O último post do blog abordou o tema de cura das resinas termofixas e destacou a importância de sempre buscar a cura total durante o processo de laminação, apesar disso se tornar complicado ao passo que conforme as ligações se formam, o movimento das cadeias poliméricas é limitado e o avanço da cura é restringido.
Se a laminação for realizada em temperaturas ambientes de cerca de 25°C e utilizar uma proporção adequada de catalisadores ou endurecedores, é comum que o grau de interligação alcançado varie entre 80% e 90%. Depois de um período de dois a quatro dias, o grau de cura pode chegar sozinho até cerca de 95%, mas não chegará perto do ideal de 100%. Para isso, é necessário adicionar uma fonte externa de calor para que seja possível se realizar o processo de pós-cura.
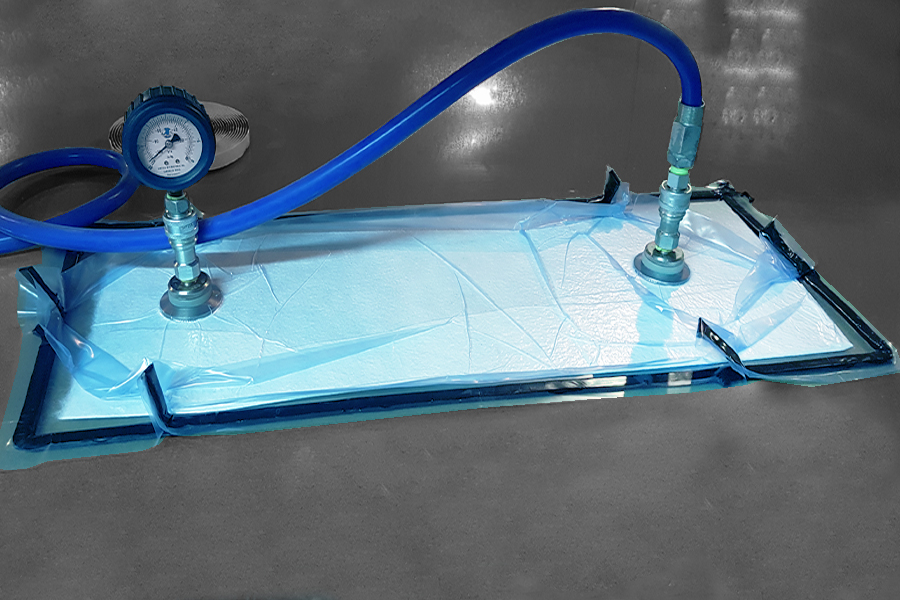
Existem algumas maneiras para determinar qual é o grau de cura de um laminado, como pela exotermia ou estimando o estireno residual no caso de resinas poliéster. No entanto, o método mais simples e que mais se adequa à realidade de um estaleiro é a determinação do grau de cura por meio da Dureza Barcol. Embora a dureza final não determine fielmente o grau de interligação, o método é simples e pode ser implementado na linha de produção de qualquer fábrica. O durômetro Barcol mede a resistência que a resina oferece à penetração de uma agulha padrão comprimida com uma pressão normalizada. Quanto maior a dureza, maior o grau de interligação.
