As vantagens do uso de estruturas sandwich vêm sendo exploradas aqui no blog ao longo das semanas, sobretudo quando as espumas de PVC são utilizadas como material de núcleo. Entre os benefícios do uso deste material é possível destacar o aumento da eficiência estrutural e as células fechadas que impedem a absorção de água.
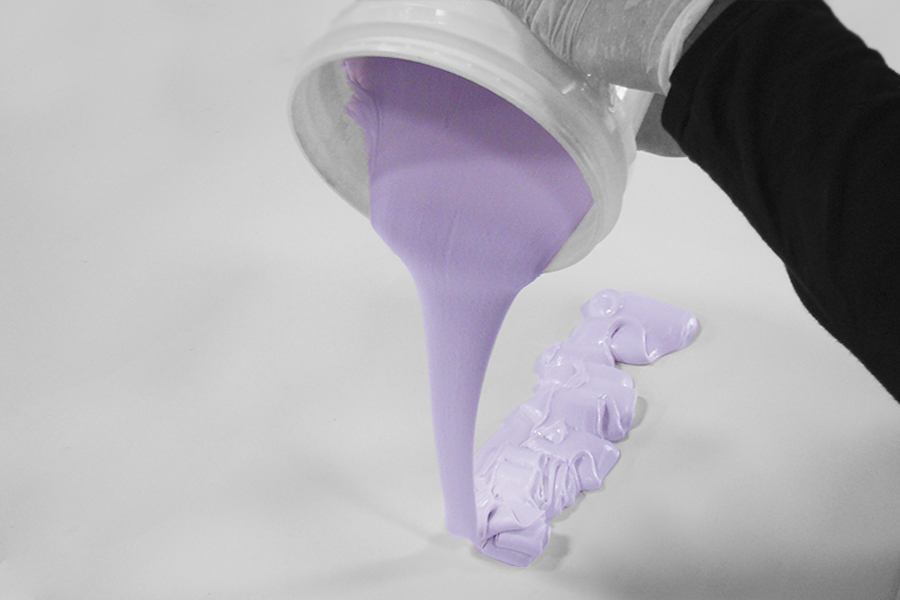
No entanto, a construção das estruturas sandwich possui particularidades. Com o uso de vácuo em processos como o de infusão, é possível consolidar toda a estrutura, as duas faces e o núcleo sandwich, de uma vez. Quando o construtor utiliza dos processos de laminação manual e por vacuum bagging, a melhor estratégia é realizar a consolidação por etapas.
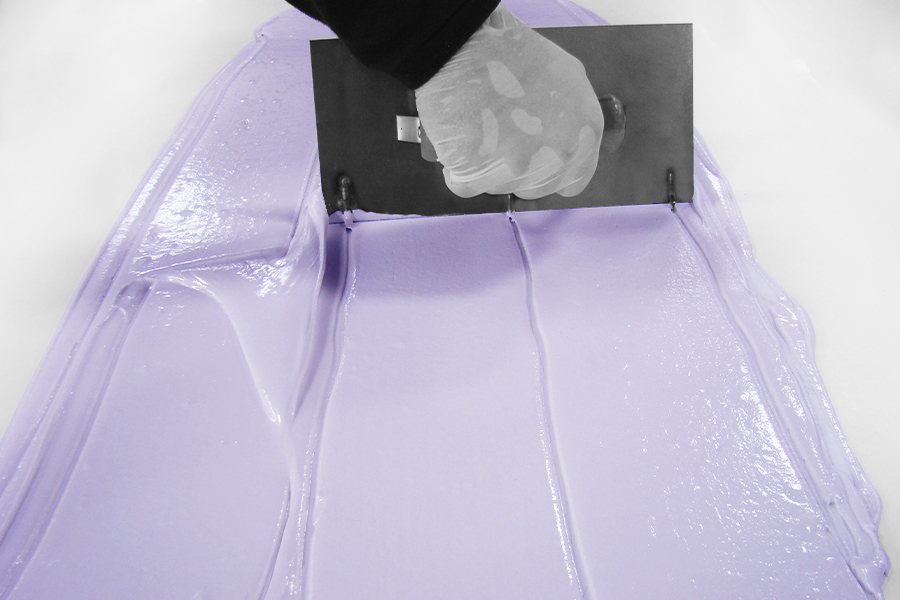
Em ambos os casos, o processo começa com a laminação e cura da face externa que, se necessário, deve passar por um processo de lixamento e limpeza. Para aumentar a produtividade do processo é essencial que as espumas sejam pré-cortadas antes da aplicação do adesivo de colagem.
