É muito comum que posts no blog destaquem que a combinação de resinas poliéster e espumas de PVC são a opção de melhor custo benefício para construção náutica. As células fechadas desse tipo de núcleo contornam o ponto negativo de que as resinas poliéster possuem baixa resistência química e o conjunto entrega excelentes propriedades mecânicas para embarcações que navegam em regime de planeio. Sendo a resina poliéster um elemento tão importante da construção náutica, é necessário explicar como ela é formulada e quais são os principais tipos a disposição do construtor.
As resinas poliéster são formadas a partir de um processo chamado de esterificação, que é a reação química entre um ácido e um álcool que resulta na formação de um éster e uma molécula de água. O resultado dessa reação é uma pasta viscosa que é misturada com um solvente chamado estireno, que torna a resina um líquido e acaba tomando parte na molécula final da matriz polimérica após a cura.
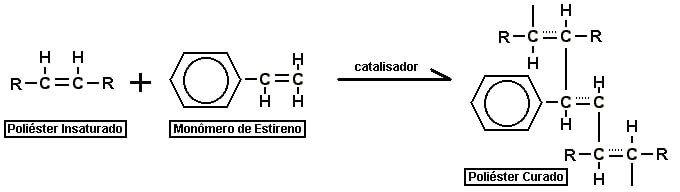
O monômero de estireno é um tipo de molécula que possui uma estrutura química chamada benzeno, ou anel aromático. Como indicado na Figura 1, a junção do poliéster insaturado com o monômero pela ação de um catalisador forma o poliéster curado. A posição das cadeias de poliéster em relação ao anel aromático dá origem à diversos tipos de resina poliéster, dentro os quais vale destacar as resinas ortoftálicas e isotftálicas.
As ortoftálicas são muito utilizadas para laminação, mas suas propriedades mecânicas e químicas são bastante pobres porque é muito difícil obter polímeros de alto peso molecular já que suas cadeias são bastante curtas. Na prática, isso significa que esse tipo de resina possui um preço baixo, mas vai permitir que a água ataque suas moléculas e permeie o laminado, causando a delaminação ou separação física da resina com a fibra ou com o material de núcleo.
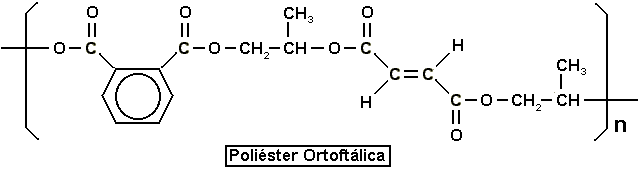
Uma solução com melhores propriedades são as resinas poliéster isoftálicas. Suas móleculas, apresentadas na Figura 3, são mais longas e permitem uma absorção melhor dos impactos e, consequentemente, melhores propriedades mecânicas. Em adição a isso, elas apresentam maior resistência térmica, o que significa um aumento de Tg e diminuição de fenômenos como o print-thru.
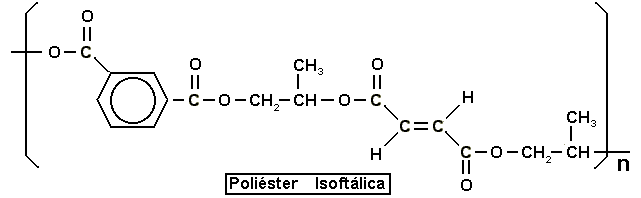
Como a diferença do custo dessas duas opções não é muito discrepante e as propriedades são significativamente melhores, as resinas poliéster isoftálicas são muito utilizados para construção náutica. Em combinação com Neo Pentil Glicol, sua resistência química é inclusive boa o suficiente para formulação de gelcoats.
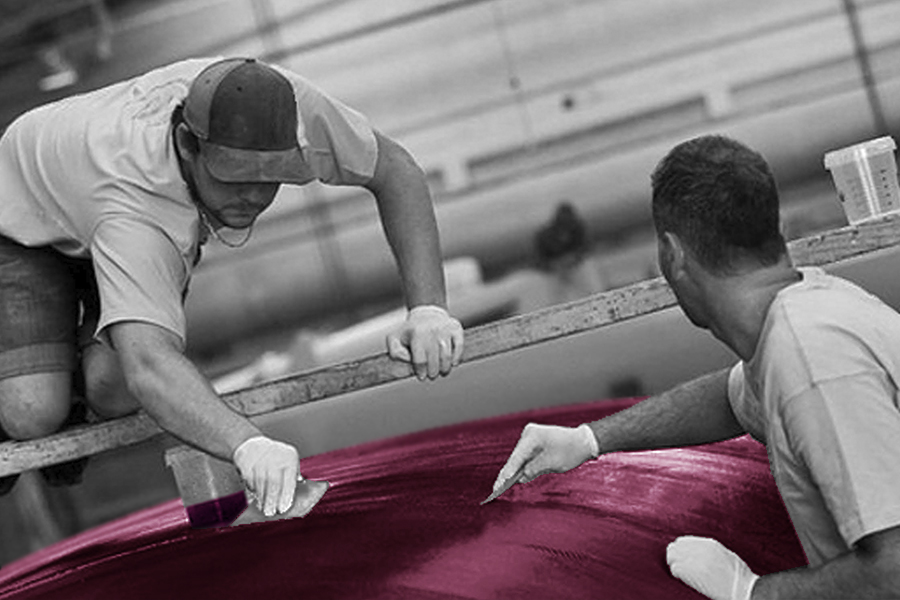
A definição de resistência química em uma resina termofixa, assim como do fenômeno de hidrólise, será feita no post da próxima semana. Para saber mais sobre os diferentes tipos de resina poliéster, é possível consultar o livro Manual de Construção de Barcos.