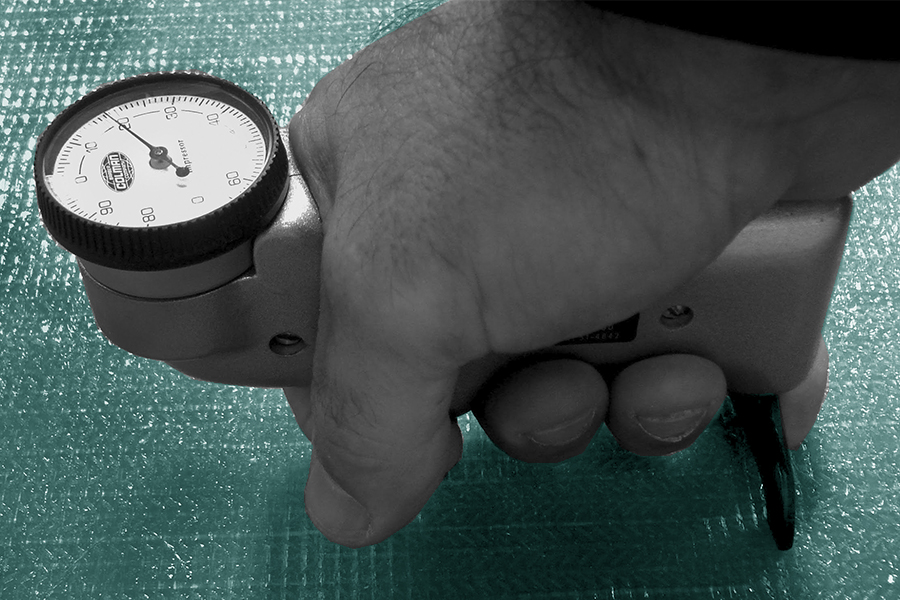
Uma característica chave tanto do processo de cura como das condições de operação da resina é a temperatura de transição vítrea, normalmente chamada de TG. Essa temperatura marca o ponto que divide o estado em que as ligações cruzadas continuam a se formar e o de repouso molecular. Acima da TG as moléculas ainda podem se mover, abaixo elas ficam em repouso e o processo de cura não evolui.
Além disso, quando colocada em temperaturas acima da TG durante o ciclo de vida do laminado, a resina adquire um aspecto borrachoso. Isso é particularmente preocupante em resinas epoxy com baixas temperaturas de transição vítrea, que podem ser alcançadas simplesmente pelo calor gerado durante períodos de exposição solar, fazendo com que os laminados sofram um tipo de “amolecimento”.
O processo de pós-cura é capaz de aumentar a TG ao mesmo tempo que permite aumento do grau de interligação da resina, possibilitando que o grau de cura se aproxime de patamares próximos a 100%. O princípio do processo é que, após o processo de vitrificação que impede o progresso do processo de cura, uma fonte externa fornece calor o suficiente para que o laminado seja aquecido acima da TG para que as interligações sejam retomadas até alcançarem outro patamar de vitrificação, caracterizado por outra temperatura de transição vítrea. Então outro aquecimento avança a interligação para um patamar ainda mais alto e assim sucessivamente até a cura plena.
É sempre ideal seguir as orientações dos fabricantes das resinas termofixas, mas em geral o processo de pós-cura é feito somente após que todo o ciclo de cura em temperatura ambiente acontece. Se o método de laminação utilizado tiver o auxílio de vácuo, este deve ser mantido antes e durante a pós-cura, que se inicia apenas após o laminado estar em temperatura ambiente por duas horas.
