Apesar de o método de laminação manual ser capaz de entregar laminados com boa resistência, durabilidade e aparência cosmética, o uso de vaccum bag é capaz de fabricar uma estrutura mais leve e mais forte. A ideia é usar a pressão atmosférica para compactar o laminado durante o processo de cura.
É possível realizar a laminação de peças sólidas ou utilizar esse método para colagem de materiais sandwich. O processo consiste em posicionar os reforços e impregnar manualmente o laminado com resina antes de revesti-lo em uma bolsa plástica, que é conectada a uma bomba de vácuo usada para remover o ar existente dentro da cavidade do molde. Para esse processo pressões entre 0,4 e 0,6 atm são suficientes.
Esquema de laminação a vácuo
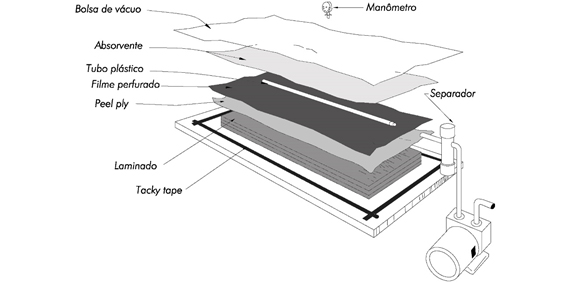
Entre o laminado e a bolsa de vácuo há alguns outros materiais descartáveis essenciais para o sucesso do processo. A começar pelo tecido de poliamida, chamado de peel ply, posicionado em contato direto com o laminado e que possui a função de desmoldante e facilita a retirada dos demais materiais descartáveis após o processo de cura. Acima do peel ply deve ser colocado um filme perfurado, usado para deixar passar ou bloquear a passagem de resina, já que normalmente se utiliza umva quantidade de 3% a 5% maior de resina do que o projetado para facilitar a impregnação inicial e que deve ser retirada durante a aplicação de vácuo.
Em sequência, é posicionado um material absorvente, chamado breather, que tem a finalidade de absorver a resina que que o filme perfurado deixou passar e homogeneizar a distribuição de vácuo. Finalmente a bolsa de vácuo fecha o envelope e deve ser fixa no molde com a tacky tape, uma fita emborrachada dupla face que tem cerca de 12 mm de largura.
Todos os materiais descartáveis devem ter resistência a temperatura e aos solventes emitidos pelas resinas durante o processo de cura exotérmica. Para resinas que curam a temperatura ambiente, os materiais devem ser especificados para uma operação mínima de 80°C.
Como a impregnação dos reforços deve ser feita de forma manual, dependendo das dimensões do laminado esse processo toma bastante tempo. Por esse motivo é preciso utilizar uma resina com gel time alto, normalmente epoxy, o que aumenta o custo do processo.
Apesar do custo dos materiais descartáveis, da bomba de vácuo e da resina, o processo é capaz de entregar um teor de fibra de cerca de 50%, maior que os 40% da laminação manual e da faixa de 20 a 30% obtida pelo spray-up. Por esse motivo a estrutura fica mais leve e tem aumentos consideráveis nas propriedades mecânicas. Além, é claro, de que o uso de vácuo para compactação das fibras também diminui a quantidade de vazios e melhora a qualidade do laminado.