A resistência estática dos materiais já foi bastante discutida no blog, inclusive em um post dedicado a definição dos conceitos de resistência e rigidez. No entanto, é muito comum que em condições normais de operação, os materiais não estejam submetidos a uma única condição de carga monotônica e sim a carregamentos cíclicos com tensões que estão teoricamente abaixo do limite de resistência da estrutura.
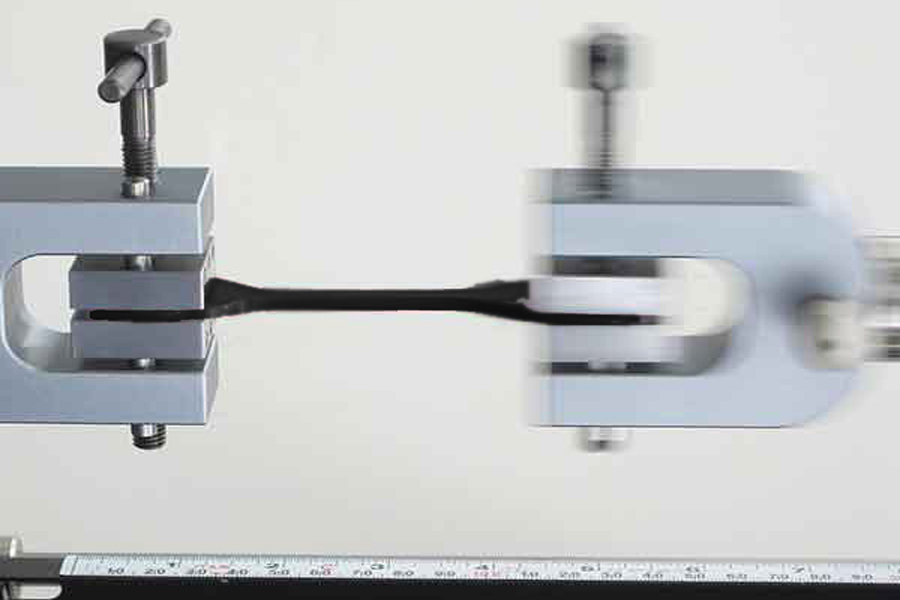
Nesses casos, o modo de falha com o qual o projetista deve se preocupar não é o limite de escoamento e sim a resistência à fadiga, que é a capacidade de um material suportar um número determinado de carregamentos cíclicos, como o apresentado no Gráfico 1. Em geral, quanto maior o número de ciclos que o material deve suportar, menor deve ser a amplitude da tensão SAMP aplicada.
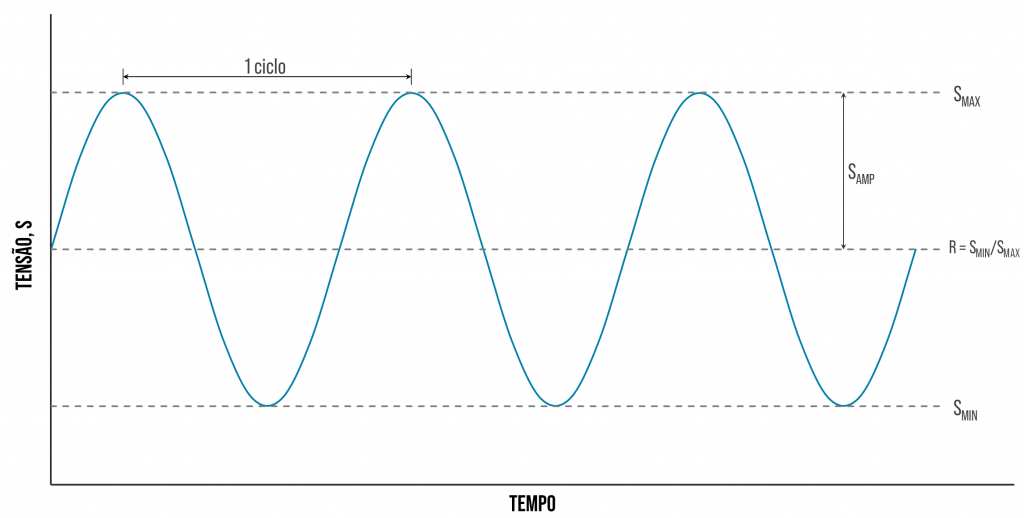
Esse fenômeno e suas causas já foram exaustivamente estudados para materiais metálicos, que falham por fadiga devido ao aumento progressivo de trincas ao decorrer de ciclos de tensão. A resistência à fadiga desses materiais, assim como dos composites, é definida por um par ordenado que combina uma determinada amplitude de tensão SAMP com um número de ciclos N, como indicado no Gráfico 2 que apresenta um diagrama S-N.
