O processo de cura de resinas termofixas pode ser definido como um fenômeno exotérmico que representa a transformação da resina do líquido viscoso em que ela é comercializada para o estado sólido em que ela exerce o papel da matriz polimérica responsável por transferir os esforços mecânicos às fibras de alta rigidez e resistência.
Sejam amadoras ou profissionais, as construções de embarcações em materiais compostos utilizam majoritariamente as resinas poliéster, estervinílicas e epoxy. As duas primeiras possuem longas cadeias poliméricas diluídas em monômetros de estireno e apresentam o mesmo mecanismo de cura ativada por catalisadores por esse motivo, enquanto a resina epoxy trabalha com endurecedores.
As resinas poliéster e estervinílicas iniciam seu processo de cura a partir da adição de um catalisador de peróxido à sua composição, que tem a função de quebrar as ligações insaturadas das cadeias poliméricas e dos estirenos, formando radicais livres altamente energizados e fornecendo calor à mistura. Calor causa ainda mais agitação das moléculas, acelerando o processo de cura.
Esses radicais livres podem encontrar outros monômeros de estireno ou polímeros de poliéster insaturado. É muito mais provável que eles encontrem monômeros de estireno e formem ligações cruzadas usando esse elemento, que antes fazia o papel de diluente, como uma ponte molecular entre cadeias de polímeros.
A formação dessas ligações cruzadas, que também são chamadas de cross-link, acabam restringindo os movimentos da solução que sai do estado líquido e passa para o estado de gel. O intervalo em que é possível trabalhar com a resina no processo de laminação é compreendido entre o momento da adição do catalisador até a passagem da solução para o estado de gel e é chamado de gel time.
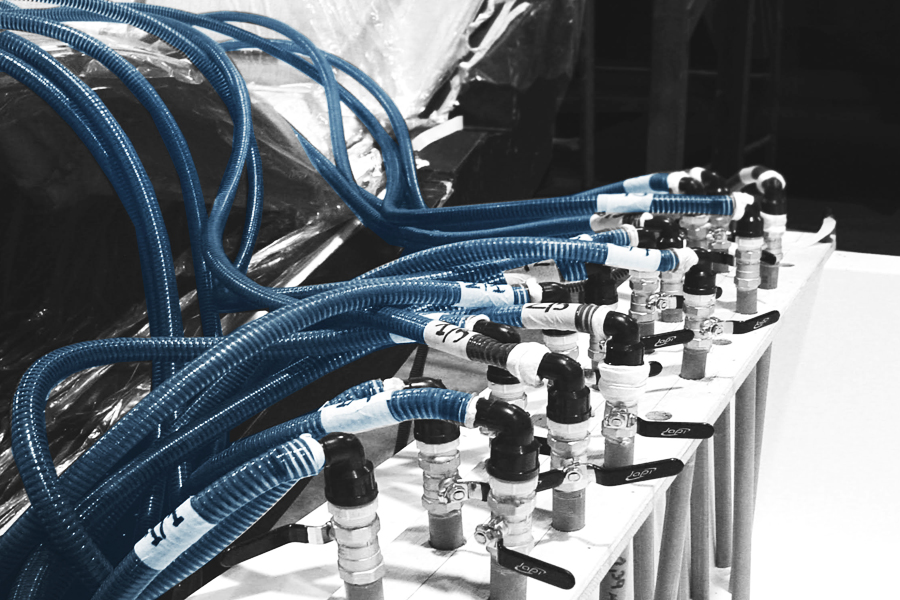
Os catalisadores de peróxido são utilizados em pequenas quantidades, em concentrações que variam entre 0,5% e 2% do peso total de resina. Dependendo da temperatura da resina, eles são capazes de fornecer um gel time entre 20 e 30 minutos, mas com o uso de inibidores é possível alcançar um tempo de trabalho de até 45 minutos.
Esse intervalo pode variar entre 15 minutos e algumas horas quando se trabalha com resinas epoxy, dependendo do endurecedor com o qual se trabalha. Diferente dos catalisadores que possuem apenas a função de quebrar as ligações saturadas e formar radicais livres, os endurecedores utilizados para cura das resinas epoxy fazem parte da composição final da resina. A proporção da mistura também é completamente diferente, e resinas de laminação de alto desempenho acabam por ter proporções de resina e endurecedor em torno de 100:33 ou 100: 25 em peso.
Existem diversos tipos de endurecedores que controlam o gel time e as propriedades finais do laminado, assim como a cinética de cura e o ciclo de processamento da resina. Vale destacar os agentes de cura amínicos e os anidros.
Os agentes amínicos são divididos em aminas alifáticas e aminas aromáticas. As aminas alifáticas são altamente reativas e se encontram em estado líquido e volátil em temperatura ambiente, onde apresentam tempo de gel inferior a 60 minutos. Já as aminas aromáticas são endurecedores de cura a quente bem menos reativos que precisam de temperaturas entre 150°C e 180°C, permitindo um tempo de processamento bem maior. Como podem formar estágios de cura parcial, as aminas aromáticas são bastante utilizadas para a manufatura de prepregs.
Os agentes de cura anidros possuem reatividade ainda menor que as aminas aromáticas, possibilitando um longo tempo de utilização durante o processo. Os processos de cura que fazem uso desses endurecedores são relativamente longos e possuem baixa exotermia e, por isso, eles normalmente são utilizados em conjunto com aceleradores.
