A resistência e a rigidez de materiais e estruturas são frequentemente citadas nos posts do blog como importantes requisitos de projeto. Uma ferramenta interessante para ajudar a esclarecer e definir esses conceitos é o diagrama de Tensão (σ) x Deformação (ε) de um material.
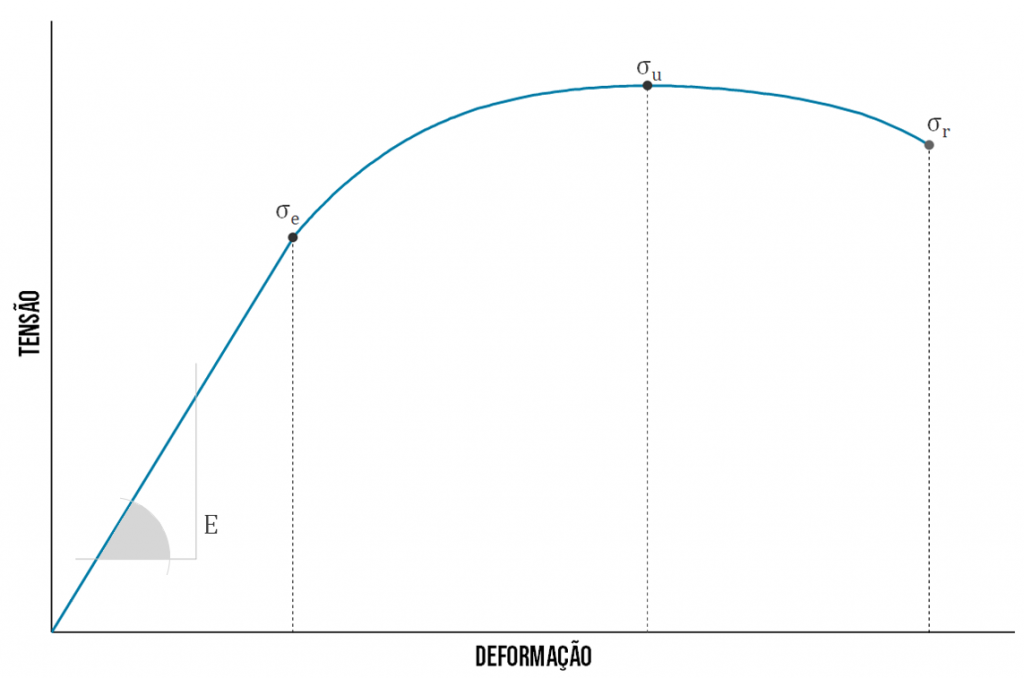
O Gráfico 1 apresenta esse diagrama produzido a partir de um ensaio de tração, que consiste em aplicar uma carga axial que desenvolve um deslocamento constante em um corpo de prova. A tensão σ no corpo de prova é determinada a partir da razão entre a carga P necessária para impor esse deslocamento pela área A da seção transversal do corpo de prova, ou seja:
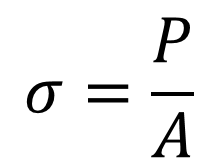
Já a deformação ε é a razão entre o comprimento Li do corpo de prova em um determinado momento pelo comprimento inicial Lo da amostra, ou seja:
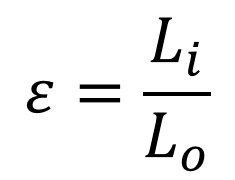
A resistência de um material é a máxima tensão que ele pode suportar antes que um determinado fenômeno ocorra. O Gráfico 1 destaca três eventos importantes demarcados pela resistência ao escoamento σe, pela resistência máxima σu e pela resistência à ruptura σr.