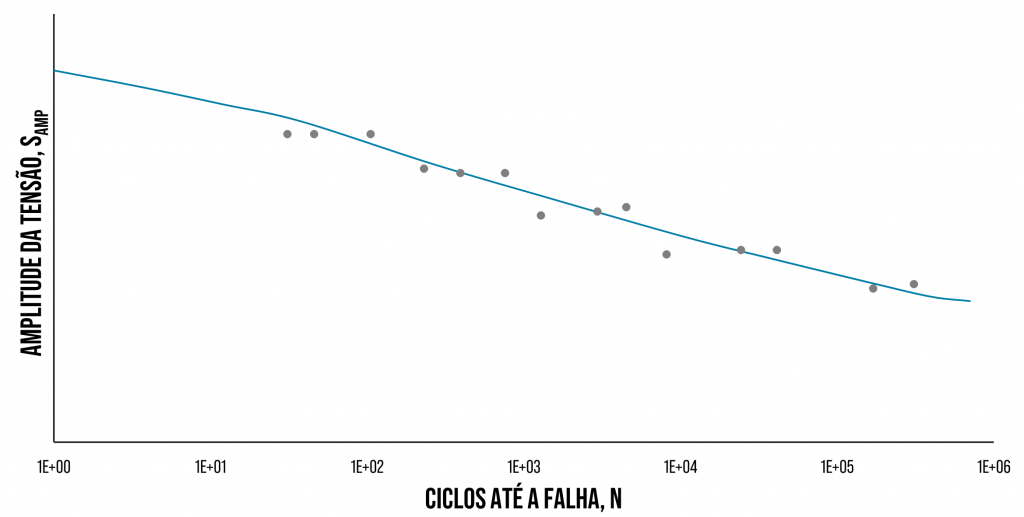
Os projetistas podem trabalhar a fadiga em materiais compostos com as mesmas ferramentas utilizadas para materiais isotrópicos, mas devem ter em mente que os mecanismos que causam a diminuição progressiva da resistência em estruturas construídas com esses materiais são completamente diferentes. Como demonstrado no Gráfico 3, cerca de 50% do dano em materiais compostos acontecem nos primeiros 20% da sua vida em fadiga, enquanto a propagação de trincas em metais se inicia após 75% do limite de ciclos.
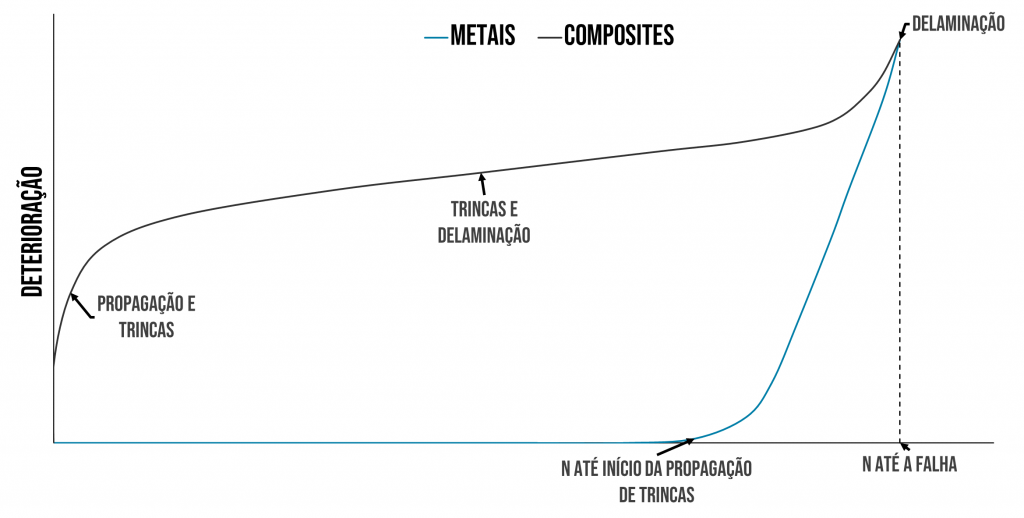
Isso significa que estruturas em composites conseguem conviver bem com algum nível de dano durante a sua vida, enquanto as trincas se propagam rapidamente em materiais isotrópicos. Isso ocorre porque os danos em laminados poliméricos reforçados por fibras ocorrem de uma maneira bastante diferente, com um grande número de eventos microscópicos se desenvolvendo de maneira gradual sobre um grande volume de material.