O adesivo de colagem pode ser a base de resina poliéster ou resina epoxy combinadas com um agente tixotrópico, que pode ser uma mistura de sílica e microesferas. É importante observar que a resina epoxy pode ser utilizada em qualquer ocasião, mas a resina poliéster só pode ser utilizada se a resina de laminação também for de poliéster.
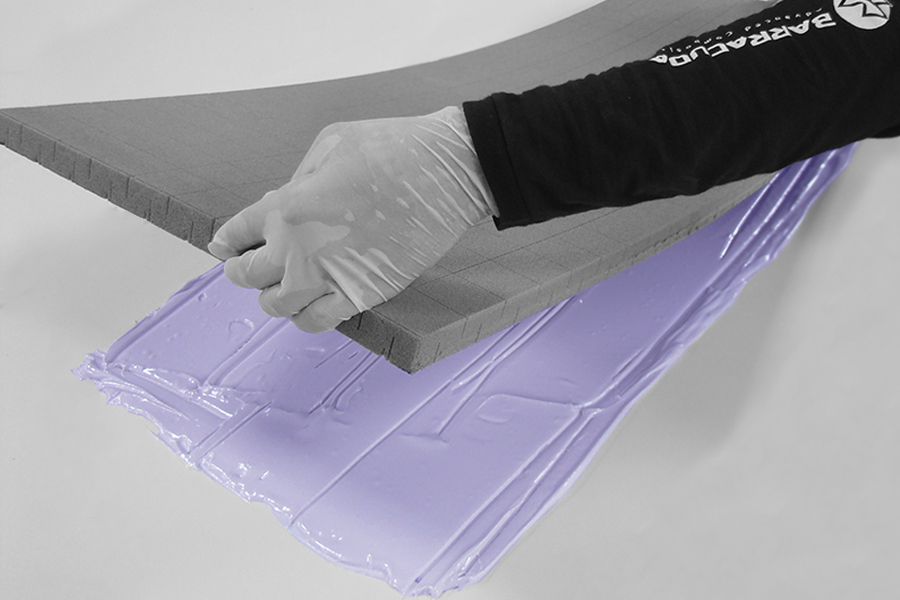
No processo de colagem manual, a placa deve ter corte GS para regiões com curvaturas acentuadas e corte DC para regiões planas. O adesivo de colagem deve ser aplicado em quantidade suficiente para preencher todos os espaços vazios e depois da colocação da espuma, ela deve ser compactada como um rolo vibrador até que seja possível ver massa de colagem na face oposta da espuma.
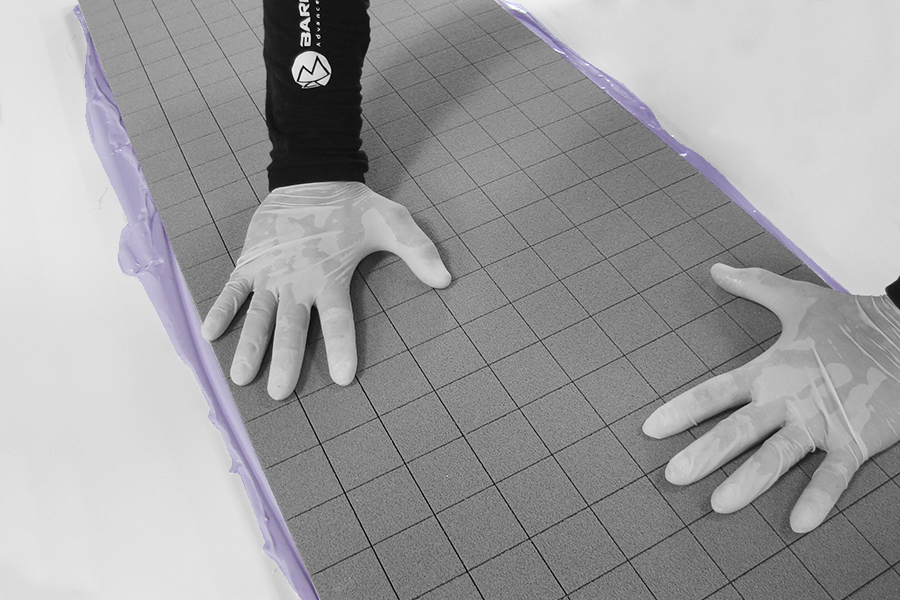
Garantir que não há espaços vazios fornece uma adesão de boa qualidade e não deixa espaços para entrada de água e umidade, que pode causar delaminações e comprometer a estrutura do laminado. Além disso, deve-se evitar espaços vazios como um todo no laminado, pois diminuem a qualidade estrutural da peça ao criar concentradores de tensão que podem propagar defeitos.
