Materiais compostos são ortotrópicos, o que significa que possuem propriedades mecânicas diferentes quando as cargas são aplicadas em diferentes direções, diferente dos materiais isotrópicos, como metais ou até mesmo um laminado de manta, que apresentam valores de rigidez e resistência independentes da direção do carregamento.
Essas propriedades direcionais, apesar de exigirem uma maior compreensão de como o material funcionam e cálculos estruturais mais complexos, são uma grande vantagem dos materiais compostos. A ortotropia permite ao projetista maximizar as propriedades do laminado em uma direção particular para absorver as tensões, sem precisar adicionar peso em outras direções que não necessitam de tanta rigidez ou resistência.
É por esse motivo que nas fichas de dados técnicos de fibras de alta performance trazem informações sobre as propriedades mecânicas em função das orientações das fibras. Isso permite ao projetista utilizar essas propriedades a seu favor durante o desenvolvimento da estrutura.
A direção das fibras é dada em um ângulo θ que varia em relação à direção longitudinal do laminado, como mostra a Figura 1 abaixo. Uma camada de tecido unidirecional será muito mais rígida e resistente na direção principal do que elas será na direção x e y.
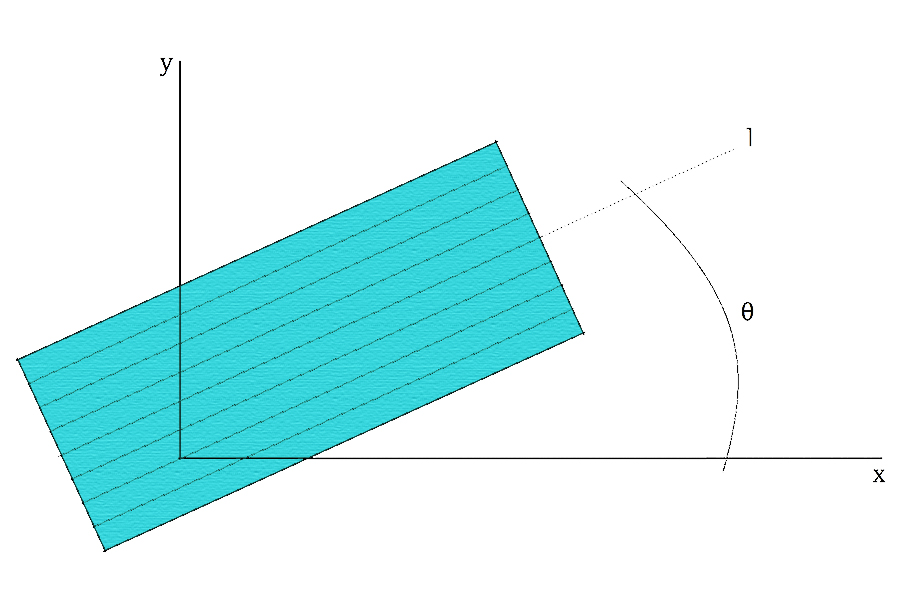
Existem alguns pontos chaves na estrutura de barcos onde o uso da ortotropia pode aumentar a rigidez e melhorar o sistema construtivo com a vantagem de ainda reduzir o peso e reduzir o custo da laminação. Estes locais são as colagens secundárias que a maioria dos barcos está exposta, como no caso da colagem de anteparas com costados e de reforçadores longitudinais e transversais no fundo do casco.
Tradicionalmente estes locais eram laminados com um misto de woven rovings e mantas de fibra de vidro. As mantas são um tipo de material que exibe uma resistência muito baixa e no caso dos woven rovings, além de terem uma baixa estabilidade dimensional devido à sua trama muito frouxa, ainda têm fios na direção paralela ao esforço de colagem que não contribuem nada na resistência de colagem. A única direção que resiste durante esta colagem é o filamento da trama que está a 90º de direção.
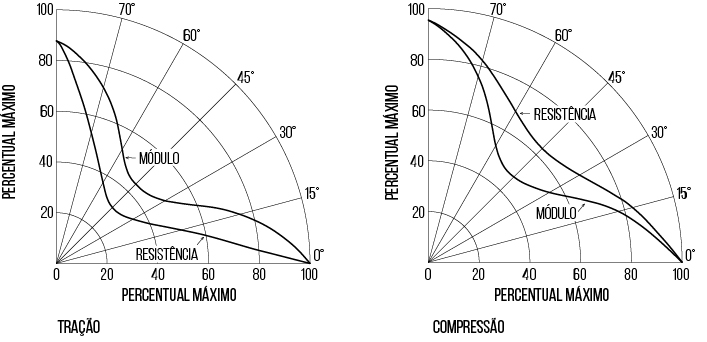
Atualmente, estas partes de um barco são coladas com tecidos biaxiais nas direções de [±45], o que possibilita que as duas direções do laminado trabalhem para fixar a antepara além de permitir uma perfeita acomodação do laminado em uma posição onde as superfícies fazem um ângulo fechado. Outra vantagem também é que os tecidos mutidirecionais podem ser cortados em fitas de modo a reduzir a área de colagem e reduzir o peso.
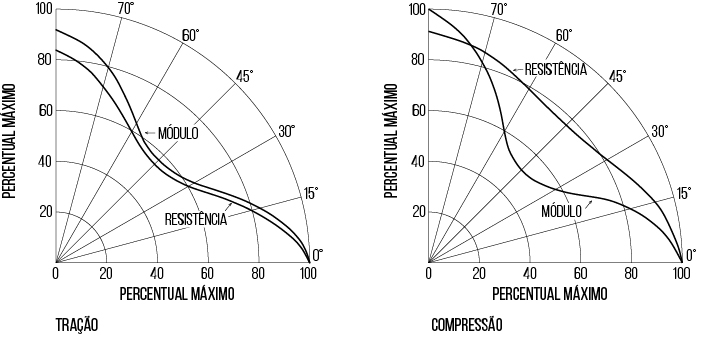
Levando-se em conta que um barco tem uma série de locais e uma grande área sujeita a laminação secundária, é possível imaginar o tremendo ganho de peso que uma embarcação pode ter com o uso perfeito da direcionalidade dos tecidos.
O uso de tecidos triaxiais também é muito importante na construção de estruturas internas. Ao contrário da construção utilizando tecidos do tipo woven roving nas direções de [0/90] os tecidos triaxiais construídos nas direções de [0/±45] podem proporcionar o balanço correto de propriedades mecânicas estruturais para as vigas das transversais e longitudinais de um barco. Nestas peças as direções preferenciais são [±45] para as almas das vigas e [0] para os flanges. Nestes casos, os tecidos triaxiais devem ter um balanço de 50% de fibras nas direções oblíquas de [±45] e o restante dos 50% na direção de [0]. Estas estruturas devem ser coladas e laminadas ao casco com tecidos nas direções de [±45].