Por essas razões, os efeitos da fadiga em composites foram negligenciados já que acreditava-se que os níveis de tensão que as estruturas deveriam suportar durante a operação eram muito distantes dos necessários para criação de mecanismos de falha locais. Isso possui algum sentido, considerando que em carregamentos cíclicos com tensões que representam até 60% da resistência ao escoamento, os laminados não apresentam propagação significativa de trincas.
Porém, a expectativa em relação ao uso de composites em projetos de alto desempenho fez com que eles fossem submetidos a carregamentos cada mais severos, fazendo com que a fadiga começasse a se apresentar como um modo de falha importante, principalmente quando as estruturas são submetidas à compressão e cisalhamento, ponto fraco das fibras de reforço que resistem muito bem somente à tensão.
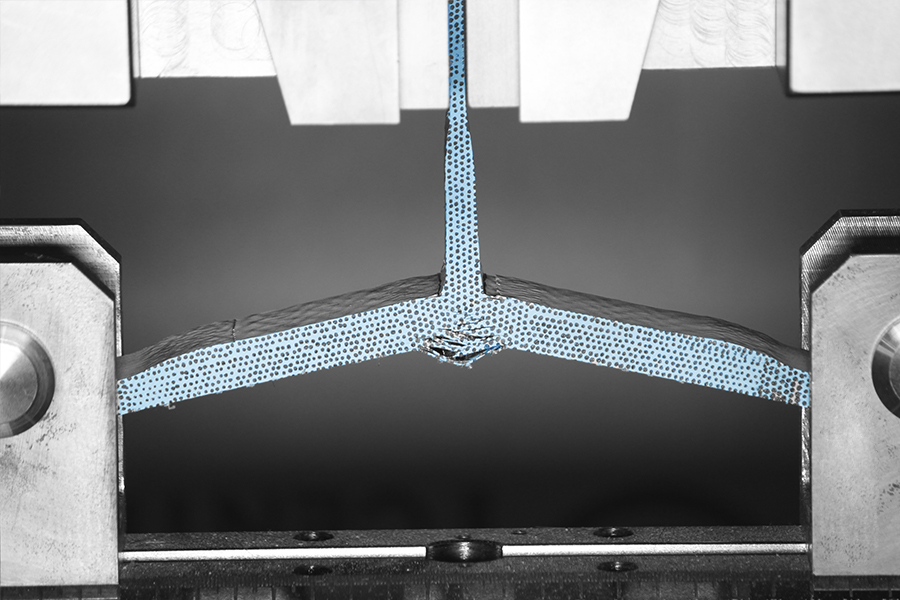
Fatores que podem agravar a deterioração de composites submetidos à carregamentos cíclicos são variações de temperatura, contato com intempéries ambientais e abrasivos químicos, umidade e vazios causados por processos de fabricação que causam um grande índice de microbolhas, que agem como concentradores de tensão.
Como o Gráfico 3 indica, a delaminação é um dos defeitos que acabam se propagando e causando a falha, portanto a adesão entre matriz e reforços representa uma variável importante na resistência à fadiga. Outras variáveis, assim como desempenho de alguns tipos de materiais de reforço e núcleos, serão exploradas na segunda parte do post de resistência a fadiga em materiais compostos.