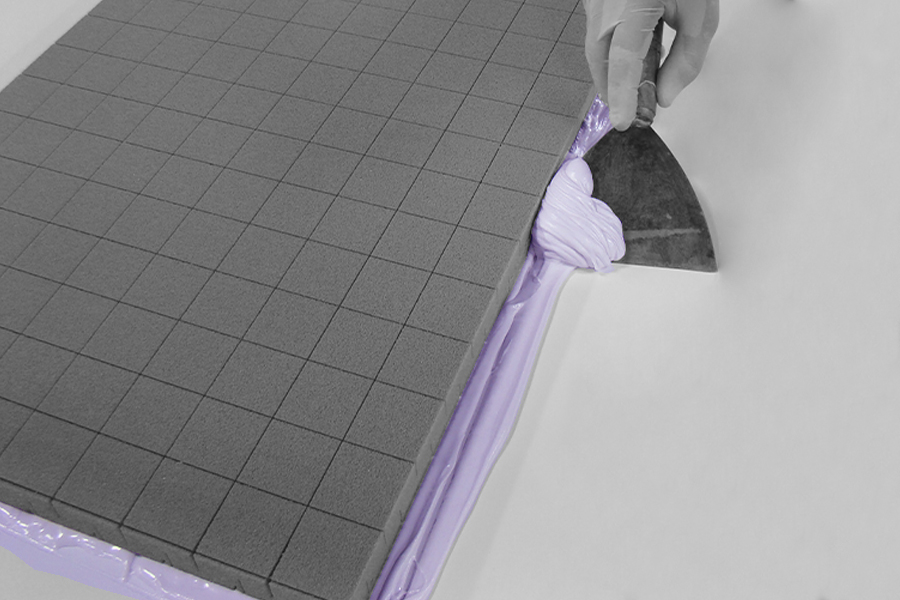
No processo de colagem manual utilizando o compactador pneumático o adesivo deve ser aplicado apenas na região em que a espuma está sendo colada. No caso da colagem a vácuo a espessura do filme adesivo deve ter entre 1 e 2 mm e ser deve ser aplicado em toda a superfície que se deseja realizar a colagem. Uma espátula dentada ou calibrada pode ser utilizada para garantir que a espessura do adesivo seja homogênea.
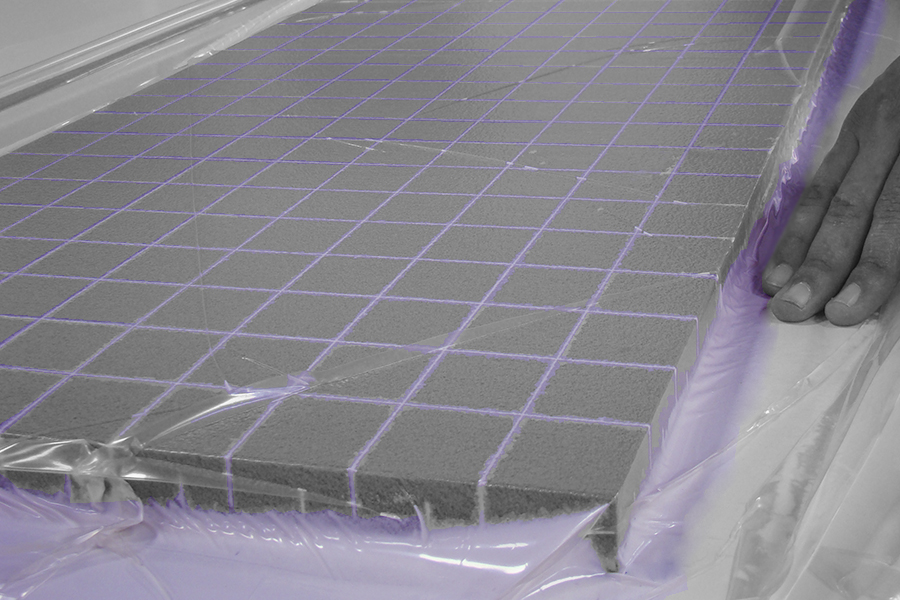
É importante que o tempo de cura do adesivo seja suficiente para sua aplicação, posicionamento das placas e posterior aplicação do vácuo. Como a utilização de vácuo ajuda a conformar a espuma, em regiões com curvaturas suaves é possível utilizar placas planas apenas com cortes e perfurações para permitir a passagem do ar entre as duas faces. Placas GS ainda devem ser utilizadas em regiões com curvaturas mais acentuadas.