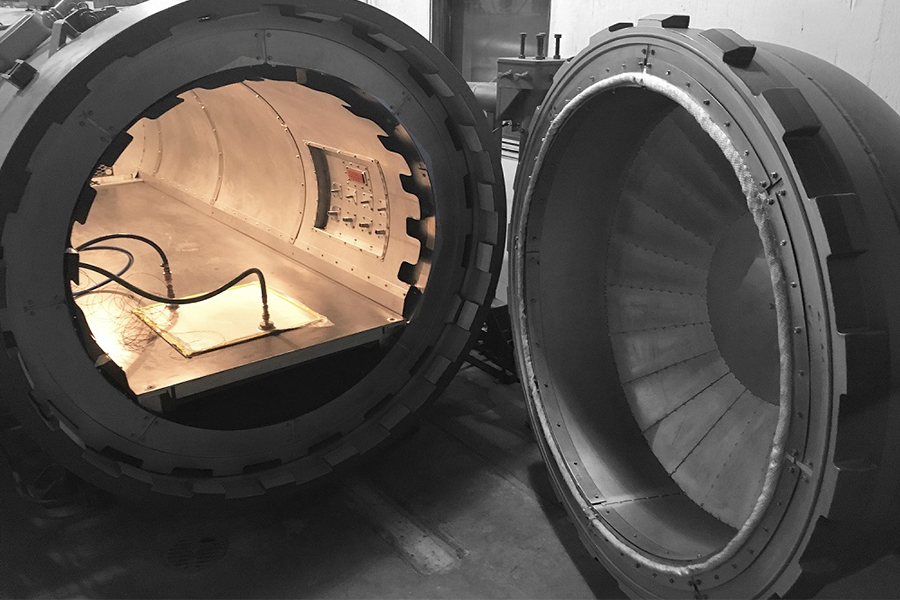
É necessário então elevar a temperatura de forma controlada, com uma taxa de aproximadamente 1°C/min. Quando alcançar TG, deve-se estabilizar a temperatura por uma hora para que a temperatura superficial da peça se estabilize. Depois desse período, inicia-se novamente um período de subida de 1°C/min. Ao chegar em um novo patamar de vibração, deve-se estabilizar a temperatura por 5 horas e, após esse período, é interessante voltar a temperatura ambiente também com uma taxa de resfriamento entre 1°C/min e 2°C/min, se a infraestrutura permitir. O ciclo de temperatura de um processo de pós-cura de uma resina epoxy é apresentado no gráfico abaixo.
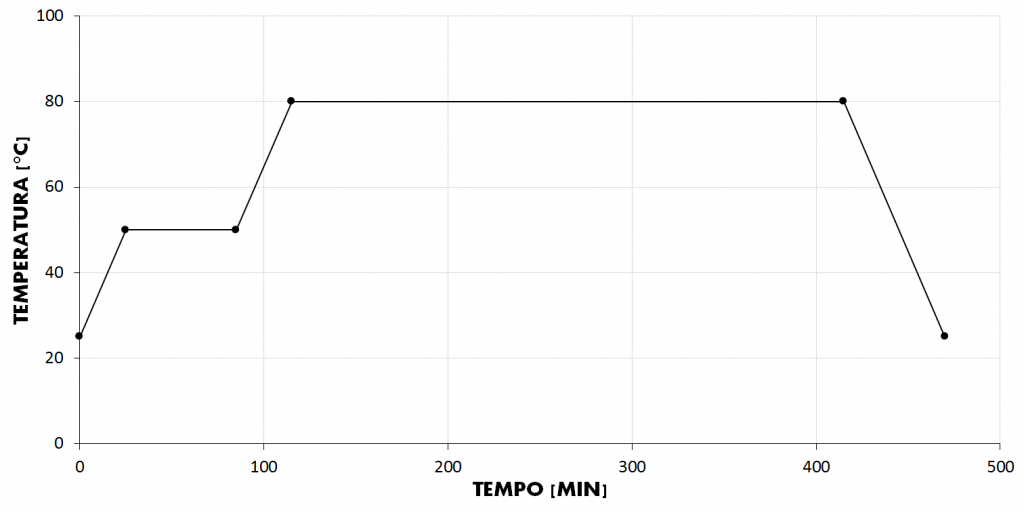
A fonte externa que fornece calor pode ser uma manta térmica ou uma estufa. Alguns construtores tentam fazer pós-cura por meio da exposição solar, mas esse tipo de procedimento não fornece o controle nem o tempo de exposição necessários a uma temperatura alta e constante o suficiente para realização do processo descrito.
O objetivo do processo de pós-cura, portanto, é aumentar o grau de cura das resinas termofixas que exercem o papel de matriz nos materiais compostos. Por conta disso, é capaz de melhorar as propriedades mecânicas dos laminados, além de aumentar a faixa de temperatura de operações do laminados ao aumentar a temperatura de transição vítrea, bastante conhecida como TG.