A madeira balsa representou uma revolução na construção em materiais compostos, sendo o primeiro material de núcleo utilizando em uma construção sandwich na década de 1940. Apesar da teoria sobre a eficiência desse tipo de estrutura estar estabelecida há algum tempo, não foi isso que fez a madeira balsa entrar em cena.
Durante a Segunda Guerra Mundial, os esforços de guerra causaram uma escassez de aço em todo o mundo, obrigando todos os países a encontrarem alternativas. Foi um período em que os materiais compostos tiveram um grande desenvolvimento e foi quando a madeira balsa foi utilizada na construção do bombardeiro Havilland DH.98, a aeronave mais veloz da época.
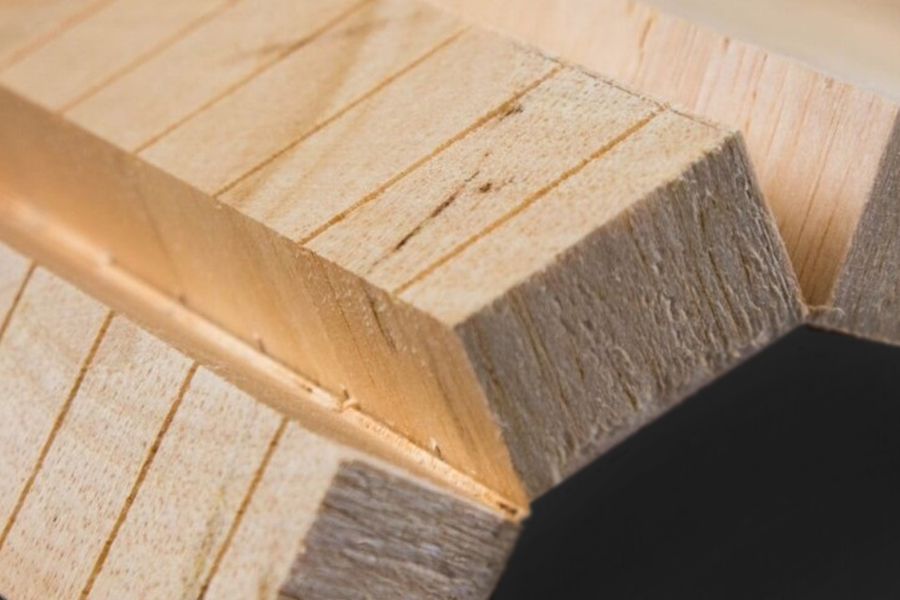
O “Mosquito”, como era mais conhecido, foi construído em madeira balsa e madeira compensada. Como aconteceu com diversos materiais desenvolvidos nesse período, ao fim da guerra a construção náutica adotou o uso da madeira balsa também, incentivada por sua baixa densidade e excelentes propriedades mecânicas.
Em comparação com outras madeiras, a balsa é muito leve, chegando a ter 150 kg/m³, embora muitas versões possuam densidades acima de 250 kg/m³. Como sua microestrutura é formada por células dispostas na direção transversal à placa, as resistências à compressão e ao cisalhamento são relativamente altas.
A forma de balsa mais utilizada atualmente é a End Grain, madeira originária de florestas tropicais da América do Sul e cultivada principalmente no Equador.
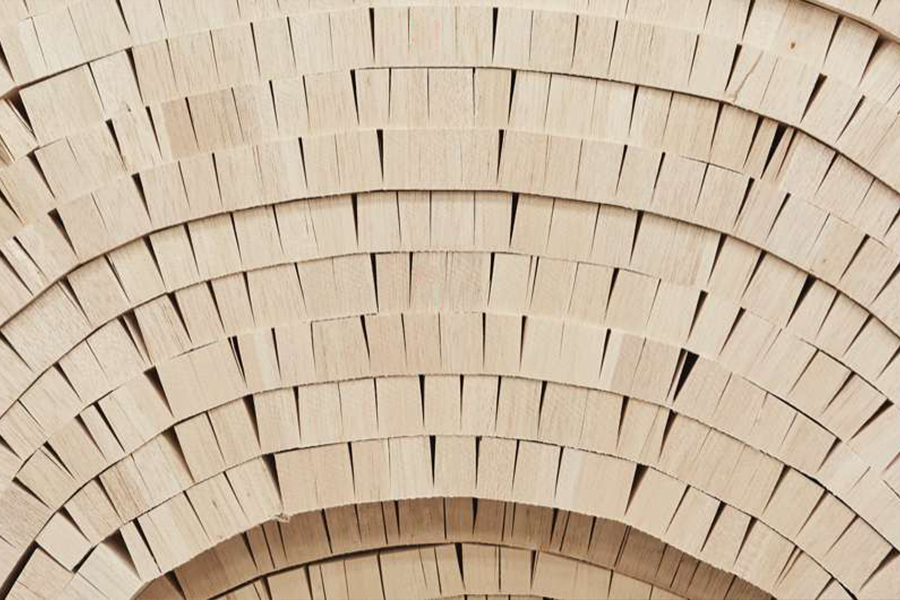
Por ser um material orgânico, a sua densidade é muito variável. Para contornar esse problema, os fabricantes fatiam a madeira extraída em pequenos sarrafos que são colados para formar um bloco a partir do qual são fatiadas placas com quadrados de densidades parecidas, o que resulta em um material com densidade media equalizada, mas cada placa vai possuir um peso diferente.
