Uma das formas de se identificar as quantidades de fibra e resina dentro de um laminado e conseguir estimar os valores de resistência a tração, compressão, flexão e seus módulos de elasticidade é pelo cálculo de fração de volume e peso em um laminado. A estrutura básica de laminação é constituída por uma fibra de reforço, que pode ser vidro, aramida ou carbono e seus híbridos com uma matriz polimérica, seja ela poliéster, estervinílica ou epoxy.
Cada um destes materiais exibe uma densidade e um limite teórico para ser usado em conjunto, de modo que seja possível utilizar o menor valor possível de resina, mas ainda garantindo a impregnação de todas as fibras. Cada fibra apresenta uma característica diferente de “molhabilidade” em função do seu diâmetro e da compatibilidade com a resina. Quanto menor o diâmetro do filamento, maior a necessidade de usar resinas com melhor propriedade de adesão e maior pressão de vácuo sobre o laminado para que todas as fibras fiquem impregnadas e transmitam melhor os esforços entre si.
A fração em peso geralmente é aquela que o construtor usa para determinar a quantidade de fibra e resina em seu laminado, também conhecida como teor de fibra. Se o peso de cada produto dentro do laminado for conhecido, é possível então identificar a fração em volume da fibra e da resina por meio de formulações simples. A massa total, assim como o volume do laminado, pode ser descrita matematicamente como:
Equação 1

Equação 2

Onde V se refere ao volume, M a massa, o subscrito f a fibra, o m se refere a matriz de resina e o c ao composto inteiro. Dividindo os dois lados das equações por MC e VC, respectivamente, podemos obter as frações mássicas e volumétricas:
Equação 3
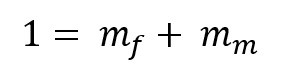
Equação 4
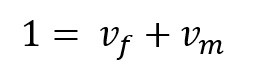
As frações mássicas e volumétricas são números que variam entre 0 e 1 que indicam quanto espaço ou massa elas representam no todo do laminado. Sabe-se que as frações mássicas são fáceis de se medir antes da fabricação do laminado com uma balança comum, por isso são muito úteis para calcular a densidade do composto. No entanto, a fração volumétrica é a variável utilizada para prever as propriedades do composto com base na micromecânica, por isso é importante ter uma forma de obter essa informação.
É possível identificar a fração em volume da fibra e da resina por meio da Equação 5, onde os subscritos f e m são intercambiáveis.
Equação 5
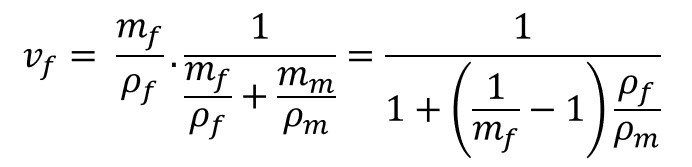
Na Figura 1, é possível encontrar a relação descrita pela fórmula anterior em um gráfico que diz respeito a três tipos de fibra muito comuns.
Figura 1 – Fração em volume em função da fração em peso
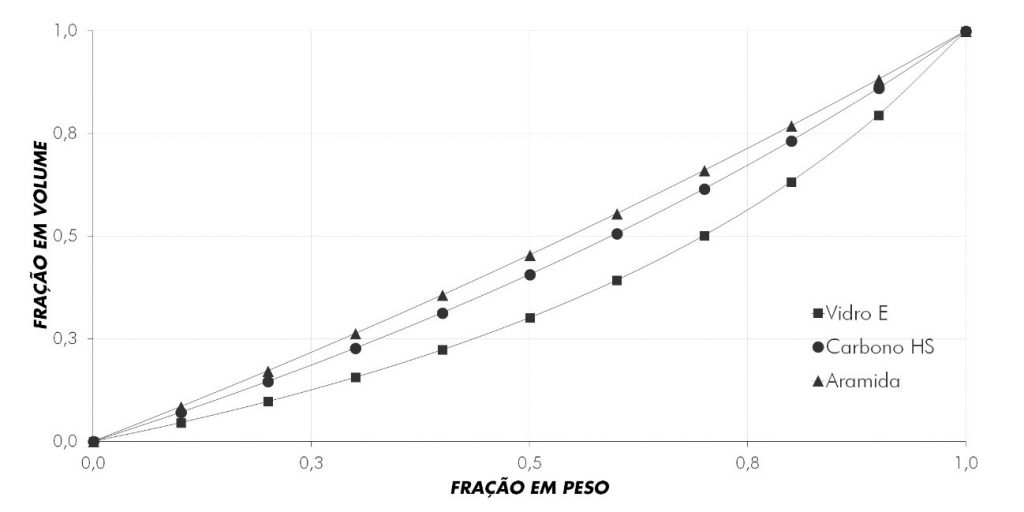
Como o principal fator na resistência e no módulo de elasticidade está associado à quantidade de fibra e resina dentro do laminado, no geral, quanto mais fibra, mais resistente é o laminado. Entretanto, uma quantidade reduzida demais de resina pode gerar um laminado seco e frágil, com baixa resistência a compressão, e uma quantidade grande demais irá produzir um laminado pesado e não econômico
Com isso, mesmo que o objetivo final fosse produzir um laminado com 100% de teor de fibra, esse número nunca poderia ser atingido, pois por melhor que as fibras fossem acomodadas, alinhadas e compactadas, ainda assim haveria espaços a serem preenchidos com resina. Isto só aconteceria se o laminado fosse unidirecional e todas as fibras fossem hexagonais e todas se tocassem por meio das arestas. Como as fibras têm uma forma quase circular, o agrupamento de três filamentos, por exemplo, iria criar um espaço vazio entre eles, proporcional ao diâmetro do filamento. Assim fibras com um menor diâmetro de filamento tendem a ter uma fração em volume maior e por esse motivo uma resistência maior.