O acabamento superficial do casco é um aspecto fundamental da construção náutica e um dos fenômenos que mais ameaça essa característica é o print-thru, que é que a impressão visível das fibras de reforço ou material de núcleo no gelcoat.
Qualquer construtor de embarcações vai destacar que o reparo desse tipo de defeito exige uma grande alocação de recursos. O trabalho é manual, demorado e pode não apresentar o resultado desejado. É interessante, então, conhecer as causas e formas de prevenção para evitar que esse tempo de produção seja dedicado à atividades de retrabalho.
A principal causa do fenômeno é a diferença entre os coeficientes de expansão térmica da resina e da fibra. Qualquer material sofre alterações em suas dimensões em função da variação de temperatura e, em geral, quanto maior a temperatura, maiores são suas dimensões. Porém, a taxa de deformação da resina quando acometida pelo calor da reação exotérmica de cura é muito maior do que a deformação da fibra. Quando a temperatura volta a cair, a resina se contrai e cria uma tensão residual que é aliviada ao longo de vários meses e até mesmo anos.
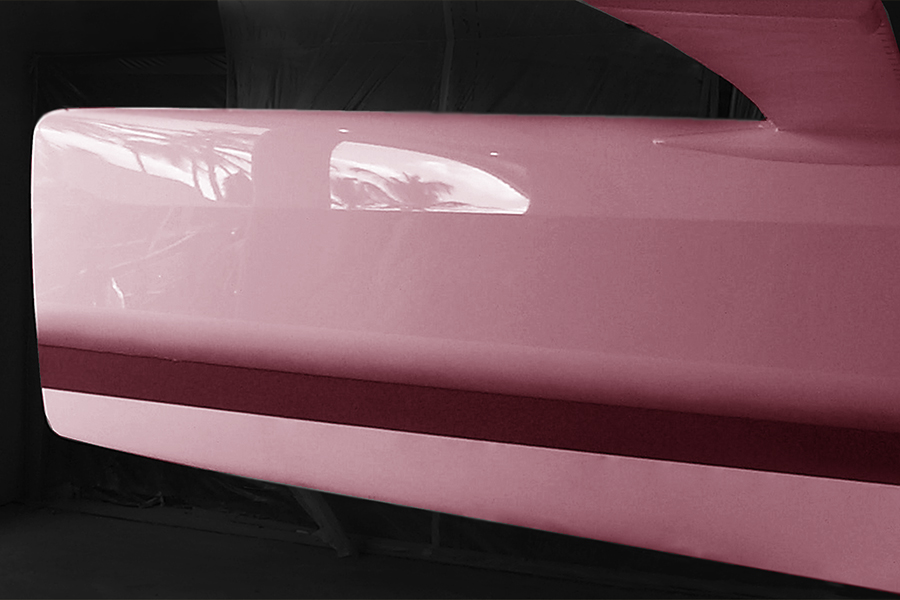
Durante esse período de alívio da tensão residual, a impressão das fibras pode se tornar visível e prejudicar o acabamento da superfície meses após a construção da estrutura. É por esse motivo que o reparo logo após o desmolde da peça pode não resolver o problema completamente, já que ele pode reaparecer muito tempo após a conclusão da fabricação do barco. É muito mais efetivo atacar as causas e utilizar mecanismos para suavizar o fenômeno.
A resina poliéster é a mais popular na construção náutica por conta de seu excelente custo benefício, mas ela apresenta alta contração após a cura, ou seja, cria tensões residuais que acabam deixando a peça suscetível ao print-thru. Além disso, a quantidade de ésteres presentes em sua molécula faz com que seja muito suscetível à hidrólise, o que diminui sua resistência química. A utilização de outras resinas com menor contração e maior capacidade de proteger as primeiras camadas de reforço é bastante indiciada e as resinas estervinílicas são normalmente escolhidas para exercer esse papel.
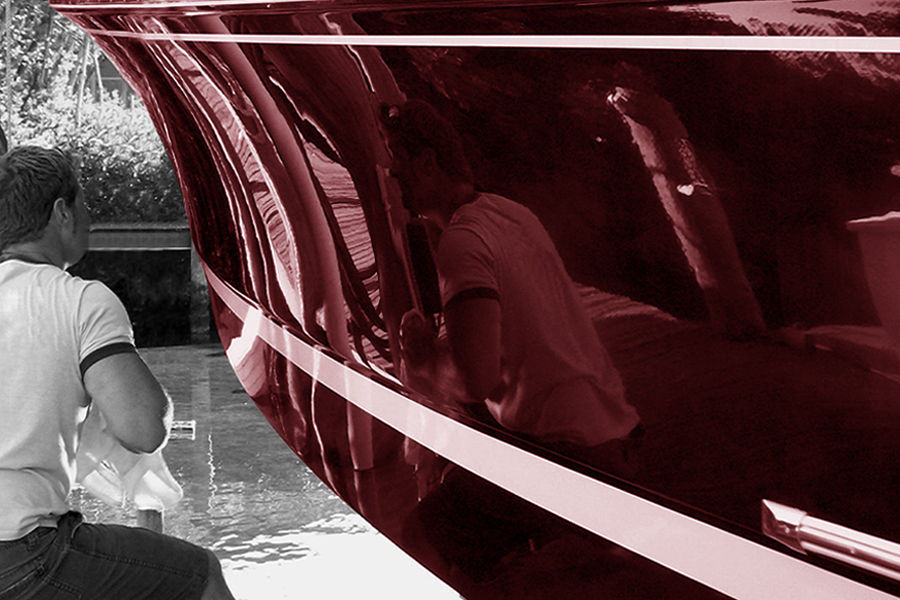
Obviamente, a resina epoxy se sairá melhor em todos esses aspectos, mas seu custo e, muitas vezes, a necessidade de realizar pós-cura, acaba afastando os construtores náuticos que utilizam reforços de fibra de vidro. A resina estervinílica se oferece como uma opção de melhor custo benefício nesse aspecto.
