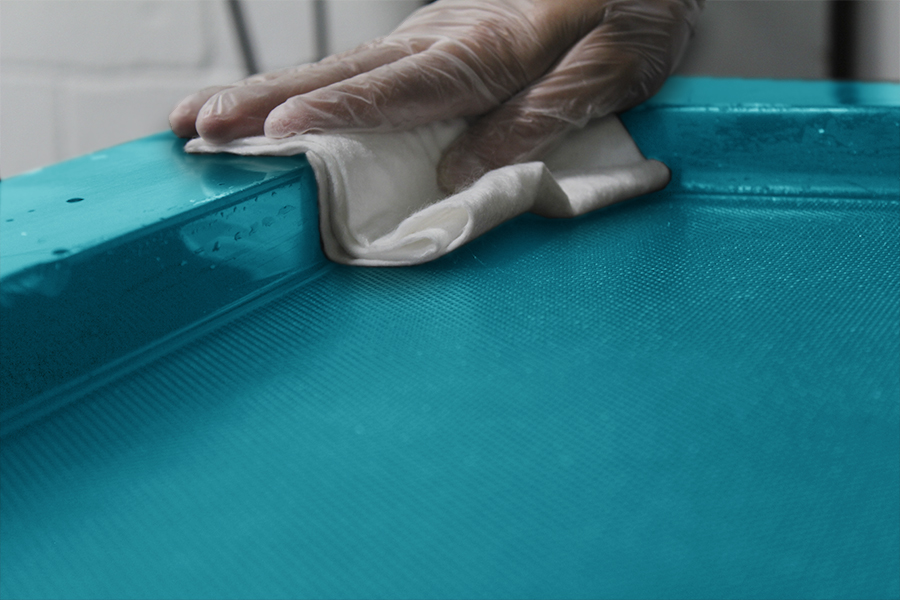
As opções disponíveis no mercado se dividem primeiramente em agentes internos e externos. Agentes internos funcionam com a dissolução de produtos como ésteres de ácidos graxos, estearatos metálicos e ceras nas resinas termofixas. A teoria é que esses produtos migram para a superfície do molde durante a cura da resina, criando um filme de separação entre a peça laminada e o molde, garantindo a desmoldagem e economizando muito tempo ao remover a etapa de aplicação do release agent.
Porém, na prática ainda não existem agentes desmoldantes internos que tenham eficiência o suficiente para que os agentes externos sejam eliminados e, por essa razão, ainda não são muito populares especialmente na indústria náutica, que trabalha principalmente com três tipos de desmoldantes externos: ceras, PVA e semi-permanentes.
Ceras de carnaúba são opção de melhor custo-benefício a disposição dos construtores e possuem fácil aplicação, apesar de consumir algum tempo. Depois da limpeza do molde, a cera deve ser aplicada com movimentos circulares e depois polida. Para moldes novos, essa etapa deve se repetir entre 5 e 10 vezes e depois a cada desmoldagem. Inevitavelmente, resíduos de cera ficarão aderidos ao laminado e uma etapa de limpeza é necessária antes de continuar a fabricação da embarcação.
O desmoldante PVA é um líquido a base de álcool polivinílico de baixa viscosidade. Depois de sua fácil aplicação, álcool e água evaporam deixando apenas um filme uniforme resistente a solventes e ao estireno que adere completamente à peça após o desmolde. A dissolução desse filme deve acontecer por meio da lavagem da peça com água antes de continuar os demais processos de construção.
Esses dois sistemas desmoldante são chamados de camadas de sacrifício, já que criam uma barreira física entre o molde e o laminado. Isso faz com que seja necessário um processo de limpeza das peças e/ou do molde, além da reaplicação do produto a cada processo de laminação, criando duas etapas que aumentam o tempo de produção. Uma maneira de reduzir esses pontos negativos é a utilizados de sistemas semi-permanentes, que podem suportar múltiplas desmoldagens.
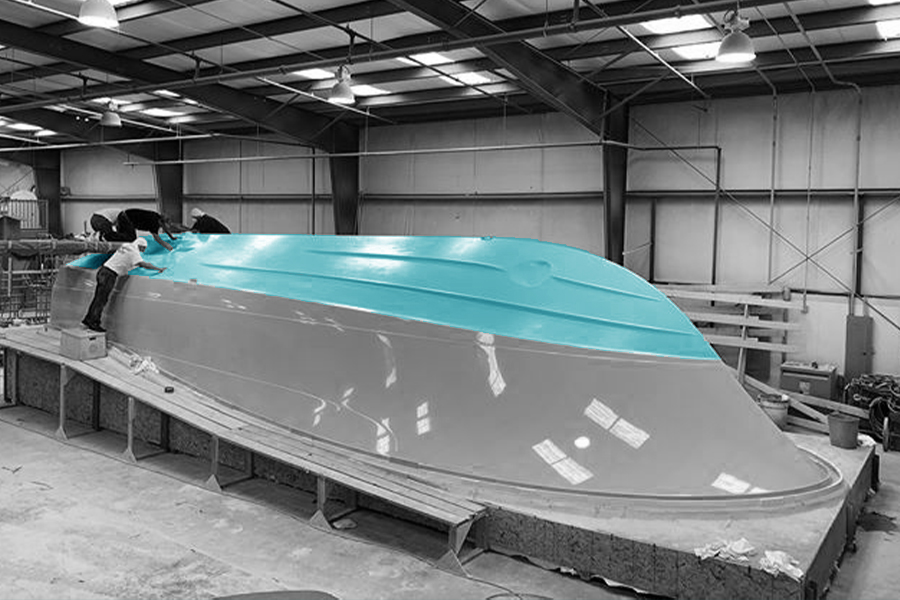
É importante deixar claro que o desmoldante líquido é apenas uma das partes que compõe um sistema semi-permanente, que começa com a limpeza do molde e segue com a aplicação de uma solução primer e de um selante para então ser possível aplicar o desmoldante. Seu princípio de funcionamento é a criação de um filme inerte e durável quimicamente ligado à superfície do molde, garantindo múltiplas desmoldagens e evitando a contaminação do laminado.
Em geral, os construtores náuticos trabalham com agentes desmoldantes externos e as ceras de carnaúba são a opção de melhor custo-benefício em curto prazo, especialmente em projetos one-off. Fabricantes de embarcações seriadas podem recorrer às soluções semi-permanentes que, apesar de apresentarem um custo mais elevado e necessitarem de maior treinamento dos colaboradores, oferecem uma grande economia de tempo de aplicação e processamento da peça após o desmolde, maximizando a produtividade.