Antes da aplicação da pintura de base ou primer é preciso lixar o casco e fazer a preparação adequada independentemente do tipo de tinta a ser utilizado. O lixamento serve para corrigir imperfeições, retirar a pintura antiga e também melhorar a ancoragem, ou seja, aumentar a aderência da camada de tinta que promoverá o acabamento final.
Passada esta etapa e corrigidas pequenas rachaduras e trincas, caso existam, aplica-se a pintura de fundo. O número de demãos e a espessura delas depende muito do produto a ser utilizado, do fabricante dos produtos e da diluição. Logo, é imprescindível que as recomendações do fabricante sejam seguidas rigorosamente, caso contrário, o resultado final poderá ficar comprometido. A preparação do casco é outro fator vital na hora da pintura, para que se evite qualquer possibilidade da tinta se desprender do casco.
O trabalho de aparelhamento com lixa é um mal necessário e infelizmente quanto mais tempo for dedicado a essa tarefa, melhor será a aparência do barco. O trabalho de lixamento e preparação realmente dá muito trabalho! Danos à saúde estão envolvidos nesse trabalho, por isso, espera-se que o construtor siga as recomendações de segurança e utilize sempre máscara de proteção contra inalação de poeira e os EPIs indicados.
Ao trabalhar no aparelhamento com lixa é crucial atentar-se para não provocar buracos ou irregularidades na superfície. Caso enfrente esse tipo de problema, preencha com massa até tudo ficar nivelado para facilitar o trabalho de acabamento. Quando estiver utilizando a massa para nivelamento, procure sempre produtos que produzam pouca distorção térmica e, mesmo assim, não tente preencher irregularidades mais acentuadas de uma vez.
As lixas normalmente são numeradas e vão do número 24 (mais grossas) a 2000 (mais finas). As de grãos, na faixa entre 24 e 150, são de óxido de ferro e devem ser usadas a seco. As outras, de 100 a 2000 são de óxido de alumínio e devem ser utilizadas com água. Para superfícies com pintura antiga, é recomendado usar lixas na faixa de 60 a 220. Inicie com lixamento a seco e termine com lixas d’água.
Note também, que existem lixas específicas para o uso em superfícies de madeira e metais. Ao lixar peças de madeira, o acabamento mais suave pode ser obtido com uma lixa manual após usar uma com a máquina. Lembre-se que qualquer quantidade de tinta ou verniz nunca conseguirá esconder um acabamento irregular.
Para um trabalho de primeira classe com verniz, a madeira deve estar 100% lisa. Jamais utilize uma lixa mais grossa do que o necessário, você estará gastando tempo e material. Sempre comece o trabalho com lixas mais grossas e termine com uma mais fina e nunca o contrário. Ao passar uma lixa para outra, limpe a superfície para poder acompanhar e avaliar o desenvolvimento do trabalho de acabamento.
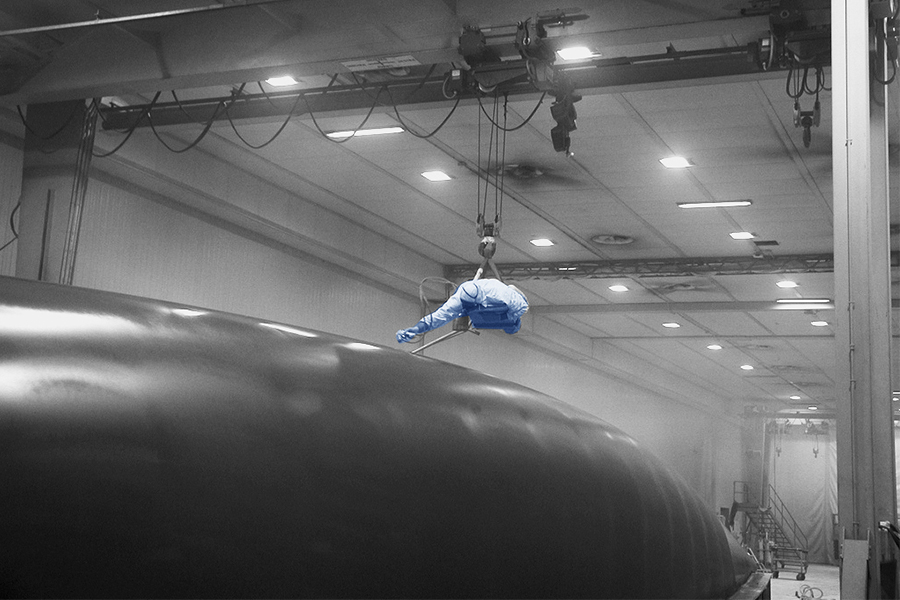
Subempreitar o trabalho de preparação do casco é definitivamente uma das maiores dores de cabeça de qualquer construtor. Nenhum pintor gosta de perder tempo lixando qualquer superfície, eles sempre arranjarão um jeito de aplicar logo a tinta e culpar a pintura antiga pelos defeitos aparentes. Isto é um erro grave que se perpetua em todos os estaleiros de reparo no mundo todo. Existem exceções, mas são raras. O trabalho de preparação requer paciência e, acima de tudo, técnica.