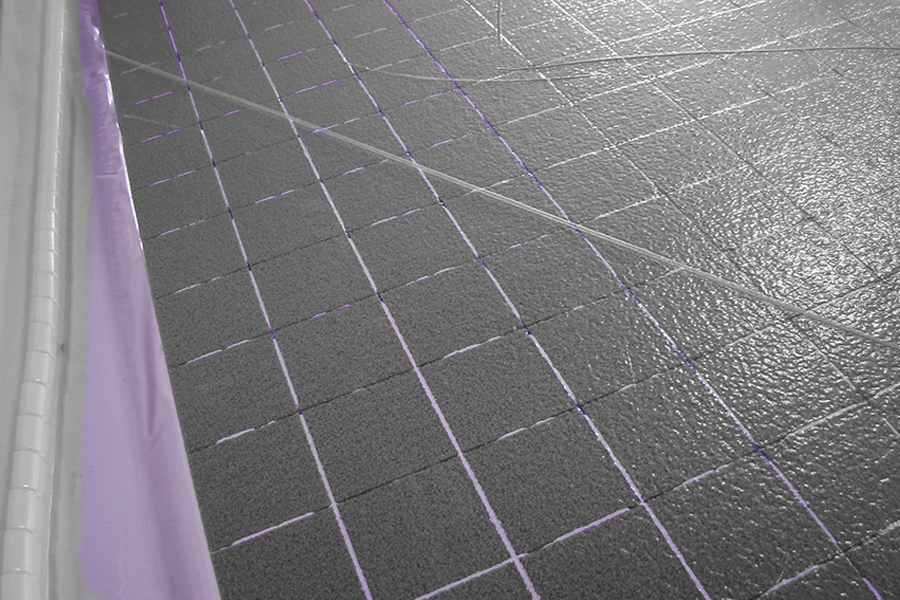
Depois do posicionamento das espumas, ainda é necessário colocar uma camada de peel ply, um filme perfurado e breather antes de cobrir tudo com a bolsa de vácuo, que deve ter uma área 20% maior que a área de colagem para garantir uma boa acomodação. Tacky tape deve ser utilizada para selar a bolsa completamente antes da aplicação do vácuo, garantindo que não haja vazamentos. A pressão de colagem deve ficar entre 0.6 e 0.8 atm. Após a cura completa do adesivo é possível retirar os materiais de vácuo que devem sair com facilidade pelo uso do peel ply.
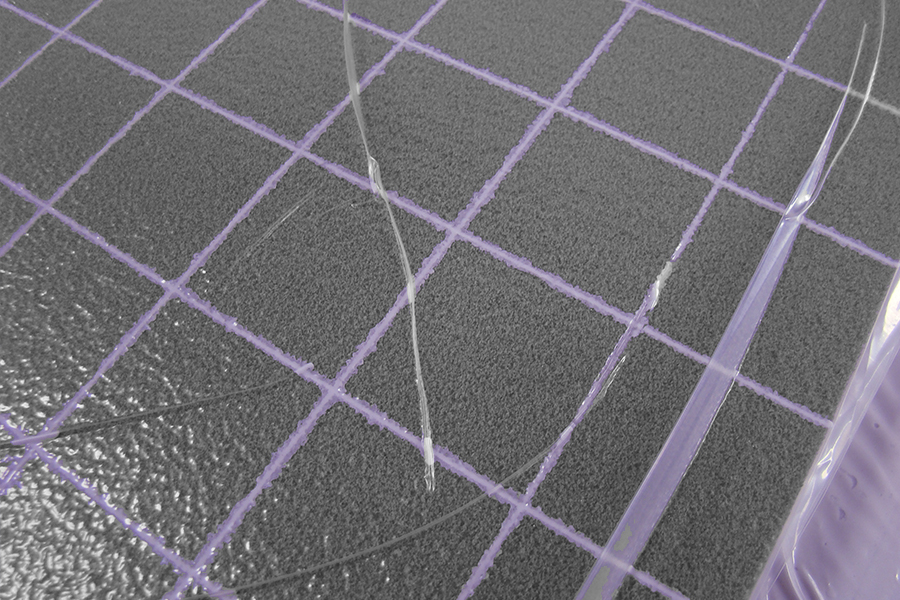
E dessa forma é possível realizar a consolidação do núcleo utilizando processo de laminação manual ou a vácuo. A peça estará então pronta para a laminação da face externa. Para melhorar a ancoragem da face seguinte, assim como feito com a laminação dos reparos, sugere-se a utilização de tecidos combinados ou uma camada de manta entre o núcleo e próximo tecido.