A facilidade de processamento da balsa também é uma vantagem. Ela pode ser utilizada em placas planas ou com groovings GS para conformação em curvaturas acentuadas. A maior parte dos construtores amadores trabalham com as ferramentas necessárias para o processamento dessa madeira e ela é compatível com diversos processos de laminação.
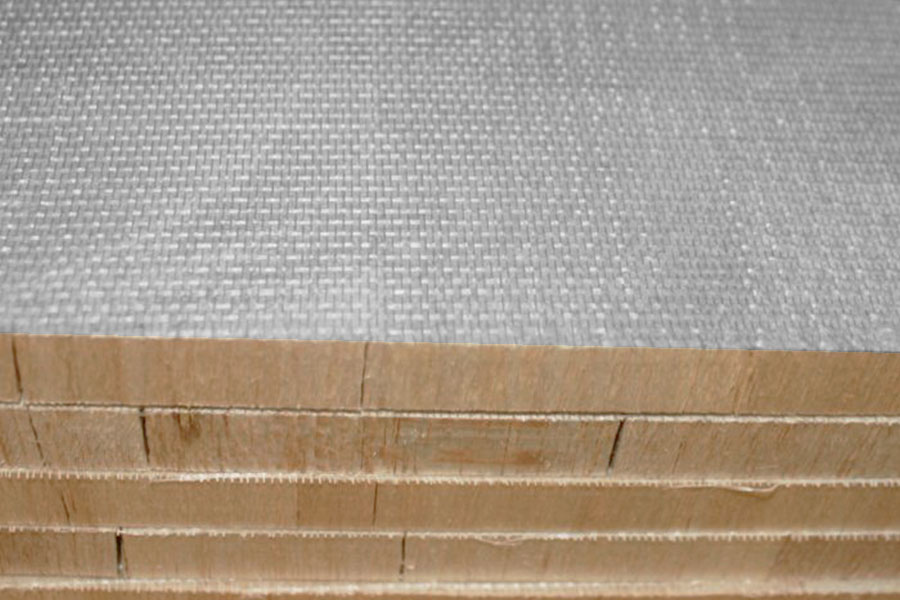
As maiores dificuldades relacionadas ao uso de balsa começam com sua alta absorção de resina. A mesma microestrutura celular que fornece ótimas propriedades mecânicas, é o que faz com que o núcleo tenha uma alta absorção de resina pelos poros e através dos cortes da placa e isto faz que o material absorva muita resina no processo de laminação.
Para reduzir esse problema, o construtor pode iniciar o processo de laminação depositando sobre a placa de madeira de balsa uma camada de resina de alta viscosidade com tempo de gel curto, selando sua superfície e impedindo a entrada excessiva de resina, o que aumenta o peso do laminado sem realmente trazer benefício estrutural.
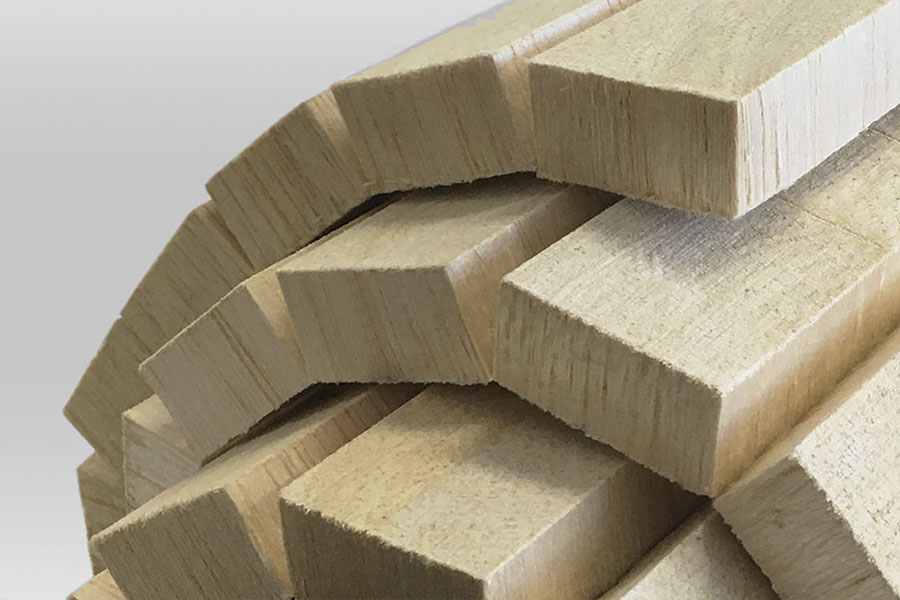
As células abertas que absorvem resina também são as que possibilitam a entrada de água e umidade, que causam a degradação do material orgânico. Para evitar esse processo, a construção em balsa também exige o uso de resina epoxy, que possui uma resistência à entrada de água muito maior do que a poliéster ou a estervinílica. Porém, uma vez que ocorra a entrada de água, a degradação ocorre em alguns anos e o material deve ser substituído, muitas vezes por espumas PVC que são mais leves e possuem células fechadas que não absorvem umidade.
O construtor deve estar sempre atento ao utilizar esse tipo núcleo para construção de embarcações. Em geral, a balsa faz com que as estruturas fiquem mais pesadas e durem menos quando comparada à embarcações construídas com núcleos de espuma PVC.