Muitos dos avanços tecnológicos da história foram impulsionados por grandes conflitos da humanidade. A história do desenvolvimento da resina poliéster, da invenção da fibra de vidro e até mesmo do uso de painéis sandwich já foram contadas no blog e estão intimamente ligadas aos acontecimentos da II Guerra Mundial. O post de hoje fala sobre como todos esses avanços criaram os elementos necessários para a construção do plástico reforçado com fibra de vidro, materiais que hoje dominam a indústria náutica.
Antes do desenvolvimento dos plásticos termofixos, os barcos eram em sua maioria construídos com materiais orgânicos como madeiras e peles de animais. Plywood estava começando a se popularizar no século XX, mas havia um ímpeto para a criação de um método que pudesse realizar a construção de toda a embarcação de uma só vez e permitir a moldagem de geometrias complexas com duplas curvaturas.
O responsável pelo criação desse procedimento é o engenheiro Ray Greene que, apesar de ter construído milhares de embarcações durante sua vida, gostava de se definir como um inventor e não como um construtor de barcos. Seu amor por embarcações se aprofundou principalmente depois que seu pai comprou uma propriedade no Michigan próxima da Transverse Bay, onde ele e seus irmãos aproveitavam tudo que a baía tinha a oferecer.
Seu vontade de entender os fenômenos da química criou episódios interessantes desde sua infância, quando destruiu a pia da cozinha tentando produzir refrigerante em sua casa utilizando gelo seco e desprezando a expansão dos gases em um recipiente fechado. Seu rigor e vontade de alcançar o melhor resultado possível podem ser explicados a partir da admiração que tinha pelo seu pai, que trabalhava como chefe de metalurgia e diretor de pesquisa em uma companhia em Ohio.
Herman Greene era seu incentivador ao mesmo tempo que era extremamente exigente com seu trabalho. O primeiro barco que Ray construiu quando tinha 12 anos foi imediatamente jogado fora depois que ficou pronto, já que seu pai ficou decepcionado com o resultado. Por outro lado, Herman deu as ferramentas e o apoio necessário para que o filho pudesse fundar o estaleiro Ray Greene & Company na garagem da família em 1929, o que permitiu que fabricassem os barcos que pagariam pelo seu curso superior em engenharia mecânica e química. Posteriormente, seria o que também permitiria que os irmãos de Ray fossem para faculdade após a morte de seu pai em 1934.
Foi na Universidade de Ohio que Ray começou a estudar resinas sintéticas, justamente com o objetivo de criar um método que permitisse a construção de embarcações leves e resistentes. As primeiras tentativas foram realizadas utilizando plásticos que necessitavam de curas em condições controladas de temperatura e pressão em autoclaves, limitando o tamanho das embarcações.
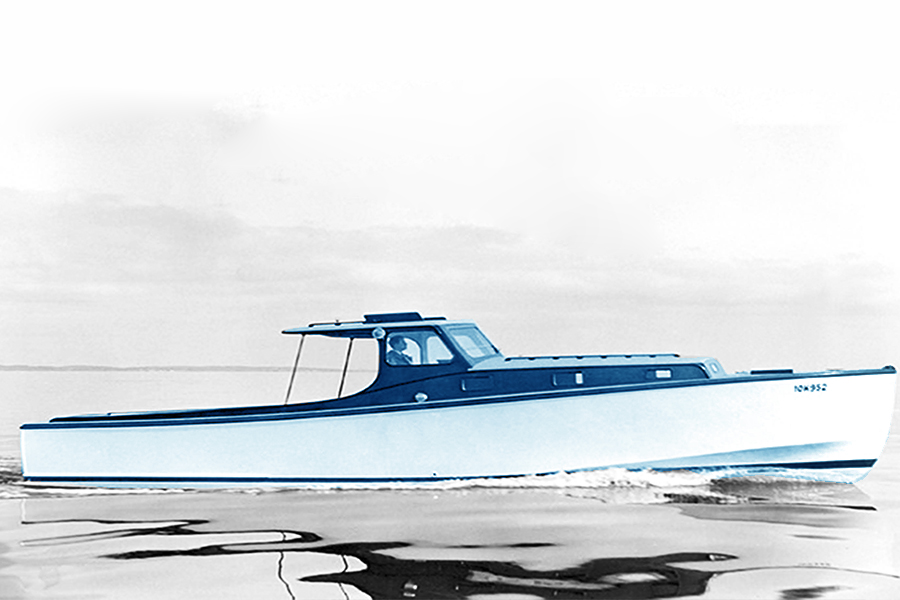
O resultado que buscava foi alcançado durante o desenvolvimento de sua tese de mestrado que originalmente se chamava “Choosing Plastics for Boat Building”. Ao receber o primeiro rascunho, seu orientador questionou se o trabalho era sobre engenharia mecânica ou arquitetura naval e sugeriu uma pequena mudança no título que se tornou “Chooosing Plastics for Large Objects”, sem mencionar em nenhum momento que o primeiro grande objeto construído em composites foi um barco.
Todas as matrizes poliméricas que Ray havia experimentado até o momento eram frágeis e apresentavam pouca resistência, deixando evidente a necessidade de um material de reforço. Depois de tentar uma infinidade de opções, suas conexões com a Owens-Corning lhe renderam a metade do primeiro lote de fibra de vidro que a empresa produziu em 1941.
Por meio de colegas pesquisadores que trabalhavam na American Cyanamid, Greene conseguiu também um galão da primeira resina termofixa capaz de ser curada em temperatura ambiente. Sendo o primeiro homem no mundo com esses dois elementos em mãos simultaneamente, ele foi o responsável por criar os procedimentos para construção da primeira grande peça estrutural de plástico reforçado com fibra de vidro, dando o primeiro passo em direção aos composites como se conhece hoje em 1942 e revolucionando a indústria náutica.
Décadas mais tarde, seu orientador contou que o tema de sua tese, a seleção de plásticos para construção de peças estruturais, foi motivo de dúvida entre os professores do departamento, que permitiram que o trabalho prosseguisse apenas por conta do entusiasmo do estudante. Vários fabricante de polímeros na época responderam aos pedidos de Ray Greene informando que a ideia de utilizar plásticos em peças estruturais era simplesmente impossível.

Com seu ímpeto de cientista-físico-inventor, conhecimento profundo sobre construção náutica e disciplina desenvolvida pelos altos padrões de exigência de seu pai, Ray Greene não encontrou apenas uma maneira de construir embarcações com plásticos reforçados com fibra, como criou uma indústria que revolucionou a construção de estruturas de alto desempenho.
O livro Processo de Infusão a Vácuo traz mais informações e curiosidades sobre a história dos materiais compostos, além de informações sobre as propriedades mecânicas dos composites e sobre os principais processos de fabricação.