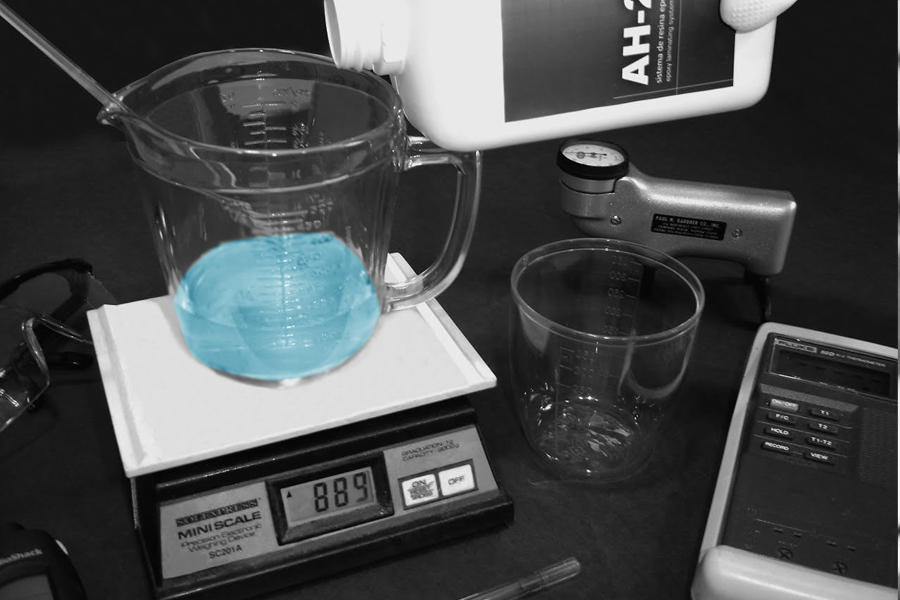
Assim como se busca um grau de interligação de 100% dos radicais livres na cura de resinas poliéster e estervinílicas, é esperado que após a cura das resinas epoxy todos os grupos epoxy tenham reagido com os agentes de cura. Para isso, a estequiometria da mistura epoxy/endurecedor é fundamental.
É importante observar que, diferente da quantidade de catalisador, não é possível alterar a quantidade de endurecedor para acelerar ou retardar o processo de cura. Como esses agentes fazem parte da composição química final da resina termofixa, utilizar a quantidade incorreta de endurecedor pode prejudicas as propriedades mecânicas do laminado e até mesmo inviabilizar o processo de cura de forma permanente.
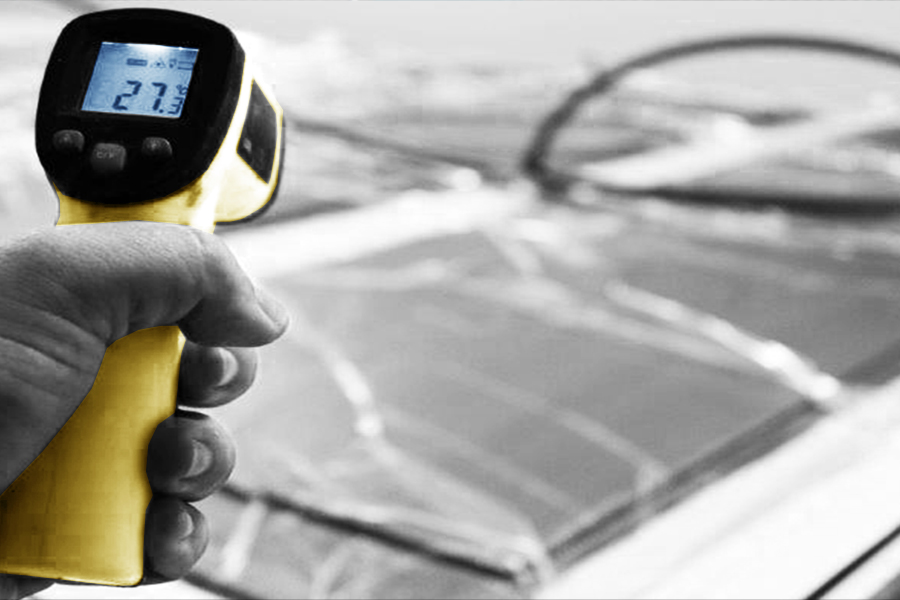
É importante destacar a íntima ligação do processo de cura com o calor, seja ele fornecido por uma fonte externa ou criado por meio da quebra das ligações saturadas e formação dos radicais livres. Nesse contexto é importante sempre pensar que quanto maior a área de troca de calor que a peça tem, mais difícil será a realização do processo de cura.
Ainda com isso em mente, é importante que a resina e o molde se encontrem em uma faixa de temperatura adequada antes do início da laminação, de acordo com as especificações dos fornecedores. Essa faixa de temperatura normalmente fica entre 15°C e 35°C e laminar abaixo desse patamar pode impedir o início da cura e acima pode deixar a resina muito reativa e com um tempo de gel muito curto.
Na próxima semana serão definidos mais alguns parâmetros importantes sobre o processo de cura de resinas termofixas, como a temperatura de transição vítrea e como alcançar níveis de interligação próximos de 100% por meio do processo de pós-cura. Além disso, mais informações sobre o tópico podem ser encontradas nos livros da Coleção Jorge Nasseh.