Independente do regime de navegação da embarcação, seja planeio ou deslocamento, a interseção entre os painéis do fundo e do costado é um ponto crítico da estrutura. É ali que ocorre a transferência de tensões entre o fundo e o costado que podem variar em até 500% em embarcações de planeio. Por esta razão, o construtor deve buscar o arranjo mais rígido possível para proporcionar uma transição contínua das tensões geradas pelas cargas de impacto do fundo.
A primeira opção é apresentada na Figura 1, onde ambos os painéis, do fundo e costado terminam com a espuma em chanfro de 30° e deixa o plano do chine sólido com uma espessura adicional provida pelo overlap entre os tecidos do fundo e do costado. Nesta configuração, deve ser acrescentados tapes de 45° com overlap progressivo no fundo e costado para aumentar o momento de inércia da área sólida.
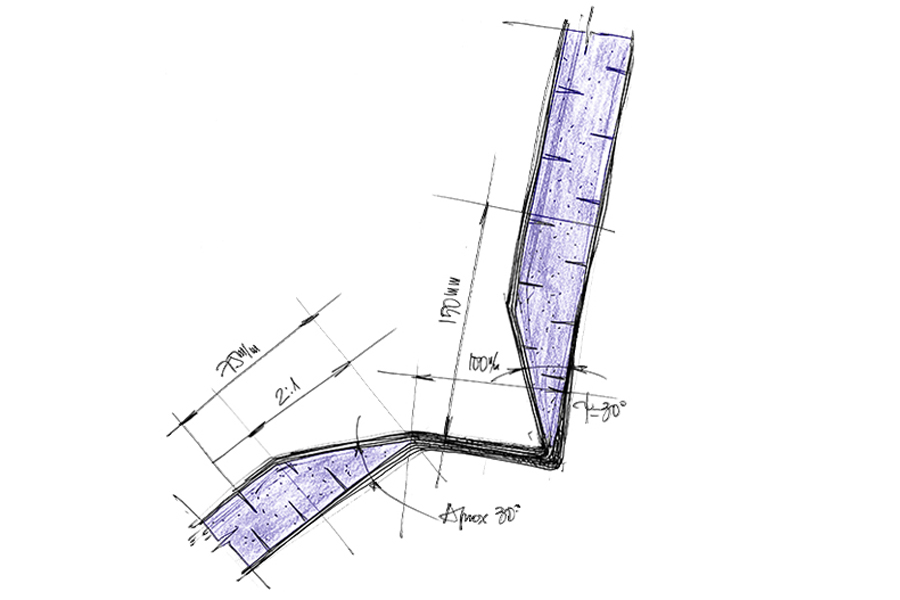
A Figura 2 apresenta uma variação, utilizando a espuma do costado montada diretamente sobre o plano do chine e o fundo é terminado com a espuma em chanfro. Nesta configuração também é necessário a adição de camadas de superposição no chine de modo a aumentar o momento de inércia da área sólida.
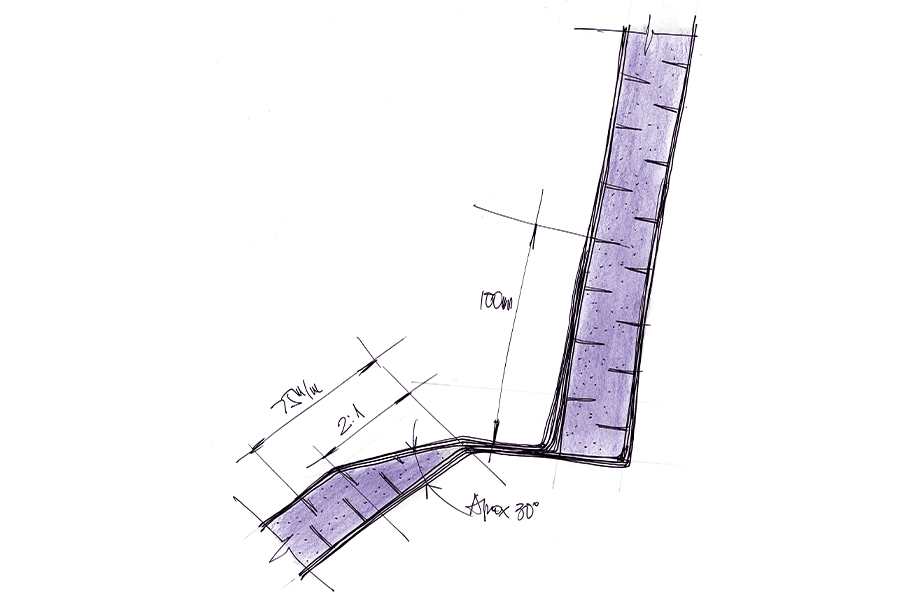
Por fim, o próximo detalhe é o que promove maior rigidez à junção entre os laminados do fundo e do costado, pois mantém o momento de inércia constante ao longo da passagem das tensões entre os dois planos. Neste detalhe ainda é adicionado um filete de espuma de PVC com um laminado na trama de 45° para criar uma transição perfeita do fluxo de tensões.
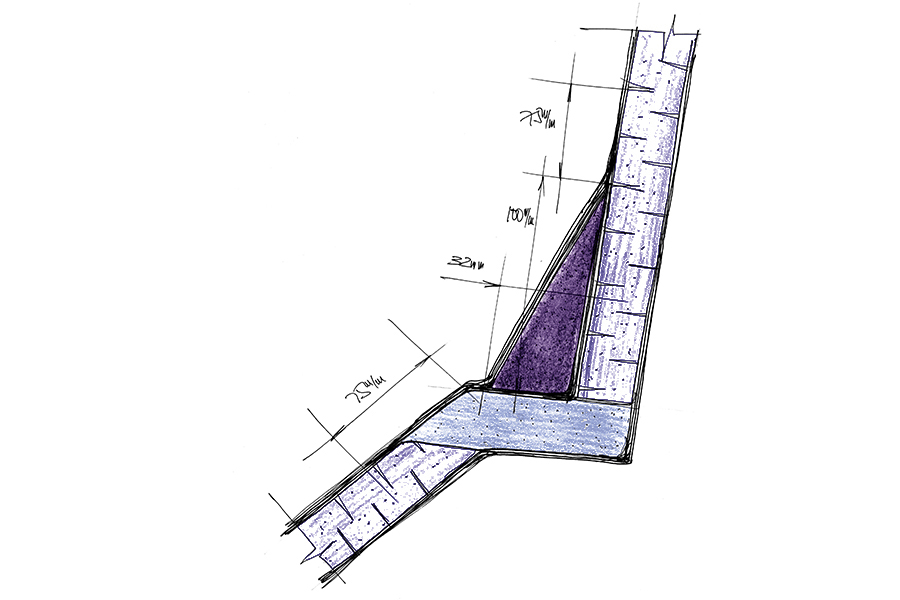
Esses são os parâmetros que o construtor deve ter em mente ao planejar a fabricação de um casco e algumas opções de configuração. É essencial ter ciência dessas variáveis e conhecerem a melhor maneira de construir esses detalhes para garantir a segurança e eficiência da embarcação.