Que está acostumado a fazer infusão com resinas do tipo poliéster vai ter que se adaptar a uma nova realidade técnica quando for trabalhar com infusão com resinas do tipo epoxy. A propriedade mais importante das resinas de infusão, sejam elas poliéster ou epoxy, é a baixa viscosidade, mas somente ela não garante o sucesso do processo.
Independente do tipo de resina que vai ser utilizada o tempo que a resina vai levar para preenchê-lo pode ser ajustado pela quantidade e espaçamento das linhas. Se o construtor sabe de antemão que a resina demora dez minutos para percorrer 1 m de comprimento no seu laminado, ele pode montar uma quantidade de linhas espaçadas com esta mesma distância e alimentadas por várias tubulações que mantenham a vazão de resina necessária para preencher o laminado.
Como regra geral, qualquer tipo de infusão deve terminar entre 45 e 60 minutos. Mesmo que a resina seja infundida por partes, a primeira delas vai começar um processo exotérmico 30 minutos depois de entrar no molde. Aumentando a temperatura dentro de uma parte do laminado e na superfície da forma, a temperatura global em volta do molde tende a aumentar e o tempo de trabalho da resina diminuir.
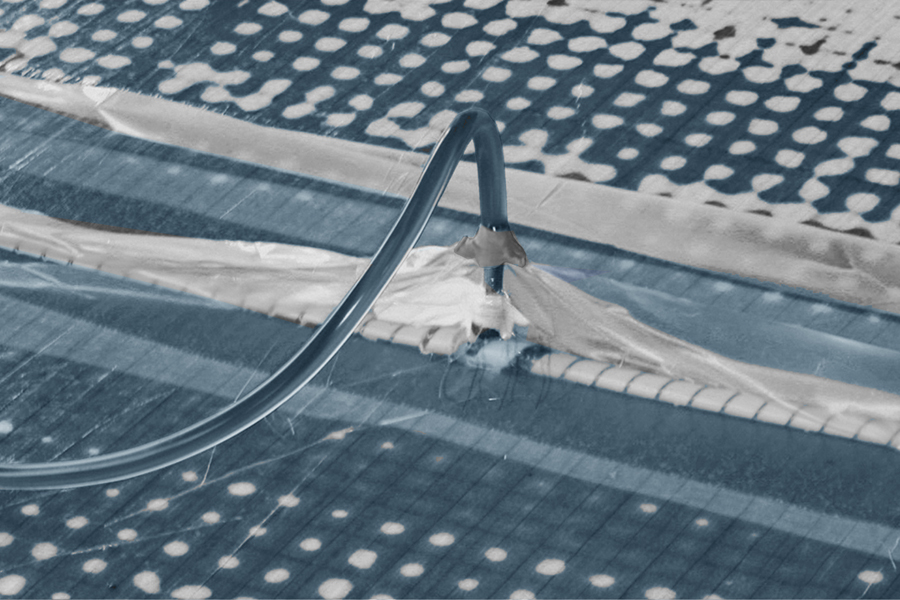
Resinas com um tempo de trabalho muito longo tendem chegar à linha de vácuo antes de aumentar a viscosidade, o que pode causar a sua recirculação dentro do sistema. As resinas para infusão a base de epoxy devem ter uma viscosidade menor que 180 cps entretanto a maioria das resina epoxy tem viscosidade superior a 1200 cps e algumas de uso geral tendem a uma viscosidade superior a 10.000 cps o que inviabiliza a infusão. Somente algumas resinas epoxy são formuladas corretamente para serem usadas na infusão.
Se o construtor tentar usar uma resina não apropriada para infusão e reduzir artificialmente sua viscosidade pela adição aleatória de alguma outra substancia é bem provável que as propriedades finais da resina vão ser afetadas e provavelmente o Tg vai ser muito baixo podendo gerar uma cura desbalanceada.
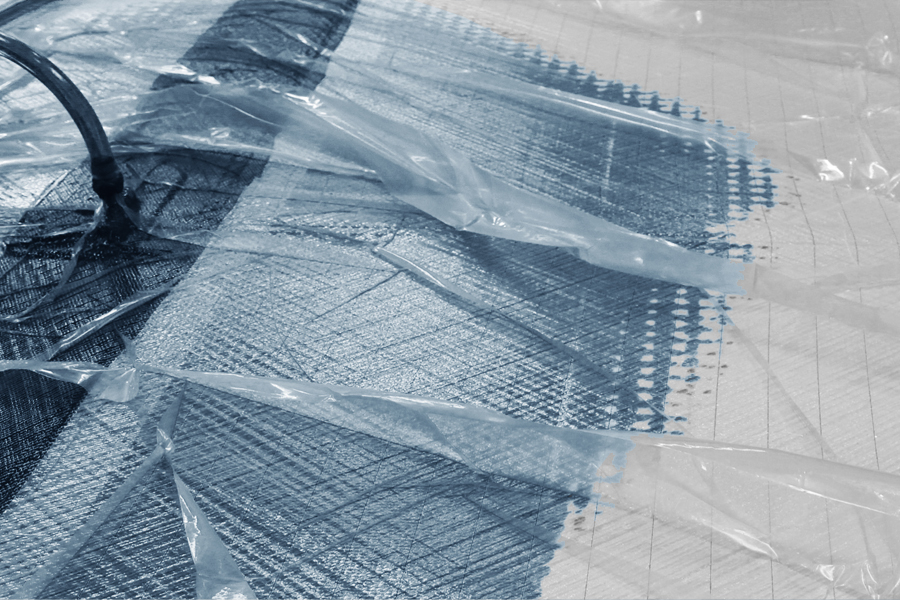
Ao contrário da resina de laminação, que tem um tempo curto de gel e um tempo relativamente grande até a cura total, a resina de infusão tem um tempo mais longo no início do processo, mas tem uma cura parcial mais aceitável para a desmoldagem logo após o pico exotérmico da resina, que acontece entre 40 a 50 minutos depois de sua catalisação dependendo do tipo de endurecedor usado. Logo após a resina preencher a cavidade do laminado, ela deve estar pronta para curar, mesmo que parcialmente, de modo a não retornar para a linha de vácuo, e se tornar necessário circular mais resina pelas linhas.
Por último, as resinas a base de epoxy somente devem ser usadas pelo construtor que tenha bastante experiência com o processo, pois estas resinas apresentam grande temperatura de exotermia durante a infusão, podendo chegar a criar pontos dentro do laminado com temperaturas acima de 100°C. Durante a infusão com resinas epoxy, tanto os filmes de vácuo quanto o restante dos produtos de fechamento da bolsa de vácuo devem resistir a temperaturas acima de 140°C.