Apesar de ajudar, a troca de resina não resolve o problema porque a contração pode ser amenizada, mas está presente qualquer que seja o material. Esse fator combinado com o uso de pressão nos métodos de vacuum bag e infusão a vácuo faz com que sejam necessários outros mecanismos para amenizar essa questão, começando com a laminação do skin coat, normalmente composto de duas camadas de manta de 300 g/m² seguidas por mais duas de 450 g/m². O peso adicional de um laminado que não contribui estruturalmente para a estrutura é o preço a se pagar para obtenção de um acabamento primoroso.
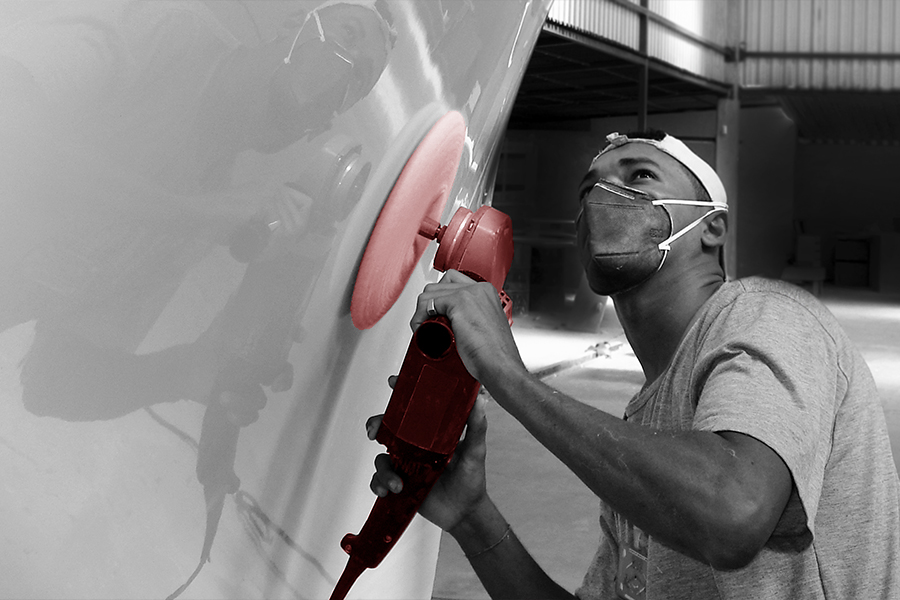
As fibras não são os únicos elementos a serem impressos na superfície do gelcoat, que também pode ser marcado pelos groovings dos materiais de núcleo. Se o skin coat não for o suficiente para impedir isso, é necessário recorrer ao uso de núcleos de poliéster como o Soric TF, desenvolvido para ser um print blocker. Outra alternativa para o construtor pode ser alterar a espessura e profundidade dos groovings utilizados e até mesmo alterar a configuração utilizada.
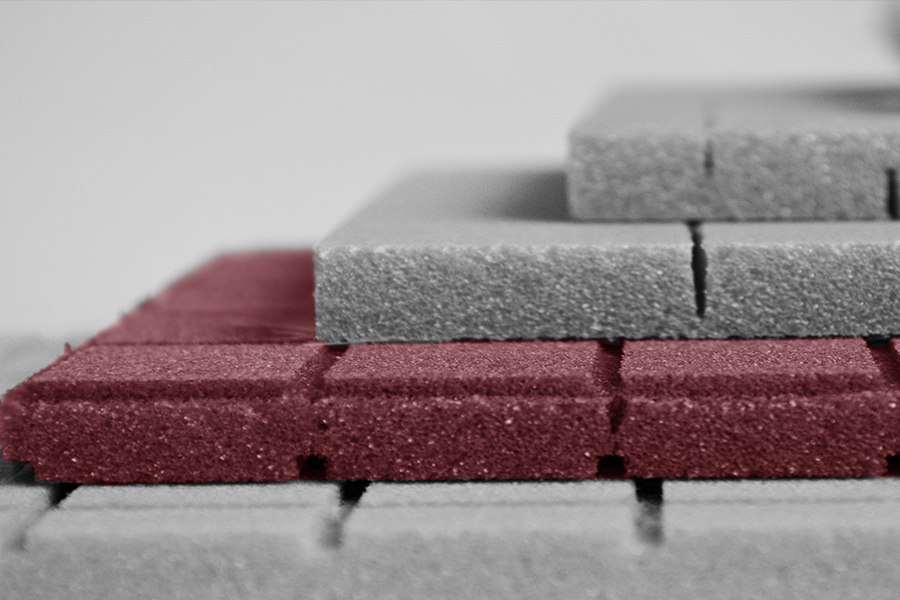
O print-thru é um fenômeno que não causa prejuízos estruturais, mas definitivamente é uma dor de cabeça para o processo de construção náutica, causando centenas de horas de retrabalho em uma linha de produção em série. Apenas o conhecimento e a prática farão com que construtores consigam evitar ou amenizar esse tipo de problema.