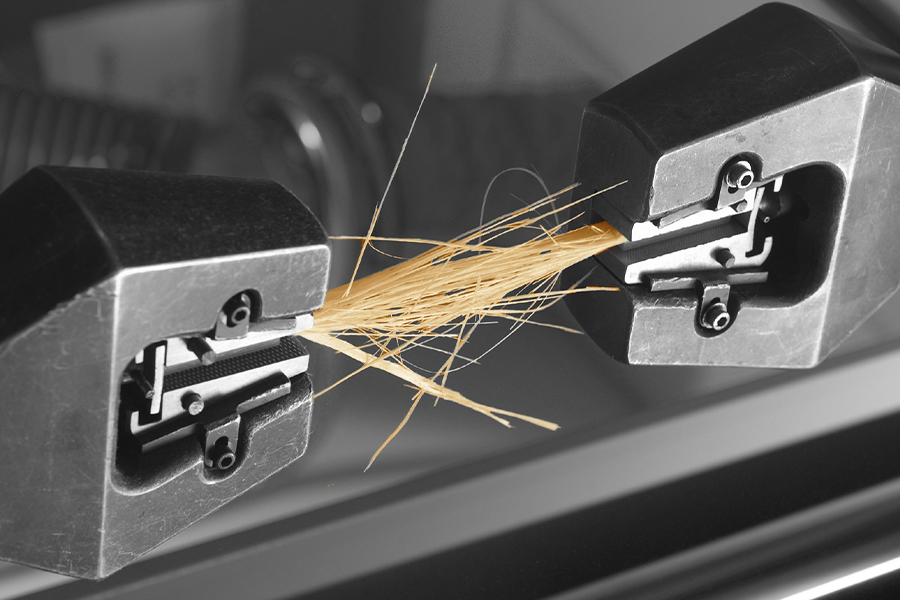
A resistência ao escoamento σe é amplamente utilizada como critério de projeto porque representa o limite entre dois tipos de comportamento de um material, o elástico e o inelástico. Abaixo da tensão de escoamento, o corpo de prova se comporta de maneira linear e a tensão aplicada é proporcional à deformação causada respeitando a Lei de Hooke:
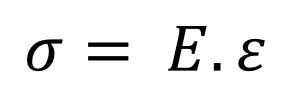
Até esse limite, qualquer deformação pode ser desfeita se a carga parar de agir no corpo de prova. Após o limite, as deformações são permanentes e comprometem a geometria do corpo de prova.
Depois de a carga aplicada causar uma tensão maior do que a resistência ao escoamento, o crescimento da tensão acontece de maneira mais lenta até alcançar a tensão máxima σu e, após esse ponto, a carga necessária para continuar a deformá-lo em uma taxa constante decai até a tensão de ruptura σr. Como deformações permanentes não são desejadas em nenhuma estrutura, normalmente os projetistas trabalham dentro do limite de escoamento e com uma certa margem de segurança.
Já a rigidez de um material pode ser definida como sua resistência à deformação, sendo representada pelo módulo de elasticidade E que no Gráfico 1 aparece como o coeficiente angular da reta que caracteriza o comportamento do material na região elástica. Manipulando a Lei de Hooke, podemos claramente observar que quanto maior a rigidez do material, menor é a deformação que uma determinada tensão causará:
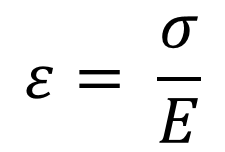
Já a rigidez à flexão de uma estrutura é o produto entre o módulo de elasticidade E do material que a compõe com o momento de inércia I da sua seção transversal, de acordo com a equação:
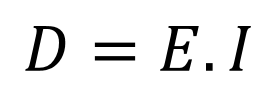
O módulo de elasticidade E de um laminado é uma propriedade mecânica que pode ser determinada por meio de ensaios mecânicas ou estimado a partir das propriedades de seus constituintes por meio da micromecânica. Já o momento de inércia I da seção transversal depende da geometria da estrutura, aumentando exponencialmente quanto maior for a espessura dessa seção.
Em suma, a resistência de um material diz respeito à quanta tensão ele é capaz de suportar antes de escoar ou se romper. A rigidez de um material pode ser quantificada por seu módulo de elasticidade, representando fisicamente a resistência que um material tem a deformação. Já a rigidez à flexão de uma estrutura depende não só da rigidez do material que a compõe, mas também de sua geometria.